下载PDF
Improving Overall A/R Efficiency with Digital Transformation of Credit, Collections, and Cash Posting
技术
- 分析与建模 - 预测分析
- 应用基础设施与中间件 - 数据交换与集成
- 功能应用 - 企业资源规划系统 (ERP)
适用功能
- 商业运营
- 质量保证
用例
- 过程控制与优化
服务
- 软件设计与工程服务
- 系统集成
挑战
Summit Electric faced several challenges in their Accounts Receivable (A/R) processes. The credit team struggled with manual and inconsistent data gathering, incomplete data, lack of real-time risk alerts, and longer turnaround times due to the absence of a workflow. The collections team had no customer prioritization strategy and faced issues with process standardization, leading to inconsistencies and inefficiencies. The cash application process was entirely manual, with poor lockbox services and manual deduction coding, resulting in slow processing and delays.
关于客户
Summit Electric Supply Co. Inc. is a privately held, independent wholesale distributor of industrial electrical equipment and supplies, founded in 1977. Headquartered in Albuquerque, New Mexico, the company has over 550 employees and ranks #17 among electrical distributors in the United States. Summit Electric is known for its forward-thinking approach towards technology and its commitment to serving customers by adding superior value through industry expertise and innovative systems. With a revenue of $505 million, the company has a significant presence in the wholesale distribution industry.
解决方案
HighRadius provided Summit Electric with a comprehensive solution to address their A/R challenges. The Credit Cloud automated the approval workflow for low-risk customers, aggregated credit data from multiple agencies, and offered an online credit application for ease of use. The Collections Cloud prioritized worklists for maximum collector effectiveness and automated correspondence for low-risk customers. The Cash Application Cloud eliminated lockbox fees, automated transactional tasks, and enabled auto-identification and submission of remittance in no remittance scenarios. Additionally, it provided automatic conversion of customer reason-codes to internal codes and auto-invoice matching, significantly improving efficiency and reducing manual effort.
运营影响
数量效益
相关案例.
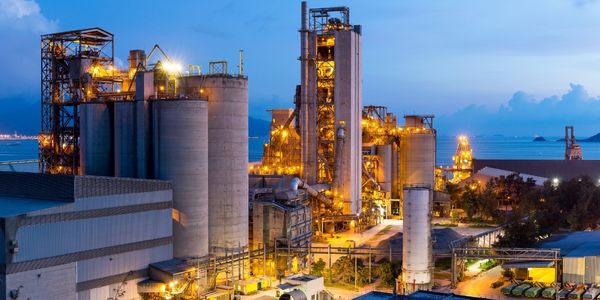
Case Study
System 800xA at Indian Cement Plants
Chettinad Cement recognized that further efficiencies could be achieved in its cement manufacturing process. It looked to investing in comprehensive operational and control technologies to manage and derive productivity and energy efficiency gains from the assets on Line 2, their second plant in India.
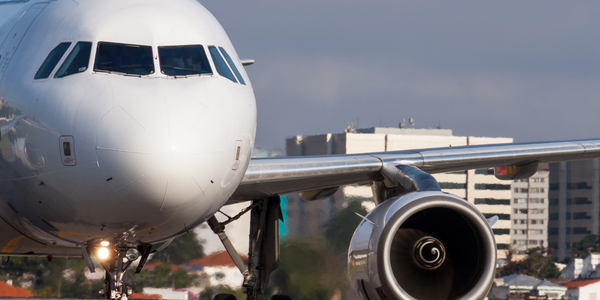
Case Study
Airbus Soars with Wearable Technology
Building an Airbus aircraft involves complex manufacturing processes consisting of thousands of moving parts. Speed and accuracy are critical to business and competitive advantage. Improvements in both would have high impact on Airbus’ bottom line. Airbus wanted to help operators reduce the complexity of assembling cabin seats and decrease the time required to complete this task.
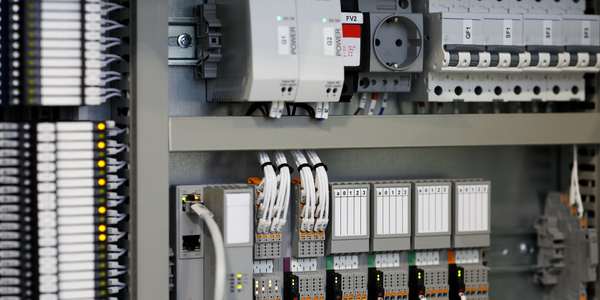
Case Study
Improving Production Line Efficiency with Ethernet Micro RTU Controller
Moxa was asked to provide a connectivity solution for one of the world's leading cosmetics companies. This multinational corporation, with retail presence in 130 countries, 23 global braches, and over 66,000 employees, sought to improve the efficiency of their production process by migrating from manual monitoring to an automatic productivity monitoring system. The production line was being monitored by ABB Real-TPI, a factory information system that offers data collection and analysis to improve plant efficiency. Due to software limitations, the customer needed an OPC server and a corresponding I/O solution to collect data from additional sensor devices for the Real-TPI system. The goal is to enable the factory information system to more thoroughly collect data from every corner of the production line. This will improve its ability to measure Overall Equipment Effectiveness (OEE) and translate into increased production efficiencies. System Requirements • Instant status updates while still consuming minimal bandwidth to relieve strain on limited factory networks • Interoperable with ABB Real-TPI • Small form factor appropriate for deployment where space is scarce • Remote software management and configuration to simplify operations
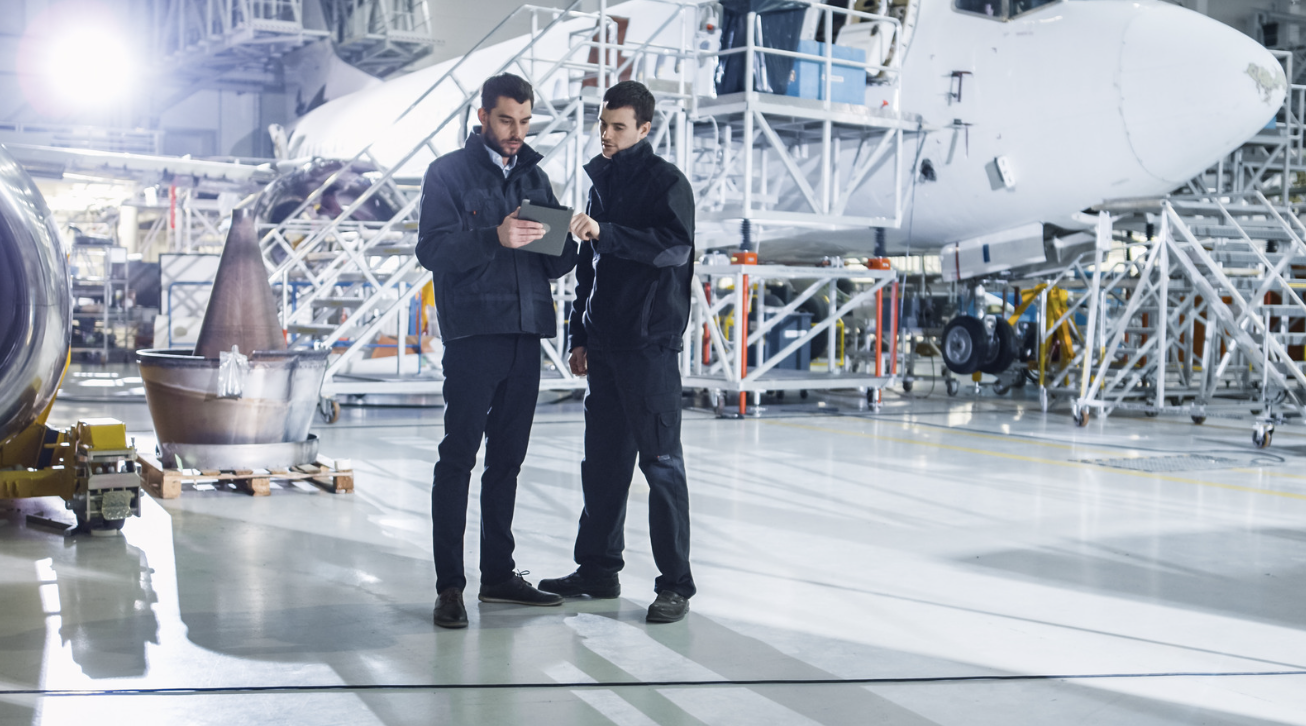
Case Study
Developing Smart Tools for the Airbus Factory
Manufacturing and assembly of aircraft, which involves tens of thousands of steps that must be followed by the operators, and a single mistake in the process could cost hundreds of thousands of dollars to fix, makes the room for error very small.