下载PDF
iCracked Enhances On-Demand iOS Device Repairs with Twilio
技术
- 分析与建模 - 实时分析
- 平台即服务 (PaaS) - 设备管理平台
适用行业
- 电子产品
- 电信
适用功能
- 维护
- 销售与市场营销
用例
- 实时定位系统 (RTLS)
- 语音识别
服务
- 系统集成
- 测试与认证
挑战
iCracked 是一家智能设备维修和转售网络,在为其用户提供高质量且响应迅速的客户服务体验方面面临着重大挑战。该公司最初在其网站上列出了数百个技术人员的个人电话号码,事实证明,这效率极低,而且令客户感到沮丧,因为他们必须通过电话号码冷酷地拨打列表才能找到可用的技术人员。 iCracked 随后转向虚拟电话系统产品,该系统缺乏用于构建高级自动化功能的 API。如果没有通话跟踪和录音,就很难监控客户互动,而且几乎不可能保证服务。现有的通信平台也无法与 iCracked 一起扩展,导致通话质量差和掉线。 iCracked 需要一个强大而灵活的通信平台,使公司能够轻松地将先进的通信功能集成到其业务流程中。
关于客户
iCracked 是全球最大、最高效的 Apple iPhone、iPad 和 iPod 按需维修和回购服务。 iCracked 在 11 个国家/地区拥有 500 多名当地技术人员,以快速、专业的服务为基础,通过将经过认证的“iTech”实时派遣到客户选择的便利地点,使客户可以轻松维修或销售其 iOS 设备。该公司的成立宗旨是让 iOS 设备维修变得快速、方便且可靠,确保消费者在 iPhone、iPad 或 iPod 出现故障时不会陷入困境。
解决方案
iCracked 采用 Twilio SMS 和 Twilio Voice 来自动安排工作、衡量技术人员的工作效率、支持实时客户沟通并提供卓越的客户服务。 iCracked 使用 Twilio SMS 发送状态更新并启用工作安排,以实现双向警报和通知。一旦客户将其信息(包括设备类型、维修问题和位置)输入 iCracked 的移动应用程序或网站,客户就会通过短信得知订单请求已收到,iTech 将很快与他们联系。在后端,iCracked 会向距离客户最近的 iTech 池发送一条短信。然后,iTechs 可以回复该文本以接受该工作。 Twilio 还支持对每个服务请求进行呼叫跟踪和录音,这是 iCracked 的关键质量控制功能,可衡量技术人员的工作效率、确保业务不会在系统之外进行,并从各种场景中学习以不断改进服务。
运营影响
数量效益
相关案例.
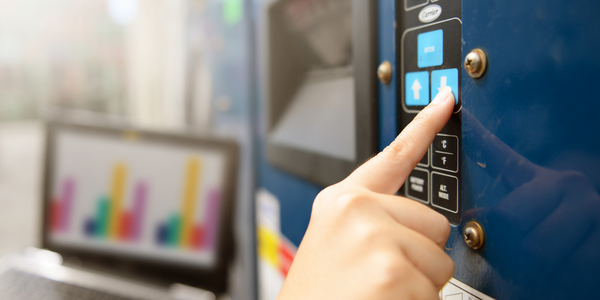
Case Study
Remote Temperature Monitoring of Perishable Goods Saves Money
RMONI was facing temperature monitoring challenges in a cold chain business. A cold chain must be established and maintained to ensure goods have been properly refrigerated during every step of the process, making temperature monitoring a critical business function. Manual registration practice can be very costly, labor intensive and prone to mistakes.
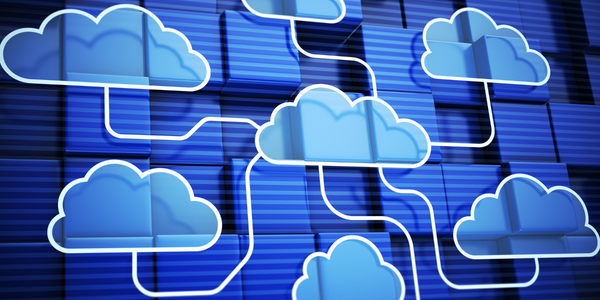
Case Study
Cloud Solution for Energy Management Platform-Schneider Electric
Schneider Electric required a cloud solution for its energy management platform to manage high computational operations, which were essential for catering to client requirements. As the business involves storage and analysis of huge amounts of data, the company also needed a convenient and scalable storage solution to facilitate operations efficiently.
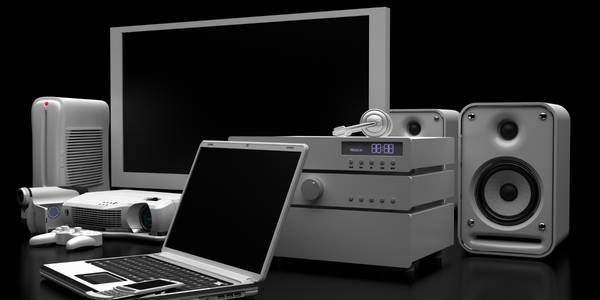
Case Study
Leveraging the IoT to Gain a Competitive Edge in International Competition
Many large manufacturers in and outside Japan are competing for larger market share in the same space, expecting a growing demand for projectors in the areas of entertainment, which requires glamor and strong visual performance as well as digital signage that can attract people’s attention. “It is becoming more and more difficult to differentiate ourselves with stand-alone hardware products,” says Kazuyuki Kitagawa, Director of Service & Support at Panasonic AVC Networks. “In order for Panasonic to grow market share and overall business, it is essential for us to develop solutions that deliver significant added value.” Panasonic believes projection failure and quality deterioration should never happen. This is what and has driven them to make their projectors IoT-enabled. More specifically, Panasonic has developed a system that collects data from projectors, visualizes detailed operational statuses, and predicts issues and address them before failure occurs. Their projectors are embedded with a variety of sensors that measure power supply, voltage, video input/ output signals, intake/exhaust air temperatures, cooling fan operations, and light bulb operating time. These sensors have been used to make the projector more intelligent, automatically suspending operation when the temperature rises excessively, and automatically switching light bulbs. Although this was a great first step, Panasonic projectors were still not equipped with any capability to send the data over a network.