下载PDF
Integrated CRM brings business benefits
技术
- 功能应用 - 企业资源规划系统 (ERP)
- 应用基础设施与中间件 - 数据交换与集成
适用行业
- 电子产品
- 设备与机械
适用功能
- 商业运营
- 销售与市场营销
- 质量保证
服务
- 系统集成
- 软件设计与工程服务
挑战
Extronics, a fast-growing specialist manufacturer and supplier of electrical and electronic equipment for hazardous areas, faced the challenge of managing customer relationships and integrating various business functions. The need for a robust and capable Customer Relationship Management (CRM) system that could seamlessly integrate with accounting, manufacturing, and back-office functions was paramount. The existing stand-alone CRM systems were not sufficient to meet the growing demands of the company, leading to inefficiencies and potential data silos. The company required a solution that could provide a comprehensive view of customer interactions, streamline the sales process, and enhance overall operational efficiency.
关于客户
Extronics is a Cheshire-based company specializing in the manufacturing and supply of electrical and electronic equipment designed for use in hazardous areas. The company has experienced rapid growth and is recognized for its expertise in providing high-quality, reliable products that meet stringent safety standards. Extronics serves a diverse range of industries, including oil and gas, pharmaceuticals, and chemicals, where safety and reliability are critical. The company is committed to innovation and continuous improvement, striving to meet the evolving needs of its customers through advanced technology and exceptional service. With a focus on customer satisfaction and operational excellence, Extronics has established itself as a trusted partner in the industry.
解决方案
Extronics implemented the WinMan CRM system, which is integrated into a complete ERP solution, to address its challenges. The WinMan CRM system is task-led, creating task lists for individuals, functions, and departments against each opportunity or project. This integration allows for seamless management of customer information, quote generation, and order processing within a single platform. The system stores information in various ways, ensuring that data related to companies, contacts, and projects are easily accessible and linked appropriately. Support cases, including technical support calls and nonconformances, are logged within the CRM, providing sales staff with insights into potential issues. The CRM data is utilized for forecasting and analysis, enabling production to make efficient forward purchasing decisions and track quote conversion rates. Additionally, the integrated document management and engineering change control capabilities provide traceability and link back to customer-specific requirements.
运营影响
数量效益
相关案例.
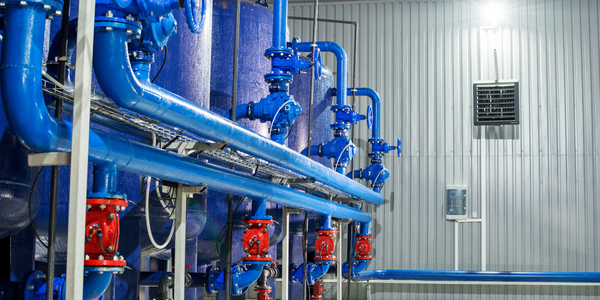
Case Study
Smart Water Filtration Systems
Before working with Ayla Networks, Ozner was already using cloud connectivity to identify and solve water-filtration system malfunctions as well as to monitor filter cartridges for replacements.But, in June 2015, Ozner executives talked with Ayla about how the company might further improve its water systems with IoT technology. They liked what they heard from Ayla, but the executives needed to be sure that Ayla’s Agile IoT Platform provided the security and reliability Ozner required.
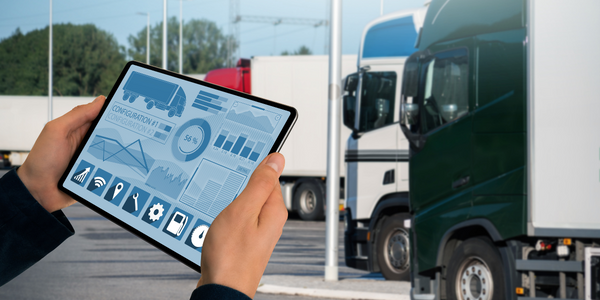
Case Study
IoT enabled Fleet Management with MindSphere
In view of growing competition, Gämmerler had a strong need to remain competitive via process optimization, reliability and gentle handling of printed products, even at highest press speeds. In addition, a digitalization initiative also included developing a key differentiation via data-driven services offers.
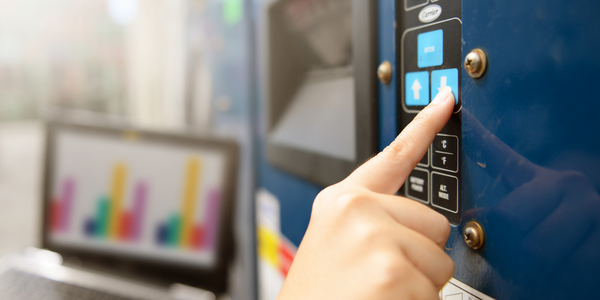
Case Study
Remote Temperature Monitoring of Perishable Goods Saves Money
RMONI was facing temperature monitoring challenges in a cold chain business. A cold chain must be established and maintained to ensure goods have been properly refrigerated during every step of the process, making temperature monitoring a critical business function. Manual registration practice can be very costly, labor intensive and prone to mistakes.
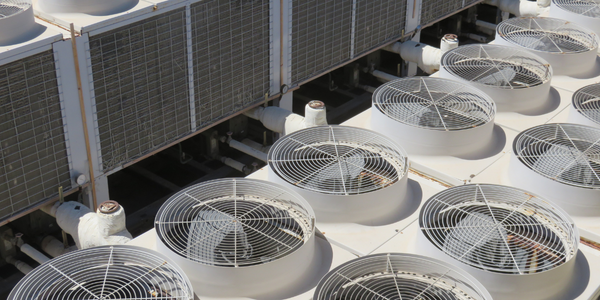
Case Study
Predictive Maintenance for Industrial Chillers
For global leaders in the industrial chiller manufacturing, reliability of the entire production process is of the utmost importance. Chillers are refrigeration systems that produce ice water to provide cooling for a process or industrial application. One of those leaders sought a way to respond to asset performance issues, even before they occur. The intelligence to guarantee maximum reliability of cooling devices is embedded (pre-alarming). A pre-alarming phase means that the cooling device still works, but symptoms may appear, telling manufacturers that a failure is likely to occur in the near future. Chillers who are not internet connected at that moment, provide little insight in this pre-alarming phase.
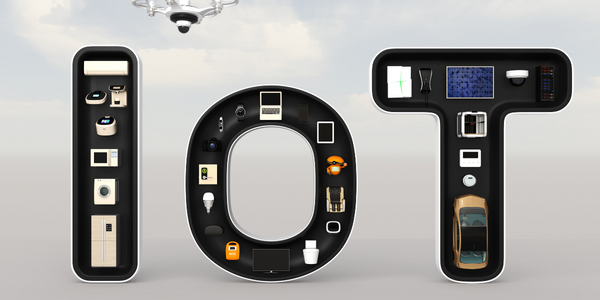
Case Study
Premium Appliance Producer Innovates with Internet of Everything
Sub-Zero faced the largest product launch in the company’s history:It wanted to launch 60 new products as scheduled while simultaneously opening a new “greenfield” production facility, yet still adhering to stringent quality requirements and manage issues from new supply-chain partners. A the same time, it wanted to increase staff productivity time and collaboration while reducing travel and costs.