下载PDF
DS PLM SUCCESS STORY - Panasonic Home Appliances
技术
- 功能应用 - 产品生命周期管理系统 (PLM)
- 功能应用 - 产品数据管理系统
适用行业
- 电子产品
- 消费品
适用功能
- 产品研发
- 离散制造
用例
- 自动化制造系统
服务
- 软件设计与工程服务
- 系统集成
挑战
Panasonic Home Appliances, a specialist in household appliances, faced a challenge of reducing product development lead time dramatically. The company needed to transition from 2D drawings to 3D design to meet the increasing demand for induction heated (IH) ranges and other IH-at-able cooking appliances. The spike in demand for IH ranges beginning around 2000 and new competitors quickly hitting the market, Panasonic knew it needed to adopt Product Lifecycle Management (PLM) technology quickly. With its customers demanding greater product variation, Panasonic understood that to remain competitive it must demonstrate consistent improvement in the functionality and quality of its products. Panasonic also knew that it must reduce costs and shorten development lead-time.
关于客户
Panasonic Home Appliances is a business unit of Panasonic that specializes in household appliances, including refrigerators, washing machines, and rice cookers. The Kitchen Appliance Business Unit (BU) manufactures and sells induction heated (IH) ranges and other IH-at-able cooking appliances. IH electrically-powered ranges have increased in popularity due to their clean and eco-friendly nature. With a spike in demand for IH ranges beginning around 2000 and new competitors quickly hitting the market, Panasonic knew it needed to adopt Product Lifecycle Management (PLM) technology quickly. With its customers demanding greater product variation, Panasonic understood that to remain competitive it must demonstrate consistent improvement in the functionality and quality of its products.
解决方案
Panasonic chose CATIA from Dassault Systèmes to create a collaborative environment among its design, manufacturing, and partner companies to promote concurrent engineering. The design team adopted 3D tools in 2000 to increase design quality and to reduce lead times through more effective collaboration on design data among internal departments, such as design, mechanical design, circuit design, and prototyping. By exchanging CATIA data between Panasonic’s design and mechanical design departments, time loss on data conversion was eliminated, hands-off effort was greatly reduced, and the reliability of the design data was increased. Concurrent design approaches are improving design quality and reducing reworks. 3D design data generated with CATIA also is being transmitted to Panasonic’s molding machines to which manufacture prototypes. This has enabled Panasonic to halve manufacturing lead time when compared to conventional NC tool machining, to eliminate manual re-works, and to improve prototype accuracy and reliability.
运营影响
数量效益
相关案例.
.png)
Case Study
Improving Vending Machine Profitability with the Internet of Things (IoT)
The vending industry is undergoing a sea change, taking advantage of new technologies to go beyond just delivering snacks to creating a new retail location. Intelligent vending machines can be found in many public locations as well as company facilities, selling different types of goods and services, including even computer accessories, gold bars, tickets, and office supplies. With increasing sophistication, they may also provide time- and location-based data pertaining to sales, inventory, and customer preferences. But at the end of the day, vending machine operators know greater profitability is driven by higher sales and lower operating costs.
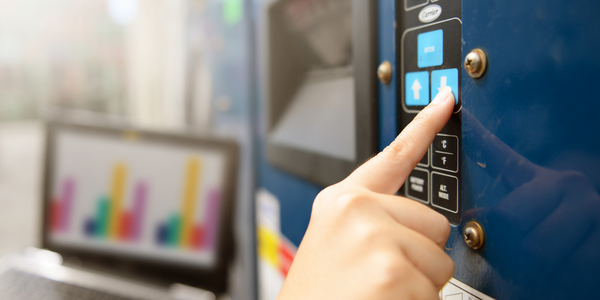
Case Study
Remote Temperature Monitoring of Perishable Goods Saves Money
RMONI was facing temperature monitoring challenges in a cold chain business. A cold chain must be established and maintained to ensure goods have been properly refrigerated during every step of the process, making temperature monitoring a critical business function. Manual registration practice can be very costly, labor intensive and prone to mistakes.
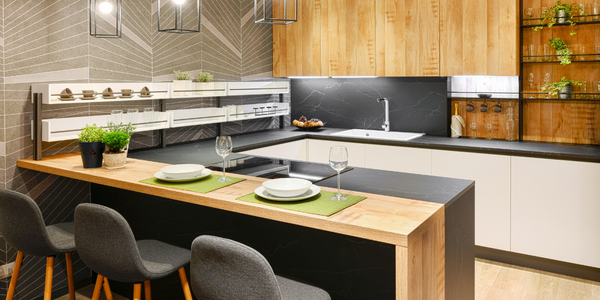
Case Study
Series Production with Lot-size-1 Flexibility
Nobilia manufactures customized fitted kitchens with a lot size of 1. They require maximum transparency of tracking design data and individual processing steps so that they can locate a particular piece of kitchen furniture in the sequence of processes.