下载PDF
Hella brings transparency to business data with QlikView
技术
- 分析与建模 - 实时分析
适用行业
- 汽车
- 零售
适用功能
- 销售与市场营销
用例
- 供应链可见性(SCV)
- 库存管理
服务
- 数据科学服务
挑战
Hella Handel Austria, a leading worldwide partner of the automotive industry, was facing challenges with its data management. The company generates vast quantities of new data every day, with 45,000 active items, 900 active customers, and approximately 20,000 orders per month. To evaluate this data, the company needed a powerful analysis tool that would allow ad-hoc analyses of its extensive data inventory while conserving employee resources. Previously, only a few specially-trained Hella experts had suitable programming skills to evaluate the business data stored in the DB2 and Oracle databases. Several employees were busy almost full-time programming queries and manually processing the results in Excel or Access. The multitude of different tools and the high percentage of manual work meant that errors were inevitable.
关于客户
Hella Handel Austria GmbH is a subsidiary of the internationally renowned automotive industry supplier. The company is a leading worldwide partner of the automotive industry, ensuring the supply of parts and accessories to repair shops and garages, particularly in the areas of lighting, electrical systems, electronics, and air conditioning. With 45,000 active items, 900 active customers, and approximately 20,000 orders per month, the company generates vast quantities of new data every day. The company operates in the retail and wholesale distribution industry and is based in Austria.
解决方案
Hella Handel Austria deployed QlikView to 30 users across a number of functional areas and at all levels of the organization within just 1 week. With QlikView, Hella Handel now analyzes key metrics across sales orders, pricing management, margin control, merchandising, category management, inventory stock, and finance. With QlikView Connector, Hella Handel is able to free the invaluable data locked in its SAP ERP system and Lawson (M3). Through QlikView Server and Publisher, Hella Handel easily manages the performance and visibility across the large data volume. QlikView was implemented quickly and without complications within a 1-week period. The centralized solution was installed and all of the future user groups were ‘trained’. Today, Hella Handel Austria is using QlikView in a wide range of departments and across all management levels – from administration and office functions to the logistics manager, controller, product manager, marketing manager, and sales office and field services.
运营影响
数量效益
相关案例.
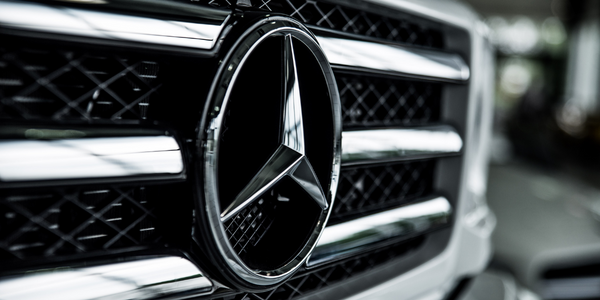
Case Study
Integral Plant Maintenance
Mercedes-Benz and his partner GAZ chose Siemens to be its maintenance partner at a new engine plant in Yaroslavl, Russia. The new plant offers a capacity to manufacture diesel engines for the Russian market, for locally produced Sprinter Classic. In addition to engines for the local market, the Yaroslavl plant will also produce spare parts. Mercedes-Benz Russia and his partner needed a service partner in order to ensure the operation of these lines in a maintenance partnership arrangement. The challenges included coordinating the entire maintenance management operation, in particular inspections, corrective and predictive maintenance activities, and the optimizing spare parts management. Siemens developed a customized maintenance solution that includes all electronic and mechanical maintenance activities (Integral Plant Maintenance).
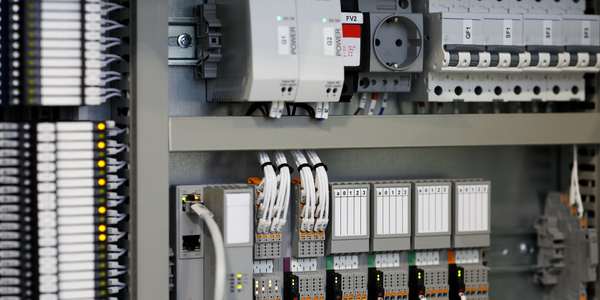
Case Study
Improving Production Line Efficiency with Ethernet Micro RTU Controller
Moxa was asked to provide a connectivity solution for one of the world's leading cosmetics companies. This multinational corporation, with retail presence in 130 countries, 23 global braches, and over 66,000 employees, sought to improve the efficiency of their production process by migrating from manual monitoring to an automatic productivity monitoring system. The production line was being monitored by ABB Real-TPI, a factory information system that offers data collection and analysis to improve plant efficiency. Due to software limitations, the customer needed an OPC server and a corresponding I/O solution to collect data from additional sensor devices for the Real-TPI system. The goal is to enable the factory information system to more thoroughly collect data from every corner of the production line. This will improve its ability to measure Overall Equipment Effectiveness (OEE) and translate into increased production efficiencies. System Requirements • Instant status updates while still consuming minimal bandwidth to relieve strain on limited factory networks • Interoperable with ABB Real-TPI • Small form factor appropriate for deployment where space is scarce • Remote software management and configuration to simplify operations