下载PDF
Gist delivers premium supply chain services with outstanding reliability
技术
- 应用基础设施与中间件 - 数据交换与集成
- 应用基础设施与中间件 - 中间件、SDK 和库
适用功能
- 物流运输
用例
- 过程控制与优化
- 供应链可见性(SCV)
服务
- 软件设计与工程服务
- 系统集成
挑战
Gist Limited, a leading U.K. supply chain solutions provider, needed to improve the speed, efficiency, and traceability of its enterprise interfaces. The company's success depends on its ability to consistently deliver superior service 24/7 despite challenging targets. Gist's IT systems had to be as reliable as the rest of its business, otherwise, it would escalate very quickly. If there was an unplanned middleware outage, file or data issue lasting longer than 20 minutes, the business would already be saying, 'Now it's too late. We're going to have to go manual and pick to an estimate.' This increases costs, incurs customer fines, and affects the company's reputation. Gist's supply chain is incredibly fast: A sandwich produced by a supplier in Scotland is available for sale by a store in the south of England, more than 500 miles away, a mere 24 hours after manufacture.
关于客户
Gist Limited is a leading U.K. supply chain solutions provider and division of The Linde Group. The company specializes in time- and temperature-controlled logistics. Gist’s personal approach and tailored, flexible solutions deliver not just supply chain reliability and end-to-end visibility but also greater competitive advantage for the company’s 3,000+ global customers. Operating from more than 40 locations in the U.K., Europe and worldwide, Gist’s 5,000 employees generate an annual turnover of €600 million. A leader in the perishable and chilled sector, Gist’s vision is to be the customer’s ongoing partner of choice for logistics innovation and delivery excellence. Suppliers, manufacturers and retailers of all sizes rely on Gist’s expertise and efficiencies in supply chain operations.
解决方案
Gist decided to move from its existing middleware platform to the webMethods Integration Platform. The company chose to implement by interface groups, essentially by large customers and customer groups, to optimize risk and minimize service disruption during the migration. After the middleware migration was complete, Gist’s second challenge to manage was a major change to its B2B service. To better support the business, Gist opted to bring its B2B service in-house using webMethods Trading Networks, complementary software to the webMethods ESB. The B2B project was high-priority—120 trading partners had to be moved to the new technology within four months. The project was staffed with the most senior people and meticulously planned at a detailed level.
运营影响
数量效益
相关案例.
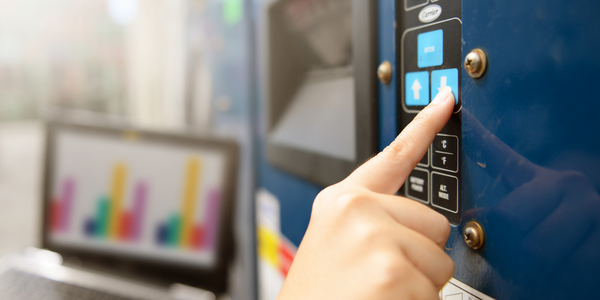
Case Study
Remote Temperature Monitoring of Perishable Goods Saves Money
RMONI was facing temperature monitoring challenges in a cold chain business. A cold chain must be established and maintained to ensure goods have been properly refrigerated during every step of the process, making temperature monitoring a critical business function. Manual registration practice can be very costly, labor intensive and prone to mistakes.
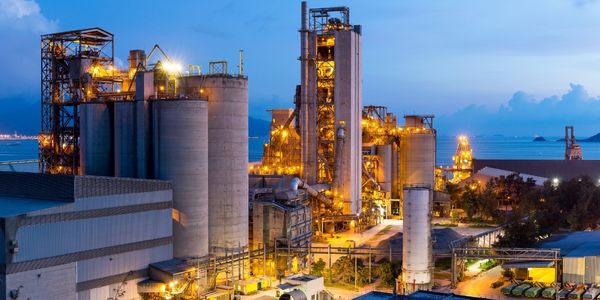
Case Study
System 800xA at Indian Cement Plants
Chettinad Cement recognized that further efficiencies could be achieved in its cement manufacturing process. It looked to investing in comprehensive operational and control technologies to manage and derive productivity and energy efficiency gains from the assets on Line 2, their second plant in India.
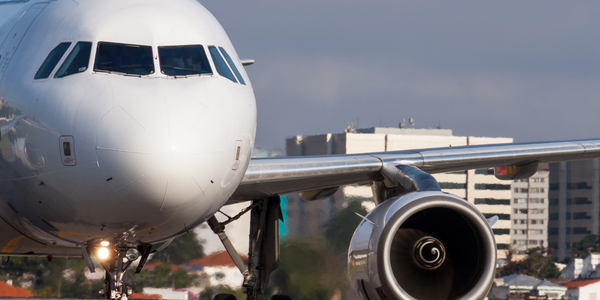
Case Study
Airbus Soars with Wearable Technology
Building an Airbus aircraft involves complex manufacturing processes consisting of thousands of moving parts. Speed and accuracy are critical to business and competitive advantage. Improvements in both would have high impact on Airbus’ bottom line. Airbus wanted to help operators reduce the complexity of assembling cabin seats and decrease the time required to complete this task.
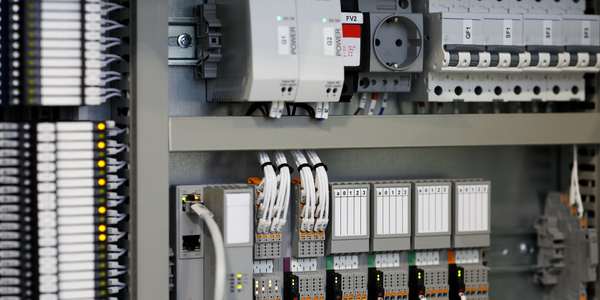
Case Study
Improving Production Line Efficiency with Ethernet Micro RTU Controller
Moxa was asked to provide a connectivity solution for one of the world's leading cosmetics companies. This multinational corporation, with retail presence in 130 countries, 23 global braches, and over 66,000 employees, sought to improve the efficiency of their production process by migrating from manual monitoring to an automatic productivity monitoring system. The production line was being monitored by ABB Real-TPI, a factory information system that offers data collection and analysis to improve plant efficiency. Due to software limitations, the customer needed an OPC server and a corresponding I/O solution to collect data from additional sensor devices for the Real-TPI system. The goal is to enable the factory information system to more thoroughly collect data from every corner of the production line. This will improve its ability to measure Overall Equipment Effectiveness (OEE) and translate into increased production efficiencies. System Requirements • Instant status updates while still consuming minimal bandwidth to relieve strain on limited factory networks • Interoperable with ABB Real-TPI • Small form factor appropriate for deployment where space is scarce • Remote software management and configuration to simplify operations