下载PDF
Digital Transformation in Meat Processing: A Case Study of ELPOZO ALIMENTACIÓN
技术
- 功能应用 - 企业资源规划系统 (ERP)
适用行业
- 生命科学
- 包装
适用功能
- 采购
- 质量保证
用例
- 库存管理
- 视觉质量检测
服务
- 测试与认证
挑战
ELPOZO ALIMENTACIÓN 是一家拥有超过 65 年经验的肉类加工公司,面临着运营数字化转型的挑战。该公司隶属于欧洲最大的农产品控股公司之一 Grupo Fuertes,致力于为利益相关者创造价值,并看到了数字化转型的必要性。最初的步骤包括克服变革阻力、定义角色和澄清流程目标。他们需要一个智能业务流程管理套件 (iBPMS),能够编排敏捷的工作流程来处理涉及多人的复杂流程,并整合 Grupo Fuertes 旗下所有公司的流程。
关于客户
ELPOZO ALIMENTACIÓN 是一家拥有超过 65 年经验的肉类加工公司。它是欧洲最大的农产品控股公司之一 Grupo Fuertes 的一部分。该公司致力于生产新鲜、加工和腌制肉制品。基于再投资和持续改进的战略,ELPOZO ALIMENTACIÓN 经历了持续增长。其年销售额超过 11 亿欧元,公司直接雇佣了 5,000 多名员工,此外还通过其业务活动创造了 23,000 多个间接就业岗位。公司致力于卓越、努力、激情、工作、亲密、谦逊、正直和常识等价值观。
解决方案
ELPOZO ALIMENTACIÓN 实施了 AuraQuantic 数字平台来组织和集中 Grupo Fuertes 的所有流程。实施包括三个操作流程:新产品发布、简化发布和新材料。新产品发布流程于 2008 年首次实施,涉及从商业数据收集到产品制造的多个阶段。简化的启动流程创建于 2011 年,用于与现有产品类似或进行修改的产品。 2015 年启动的新材料流程控制了涉及采购新材料的管理。 Grupo Fuertes 还实施了 SAP 来统一管理流程,从而能够创建与采购相关的新 AuraQuantic 流程类。新流程开发的增长得益于管理层、负责 AuraQuantic 的 Grupo Fuertes 团队的兴趣以及 AuraQuantic“SAP 连接器”模块的发布。
运营影响
数量效益
相关案例.
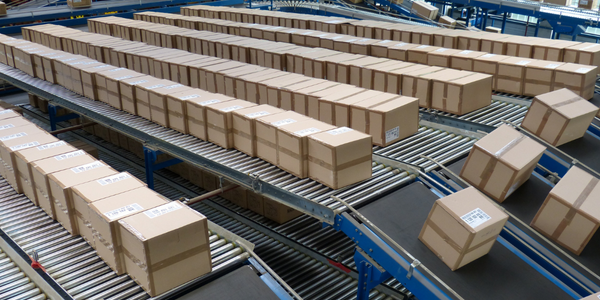
Case Study
IoT Data Analytics Case Study - Packaging Films Manufacturer
The company manufactures packaging films on made to order or configure to order basis. Every order has a different set of requirements from the product characteristics perspective and hence requires machine’s settings to be adjusted accordingly. If the film quality does not meet the required standards, the degraded quality impacts customer delivery causes customer dissatisfaction and results in lower margins. The biggest challenge was to identify the real root cause and devise a remedy for that.
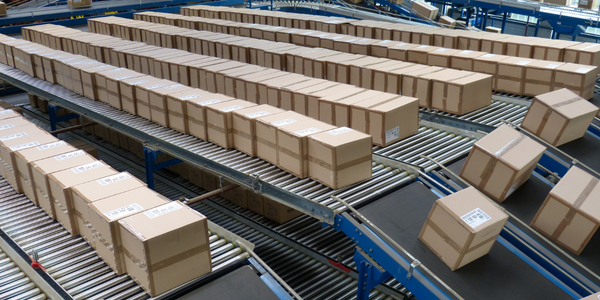
Case Study
Zenon the Ideal Basis for An Ergonomic HMI
KHS develops and produces machines and equipment for filling and packaging in the drinks industry. Because drinks manufacturing, filling and packaging consist of a number of highly complex processes, the user-friendly and intuitive operation of equipment is increasingly gaining in significance. In order to design these processes as simple as possible for the user, KHS decided to introduce a uniform, transparent and standardized solution to the company. The HMI interface should meet the requirement for people with different qualifications and enable them to work on a standard platform.
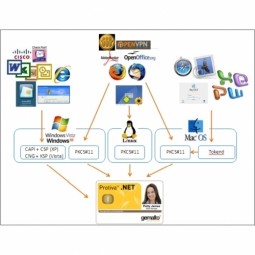
Case Study
Corporate Identity Solution Adds Convenience to Beckman Coulter
Beckman Coulter wanted to implement a single factor solution for physical and remote logical access to corporate network. Bechman Coulter's users were carrying smart card badges for doors, but also needed a one-time password token to access to our corporate network when they were not in the office. They wanted to simplify the process.
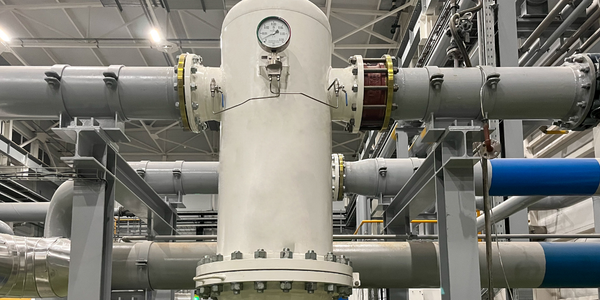
Case Study
Sparks Dynamics Assists Atlas Container Secure a $15,000 BGE Energy Rebate
The ReMASTER Compressed Air Monitoring system was installed in 2015. This system is capable of monitoring compressed air system parameters on a continuous basis and transferring that information to a cloud server which can be accessed by Atlas Container personnel, Industrial Diagnostics and Sparks Dynamics. This information was collected into a database which can be exported to an Excel spreadsheet or displayed graphically using Sparks Dynamics ViewMaster Software. The average annual compressed air electricity expense was estimated to be approximately $116,000. This is based on an incremental $/KWh electric rate of $.091 per KWh and an estimated compressed air energy consumption of 1,279,200 KWH. The implementation phase of Energy Conservation Measures (ECMs) for the Compressed Air System included: • Identification and repair of compressed air leaks • Understanding of compressed air usage per manufacturing machine and installation of shut off valves when the machines are no longer in production mode • Identification of misapplications of compressed air to include blow offs, venturis, and cooling scenarios • Understand system pressure requirements and potential installation of point of use pressure regulation.
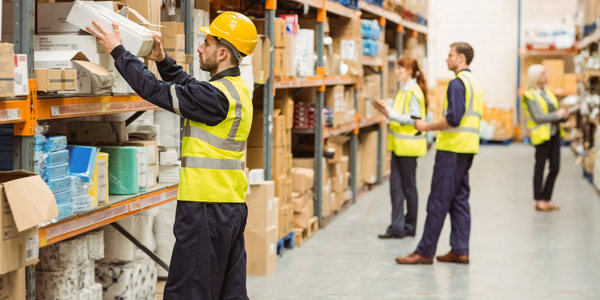
Case Study
Automated Pallet Labeling Solution for SPR Packaging
SPR Packaging, an American supplier of packaging solutions, was in search of an automated pallet labeling solution that could meet their immediate and future needs. They aimed to equip their lines with automatic printer applicators, but also required a solution that could interface with their accounting software. The challenge was to find a system that could read a 2D code on pallets at the stretch wrapper, track the pallet, and flag any pallets with unread barcodes for inspection. The pallets could be single or double stacked, and the system needed to be able to differentiate between the two. SPR Packaging sought a system integrator with extensive experience in advanced printing and tracking solutions to provide a complete traceability system.
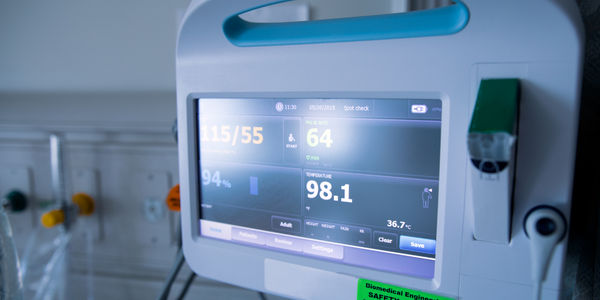
Case Study
Mondi Implements Statistics-Based Health Monitoring and Predictive Maintenance
The extrusion and other machines at Mondi’s plant are large and complex, measuring up to 50 meters long and 15 meters high. Each machine is controlled by up to five programmable logic controllers (PLCs), which log temperature, pressure, velocity, and other performance parameters from the machine’s sensors. Each machine records 300–400 parameter values every minute, generating 7 gigabytes of data daily.Mondi faced several challenges in using this data for predictive maintenance. First, the plant personnel had limited experience with statistical analysis and machine learning. They needed to evaluate a variety of machine learning approaches to identify which produced the most accurate results for their data. They also needed to develop an application that presented the results clearly and immediately to machine operators. Lastly, they needed to package this application for continuous use in a production environment.