下载PDF
In the fast lane for business transformation – with webMethods
技术
- 应用基础设施与中间件 - API 集成与管理
适用行业
- 包装
- 造纸
- 回收与废物管理
适用功能
- 离散制造
- 采购
用例
- 过程控制与优化
- 质量预测分析
- 供应链可见性(SCV)
服务
- 系统集成
- 软件设计与工程服务
挑战
Prinzhorn Group, a European market leader in the packaging, paper and recycling industry, faced several challenges as it pursued its Grow2030 vision to double in size. The rapid growth strategy brought together many different systems that needed to be integrated, posing a major challenge for the company’s IT. The company needed a suitable and flexible IT platform to integrate new facilities and systems quickly. To boost the transforming company’s operational performance, all the apps, devices and systems needed to be linked to create a common data pool for the entire group—a central point of dataflow. Furthermore, this data pool had to allow fast adaptation at any time because new systems were being added regularly, up to ten a year.
关于客户
The Prinzhorn Group is a European market leader in the packaging, paper and recycling industry. With 7,000 employees in 15 countries, the company was founded in 1853 and posts an annual turnover of 1.60 billion euros. The family-owned and managed company has its headquarters in Vienna, Austria and is structured in three divisions: Dunapack Packaging (corrugated packaging solutions), Hamburger Containerboard (production of containerboard) and Hamburger Recycling Group (collection and trading of secondary raw materials). In 2015, the company adopted the Grow2030 vision along with the goal of doubling in size, and has actively pursued this objective ever since. Today Prinzhorn is Europe’s third-largest company in the packaging, paper and recycling industry and is maintaining its course toward business transformation.
解决方案
Software AG’s B2B integration platform, webMethods, was chosen by Prinzhorn Group to integrate the different systems from Prinzhorn’s three divisions, some of which are difficult to integrate. Specifically, it was about the IT connection to operational processes as well as the SAP® finance system. The first integration was done in 2014, and many more have followed since then. The success of the integration projects rests on webMethods’ capabilities, but also flourishes because of the collaboration between Prinzhorn’s teams and Software AG’s Professional Services consultants. Software AG Austria’s experts deliver onsite support for Prinzhorn’s employees in Austria with the help of their consultant colleagues from Germany and Bulgaria. With the open and independent webMethods integration platform, Prinzhorn Holding feels “ready for the future.” webMethods enables the company to integrate existing systems into a rapidly changing IT landscape, while also connecting additional external systems.
运营影响
数量效益
相关案例.
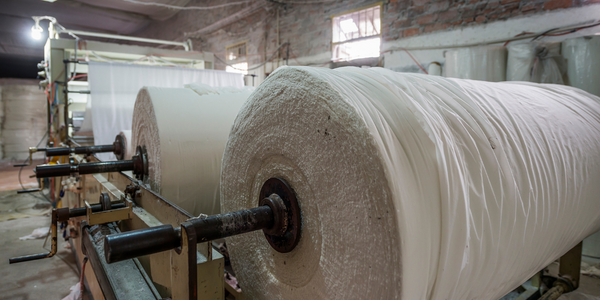
Case Study
Wireless Improves Efficiency in Compressed Air Systems
Hollingsworth and Vose wanted to improve the efficiency of their compressed air system, lower the electricity expense component of manufacturing cost in their commodity industry, and conserve energy leading to lowered greenhouse gas emissions. Compressed air systems degrade over time and become leaky and inefficient. Hollingsworth and Vose wanted to increase the frequency of system inspections without paying the high cost of manual labor.
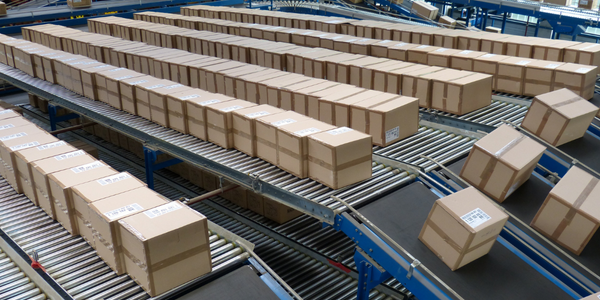
Case Study
IoT Data Analytics Case Study - Packaging Films Manufacturer
The company manufactures packaging films on made to order or configure to order basis. Every order has a different set of requirements from the product characteristics perspective and hence requires machine’s settings to be adjusted accordingly. If the film quality does not meet the required standards, the degraded quality impacts customer delivery causes customer dissatisfaction and results in lower margins. The biggest challenge was to identify the real root cause and devise a remedy for that.
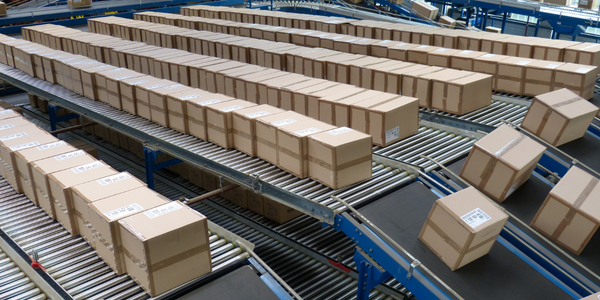
Case Study
Zenon the Ideal Basis for An Ergonomic HMI
KHS develops and produces machines and equipment for filling and packaging in the drinks industry. Because drinks manufacturing, filling and packaging consist of a number of highly complex processes, the user-friendly and intuitive operation of equipment is increasingly gaining in significance. In order to design these processes as simple as possible for the user, KHS decided to introduce a uniform, transparent and standardized solution to the company. The HMI interface should meet the requirement for people with different qualifications and enable them to work on a standard platform.
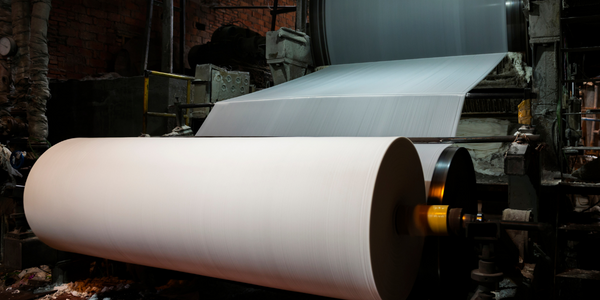
Case Study
Process Predictive Analysis in Pulp and Paper Mill
Common paper breaks consequently lead up to 60 minutes of downtime, delaying a potential $10K per hour of production value process. Thus, defective products cause financial and damage company's reputation. Improving quality and reducing defect rates can generate millions of dollars of revenue per year for your company.
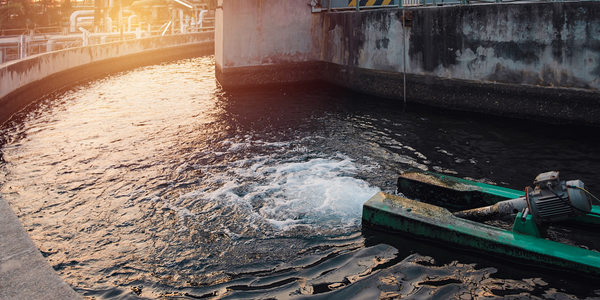
Case Study
Water Treatment Energy Management
Water pumping, treatment and conveyance are among the largest energy and cost outlays for many local and regional municipalities. Electricity time-of-use rates and peak pricing tariffs are driving those costs even higher. This case study describes how Monterey Regional Water Pollution Control Agency (MRWPCA) implemented a process data monitoring and control solution in order to analyze and optimize energy use, reduce deployment costs and save operational expenses.