下载PDF
Downtime of automated systems cut by 28% at Brillux paint plant

技术
- 自动化与控制 - 监督控制和数据采集 (SCADA)
适用行业
- 化学品
适用功能
- 流程制造
用例
- 机器状态监测
挑战
油漆和涂料专家 Brillux 是中欧的油漆产品制造商。该公司的仓库和配送业务包括由西门子 SIMATIC 自动化过程控制器控制的全自动输送系统和用于减少停机时间的传统 MLOG SCADA 系统。
客户
布里勒克斯
关于客户
Brillux 是一家提供全系列油漆和清漆的制造商和直接供应商。完整的范围包括 12,000 多篇文章。
解决方案
Brillux 与 SCHAD 合作实施 EXTEND7000 作为移动 SCADA 系统,为工程师提供“随时随地”警报。如果公司的主要配送中心出现问题,工程师可以收到系统性能问题的实时通知。此外,他们还能够使用标准的黑莓智能手机远程访问自动控制系统以调查系统性能问题。
运营影响
数量效益
相关案例.
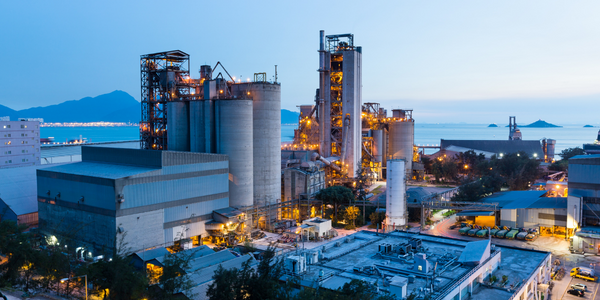
Case Study
Honeywell - Tata Chemicals Improves Data Accessibility with OneWireless
Tata was facing data accessibility challenges in the cement plant control room tapping signals from remote process control areas and other distant locations, including the gas scrubber. Tata needed a wireless solution to extend its control network securely to remote locations that would also provide seamless communication with existing control applications.
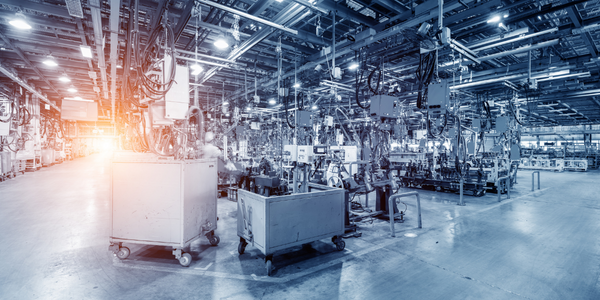
Case Study
Advanced Elastomer Systems Upgrades Production
In order to maintain its share of the international market for thermoplastic elastomers AES recently expanded its Florida plant by adding a new production line. While the existing lines were operating satisfactorily using a PROVOX distributed control system with traditional analog I/O, AES wanted advanced technology on the new line for greater economy, efficiency, and reliability. AES officials were anxious to get this line into production to meet incoming orders, but two hurricanes slowed construction.

Case Study
Wireless GPS Tracking & Security Monitoring
Enhancing the security of hazardous freight and ensuring compliance with Homeland Security’s Transportation Security Administration mandate that all trains carrying chemicals capable of creating a toxic inhalation condition are equipped with on-board safety monitoring systems.
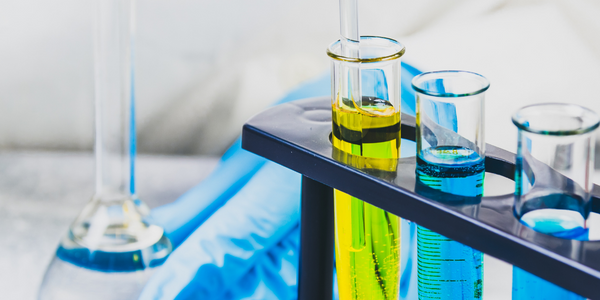
Case Study
Field Device Asset Management For Chemical Company in China
Chinese chemical subsidiary of multinational corporation serves customers throughout the world. Sales offices and research and technology centers are strategically located to provide rapid response to customer requests. Just two workers were assigned to maintain thousands of intelligent instruments in three production units, so they could do little more than react to device issues as they appeared. This costly maintenance method inevitably led to unexpected downtime when a critical instrument failed. Plant management recognized the need to change from reactive to predictive maintenance for all assets, including instruments and control valves, but help was needed in implementing such a technology-based initiative.
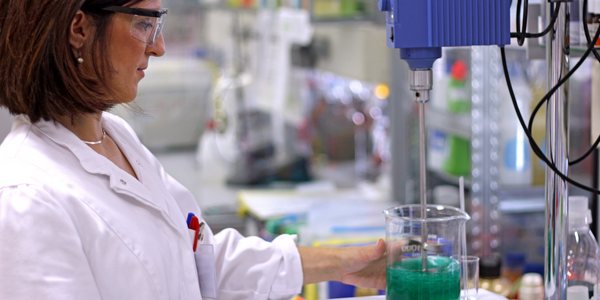
Case Study
Industrial Workforce Mobility for Improved Safety & Operations
Huntsman Corporation, a global manufacturer and marketer of differentiated chemicals, undertook an aggressive program to eliminate injuries, product defects, and environmental releases at their Port Neches facility. Termed “Project Zero”, this program required a completely mobile solution to empower operations and maintenance personnel to capture defects, track work progress and make process and safety related decisions in real-time.