下载PDF
Ds Plm Success Story - Zvezda
技术
- 功能应用 - 产品数据管理系统
适用行业
- 消费品
适用功能
- 产品研发
用例
- 快速原型制作
- 虚拟原型与产品测试
服务
- 软件设计与工程服务
挑战
Zvezda, a leading Russian toymaker, faced challenges in maintaining its lead in the domestic market and securing its entry into the international market. The company needed to reduce product development time and modernize its operations with state-of-the-art technology used in modern toy manufacturing. The company's traditional methods based on outdated drawing technology were insufficient for creating exact replicas of modern aircraft, which have exceptionally sophisticated interior layouts. Increased competition in domestic and international toy markets forced Zvezda to adopt a new strategy that ensures technological support of its production process. The company's main business goals, such as constantly replenishing its stock, improving product quality, and focusing on innovation, necessitated the implementation of a more powerful system for automated design.
关于客户
Zvezda Open Joint-Stock Company (Zvezda) is one of the largest producers of prefabricated models of civilian and military equipment, historical miniatures, table games, and toys in Russia. Located near Moscow, it is one of the most popular toy brands in the country. The company's strategic goals include the production of prefabricated models, particularly replicas of modern aircraft from aerospace manufacturers including Kamov, Sukhoy, MiG, and Tupolev. Zvezda's main business goals include constantly replenishing its stock, improving product quality, and focusing on innovation. The company produces over 50 new models annually in its core field of prefabricated models, military and historical miniatures, and successfully sells its products worldwide.
解决方案
Zvezda chose CATIA, a 3D modeling software, to speed up the design of exact replica models. The software was chosen because it is used by leading Russian design departments that work closely with the company to ensure technical precision of prefabricated aircraft models. After its designers completed training and began working with CATIA, the company noticed significant benefits in terms of time saved on designing and launching a new product coupled with overall product quality. CATIA is capable of solving design challenges such as making complicated break lines, designing tools, and creating sophisticated packaging. The software's powerful parameterization capabilities allow Zvezda to immediately change the dimensions of a form and to adjust it to a certain type of equipment.
运营影响
数量效益
相关案例.
.png)
Case Study
Improving Vending Machine Profitability with the Internet of Things (IoT)
The vending industry is undergoing a sea change, taking advantage of new technologies to go beyond just delivering snacks to creating a new retail location. Intelligent vending machines can be found in many public locations as well as company facilities, selling different types of goods and services, including even computer accessories, gold bars, tickets, and office supplies. With increasing sophistication, they may also provide time- and location-based data pertaining to sales, inventory, and customer preferences. But at the end of the day, vending machine operators know greater profitability is driven by higher sales and lower operating costs.
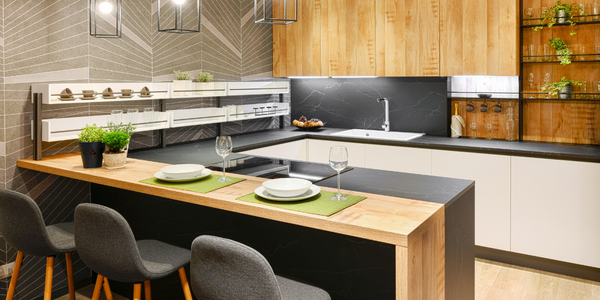
Case Study
Series Production with Lot-size-1 Flexibility
Nobilia manufactures customized fitted kitchens with a lot size of 1. They require maximum transparency of tracking design data and individual processing steps so that they can locate a particular piece of kitchen furniture in the sequence of processes.
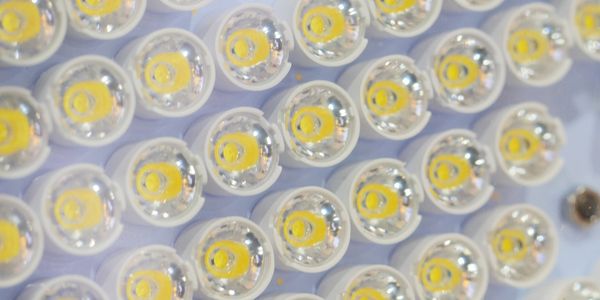
Case Study
American Eagle Achieves LEED with GE LED Lighting Fixtures
American Eagle Outfitters (AEO) was in the process of building a new distribution center. The AEO facility management team decided to look at alternate options for lighting layout that could provide energy and maintenance savings. AEO would need a full-time maintenance employee just to replace burned-out fluorescent tubes.
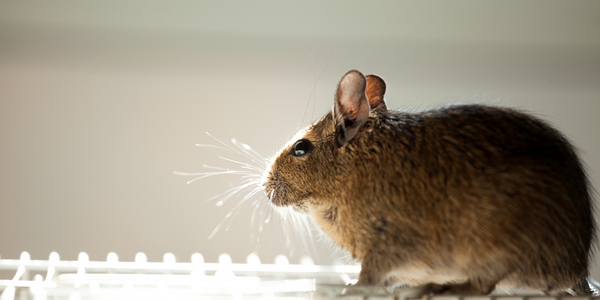
Case Study
Revolutionizing Rodent Control
From pet- and child-safe traps, to touch-free and live-catch rodent control solutions, Victor continues to stay committed to producing superior products that meet the varying needs of today’s pest control professionals. And, with a long standing history supporting customers in the food processing, service, and retail settings, Victor knew that strict regulations were costing organizations thousands of dollars in excess overhead trying to manage their rodent-control solutions. Trap inspections in these environments are often difficult and time consuming, requiring personnel to manually check a trap’s status multiple times per day, amounting to over six hours of manual labor. Victor is looking for an innovative way to increase operational efficiencies with the use of technology.