下载PDF
Integrated, real-time data in OmegaCube ERP enables Marten Machining to optimize resources, control costs in job-shop environment
技术
- 功能应用 - 企业资源规划系统 (ERP)
- 功能应用 - 远程监控系统
适用行业
- 设备与机械
适用功能
- 质量保证
用例
- 库存管理
- 预测性维护
- 过程控制与优化
服务
- 系统集成
- 软件设计与工程服务
挑战
Change is such a constant at Marten Machining that David Marten, Vice President, describes the CNC machining business as operating in a “state of controlled emergency, every day”. Typical of a job-shop, short lead-times are the rule and ongoing developments alter planning at a rapid pace - every 5-10 minutes - with new jobs coming in, old jobs shipping out, order changes, materials changes, time card changes and tool changes, to name a few. A small but loyal customer base keeps the 16-employee milling and turning operation working at close to capacity. Marten Machining focuses on multi-axis machining, which allows it to machine precision parts with complicated features and contours with a limited amount of setup a production time, a must for medical device manufacturers, which account for the largest percentage of the company’s business. “Our medical devices customers, in particular, must meet pretty significant requirements for process and materials traceability, so we face some of those same requirements as well,” says Marten. “For that reason, and because of the short-run nature of our business, we needed to be able to access current shop floor data and track things like materials, orders and changes to the BOM in real-time.” According to Marten, the company’s legacy ERP system, a non-integrated mix of database programs for financials and a job-shop-specific application, was anything but real-time. “We really didn’t realize how much time we had been spending and how much trouble it had been entering and moving data from one place to another until we started running OmegaCube ERP. With manufacturing in one place and financials in another it was costing us a lot of time, and oftentimes information just never reached the shop-floor.”
关于客户
Marten Machining is a precision CNC machining company based in Stevens Point, WI, specializing in producing tooling and fixturing for customers across various industries, with a significant focus on medical device manufacturing. The company operates with a small but dedicated team of 16 employees, working at near full capacity to meet the demands of its loyal customer base. Marten Machining is known for its expertise in multi-axis machining, which allows it to create precision parts with complex features and contours efficiently. This capability is particularly crucial for their medical device manufacturing clients, who require stringent process and materials traceability. The company’s operations are characterized by short lead times and rapid changes, necessitating a highly adaptable and integrated system to manage the constant influx of new jobs, order changes, and material adjustments. The company’s commitment to quality and efficiency has driven its need for real-time data access and streamlined processes to maintain its competitive edge in the industry.
解决方案
The integration and associated real-time capabilities of OmegaCube ERP turned out to be a tremendous time saver for Marten Machining. “With OmegaCube it’s taking us much less time to do the day-to-day administration, like purchasing, tracking orders, creating jobs and sales orders, so we’ve freed extra time for our staff,” says Marten. The solution is so much a time saver, in fact, that Marten Machining was able to abandon plans to hire an additional person for data entry and instead employ an individual to take on value-add responsibilities on the manufacturing floor. Shop floor personnel are now accessing more data through OmegaCube as well, enabling them to be more involved and informed on delivery dates, order changes and process and quality issues. According to Marten, this newfound access to information on the shop floor allows front line employees to resolve issues before key managers need to get involved. “OmegaCube has allowed us to broaden responsibility, which makes the shop-floor easier to manage,” says Marten, while pointing out that enhanced process efficiency has made it easier for the company to handle more orders and more quotes, contributing to business growth. “As soon as jobs are completed everyone knows an order is ready to ship. An email is sent via mobile devices so people throughout the facility are notified no matter where they are. When new jobs are created people can immediately check BOMs and inventory levels, so tools and materials can be ordered within minutes.” Marten Machining is streamlining its operations with OmegaCube in another way - by automating previously manual processes. Timecards, for instance, were once hand written and the time-card data entered once a week. OmegaCube ERP now tracks jobs and employees on mobile devices as they log in and out of jobs or work centers - even employees required to work on multiple jobs at multiple workstations concurrently. This customized capability is vital to cost control, resource allocation and profitability and was not even an option with the previous system, given the degree of manual intervention it required.
运营影响
数量效益
相关案例.
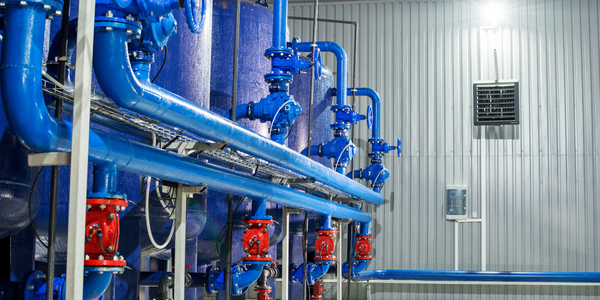
Case Study
Smart Water Filtration Systems
Before working with Ayla Networks, Ozner was already using cloud connectivity to identify and solve water-filtration system malfunctions as well as to monitor filter cartridges for replacements.But, in June 2015, Ozner executives talked with Ayla about how the company might further improve its water systems with IoT technology. They liked what they heard from Ayla, but the executives needed to be sure that Ayla’s Agile IoT Platform provided the security and reliability Ozner required.
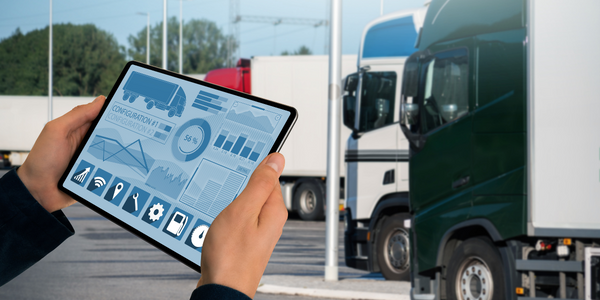
Case Study
IoT enabled Fleet Management with MindSphere
In view of growing competition, Gämmerler had a strong need to remain competitive via process optimization, reliability and gentle handling of printed products, even at highest press speeds. In addition, a digitalization initiative also included developing a key differentiation via data-driven services offers.
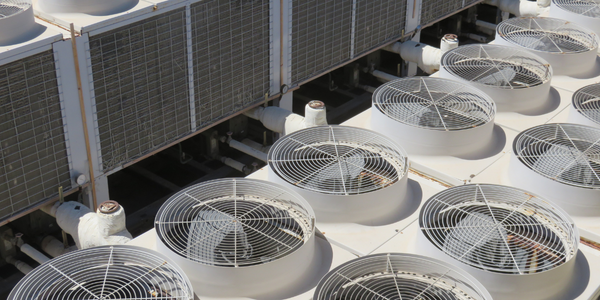
Case Study
Predictive Maintenance for Industrial Chillers
For global leaders in the industrial chiller manufacturing, reliability of the entire production process is of the utmost importance. Chillers are refrigeration systems that produce ice water to provide cooling for a process or industrial application. One of those leaders sought a way to respond to asset performance issues, even before they occur. The intelligence to guarantee maximum reliability of cooling devices is embedded (pre-alarming). A pre-alarming phase means that the cooling device still works, but symptoms may appear, telling manufacturers that a failure is likely to occur in the near future. Chillers who are not internet connected at that moment, provide little insight in this pre-alarming phase.
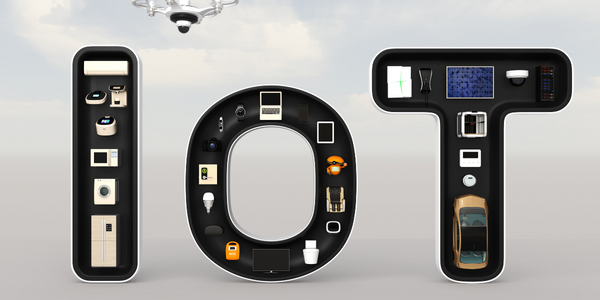
Case Study
Premium Appliance Producer Innovates with Internet of Everything
Sub-Zero faced the largest product launch in the company’s history:It wanted to launch 60 new products as scheduled while simultaneously opening a new “greenfield” production facility, yet still adhering to stringent quality requirements and manage issues from new supply-chain partners. A the same time, it wanted to increase staff productivity time and collaboration while reducing travel and costs.
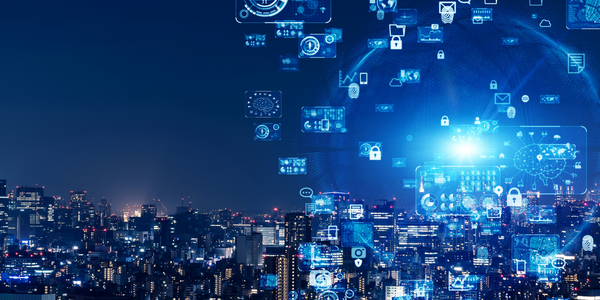
Case Study
Integration of PLC with IoT for Bosch Rexroth
The application arises from the need to monitor and anticipate the problems of one or more machines managed by a PLC. These problems, often resulting from the accumulation over time of small discrepancies, require, when they occur, ex post technical operations maintenance.
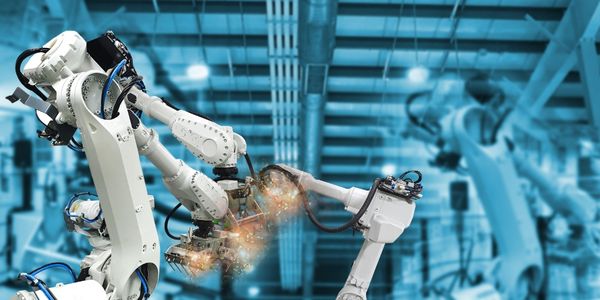
Case Study
Robot Saves Money and Time for US Custom Molding Company
Injection Technology (Itech) is a custom molder for a variety of clients that require precision plastic parts for such products as electric meter covers, dental appliance cases and spools. With 95 employees operating 23 molding machines in a 30,000 square foot plant, Itech wanted to reduce man hours and increase efficiency.