下载PDF
How FourKites Helped Unilever South Africa Overcome Border Delays in a Pandemic
技术
- 功能应用 - 车队管理系统 (FMS)
- 分析与建模 - 预测分析
- 网络与连接 - 蜂窝
适用行业
- 消费品
适用功能
- 物流运输
- 仓库和库存管理
用例
- 车队管理
- 预测性维护
- 供应链可见性(SCV)
- 实时定位系统 (RTLS)
服务
- 系统集成
- 培训
- 软件设计与工程服务
挑战
One of Unilever’s biggest challenges during the early days of the COVID-19 pandemic was establishing end-to-end visibility on carriers hauling cross-border shipments. Border crossings are traditionally a difficult challenge for supply chain and logistics professionals, and this was no exception for Unilever’s South Africa team. South Africa shares a border with six other sovereign nations, two of which are located entirely within South Africa itself. To make matters worse, the country was hit particularly hard by COVID, with a unique strain of the virus arising relatively early on. All of these obstacles escalated an already-difficult situation into a crippling challenge. In normal times, the average wait time at South Africa’s borders is between 4 to 6 hours. With the onset of COVID-19, these wait times skyrocketed to more than 10 hours a day due to congestion and new checks at the border. With delays at the borders increasing and demand for consumer packaged goods on the rise throughout the greater Sub-Saharan region, the Unilever team needed a solution, and they needed it fast.
关于客户
Unilever is a multinational consumer goods company that began its search for real-time transportation visibility in 2018. The company aimed to empower its employees to plan proactively, optimize internal processes, and collaborate more closely with customers. Unilever's objectives included receiving predictive visibility into real-time location and estimated time of arrival (ETA) for shipments, providing proactive communication to key stakeholders about delays in critical monitored shipments, reducing manual workload, improving carrier performance, and reducing wait times at customer facilities. Unilever South Africa, a regional branch of the global giant, faced significant challenges during the COVID-19 pandemic, particularly with cross-border shipments due to increased wait times and new checks at the borders.
解决方案
Unilever leveraged FourKites’ Custom Geofence capability to bolster its limited resources with proactive, predictive data. Using this solution, Unilever created custom zones around border crossings and ports of entry, configuring FourKites to automatically issue alerts to team members whenever a shipment entered, exited, or had been delayed at a border for longer than a specified time. This allowed Unilever’s team to make targeted decisions and limit their attention to shipments that were in danger of being delayed or that were experiencing major delays at border crossings around the country. These alerts helped the Unilever team to identify the cause for the delay (if any) and reschedule the appointment time with the customers based on any known delays. Using FourKites’ custom zones helped Unilever overcome a difficult situation by providing border visibility when a truck arrives, waits, and departs from the border. Additionally, Unilever configured FourKites’ Notifications & Alerts to automatically alert employees when a truck’s wait time at a facility exceeded 4 hours, enabling them to take appropriate action based on the notifications and reduce driver wait time at the facility. By recording not only planned entry and exit times but actual timestamps for updating Completion of Delivery (CoD) events, FourKites made it possible for Unilever to eliminate the highly manual task of gathering entry and exit information from employees’ workloads, and instead let employees focus on more value-add tasks.
运营影响
数量效益
相关案例.
.png)
Case Study
Improving Vending Machine Profitability with the Internet of Things (IoT)
The vending industry is undergoing a sea change, taking advantage of new technologies to go beyond just delivering snacks to creating a new retail location. Intelligent vending machines can be found in many public locations as well as company facilities, selling different types of goods and services, including even computer accessories, gold bars, tickets, and office supplies. With increasing sophistication, they may also provide time- and location-based data pertaining to sales, inventory, and customer preferences. But at the end of the day, vending machine operators know greater profitability is driven by higher sales and lower operating costs.
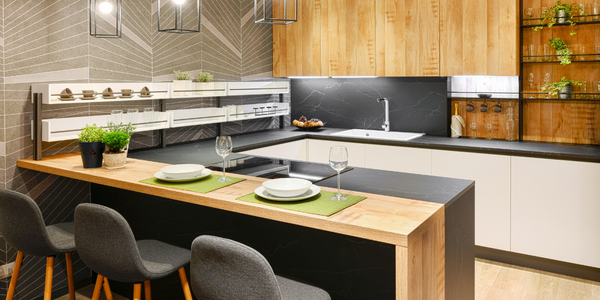
Case Study
Series Production with Lot-size-1 Flexibility
Nobilia manufactures customized fitted kitchens with a lot size of 1. They require maximum transparency of tracking design data and individual processing steps so that they can locate a particular piece of kitchen furniture in the sequence of processes.
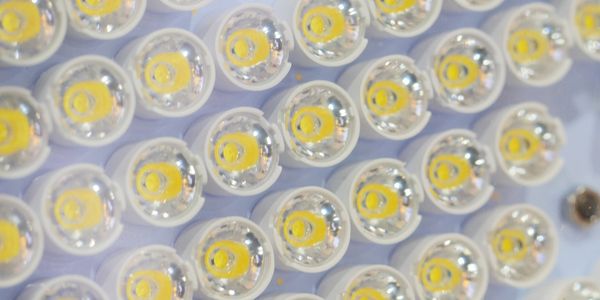
Case Study
American Eagle Achieves LEED with GE LED Lighting Fixtures
American Eagle Outfitters (AEO) was in the process of building a new distribution center. The AEO facility management team decided to look at alternate options for lighting layout that could provide energy and maintenance savings. AEO would need a full-time maintenance employee just to replace burned-out fluorescent tubes.
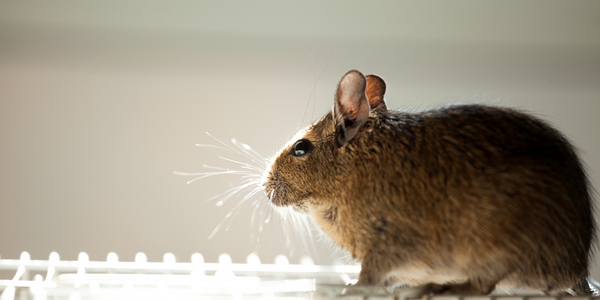
Case Study
Revolutionizing Rodent Control
From pet- and child-safe traps, to touch-free and live-catch rodent control solutions, Victor continues to stay committed to producing superior products that meet the varying needs of today’s pest control professionals. And, with a long standing history supporting customers in the food processing, service, and retail settings, Victor knew that strict regulations were costing organizations thousands of dollars in excess overhead trying to manage their rodent-control solutions. Trap inspections in these environments are often difficult and time consuming, requiring personnel to manually check a trap’s status multiple times per day, amounting to over six hours of manual labor. Victor is looking for an innovative way to increase operational efficiencies with the use of technology.