下载PDF
Lannoo Group Publishers discloses wealth of business data using QlikView
技术
- 分析与建模 - 实时分析
适用功能
- 销售与市场营销
用例
- 实时定位系统 (RTLS)
- 供应链可见性(SCV)
服务
- 数据科学服务
挑战
Lannoo Group Publishers, a publishing house specializing in non-fiction books and stationery, was facing challenges in data collection, analysis, and report generation. The existing Baan ERP system was slow and produced very basic reports that often raised new questions. To answer these questions, a programmer had to be called in each time, which was not efficient. The Oracle database contained seventeen gigabytes of data and it took the system at least fifteen minutes to produce statistics for any given year. The company was looking for a Business Intelligence (BI) package that could provide more insight into sales, customer, and item information.
关于客户
Lannoo Group Publishers specializes in non-fiction books and stationery. The group comprises of two divisions (Books & Multimedia and Paper Items & Stationery), a Staff & Support Department, which is responsible for administration, finance, HRM and ICT, a distribution center (DistriMedia) and a design studio (Studio Lannoo). Since 2005, it has also been the sole representative of Michelin Travel Publications in the Benelux. Lannoo is based in Belgium (Tielt, Leuven, Brussels) and the Netherlands (Arnhem). It employs a staff of 165 and generates sales of €45 million.
解决方案
Lannoo Group Publishers deployed twelve QlikView applications in less than six weeks. With QlikView, the publishing house now has 68 employees analyzing customers, products, inventory stock, prices, sales, margins, and complaints – all focused on driving corporate profitability. With QlikView Server (64-bit), Lannoo Group easily supports security and visibility while handling and manipulating large data volumes in order to get up-to-date insight into the corporate performance. The QlikView implementation started at the end of August 2006, and by mid-November, the modules were being used by 48 people. This number increased to 68 in July 2007 when the Michelin representatives in Belgium were added to the user base.
运营影响
相关案例.
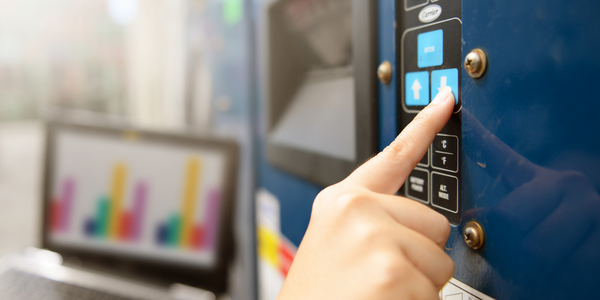
Case Study
Remote Temperature Monitoring of Perishable Goods Saves Money
RMONI was facing temperature monitoring challenges in a cold chain business. A cold chain must be established and maintained to ensure goods have been properly refrigerated during every step of the process, making temperature monitoring a critical business function. Manual registration practice can be very costly, labor intensive and prone to mistakes.
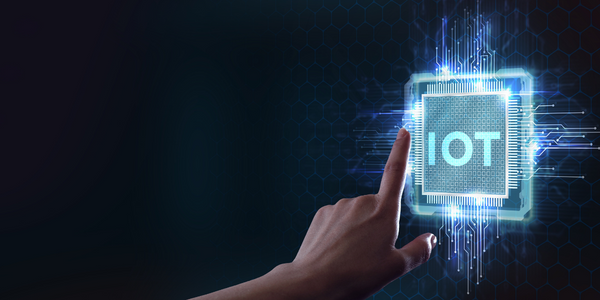
Case Study
Leading Tools Manufacturer Transforms Operations with IoT
Stanley Black & Decker required transparency of real-time overall equipment effectiveness and line productivity to reduce production line change over time.The goal was to to improve production to schedule, reduce actual labor costs and understanding the effects of shift changes and resource shifts from line to line.
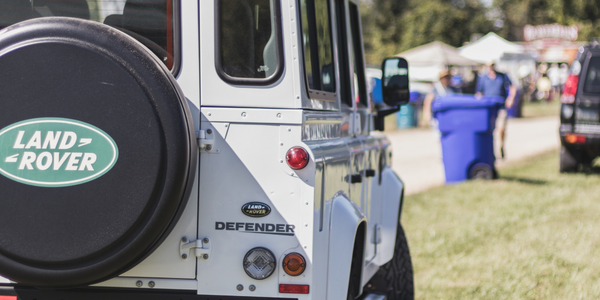
Case Study
Jaguar Land Rover Speeds Order-to-Cash Cycle
At Jaguar Land Rover, vehicles physically move around the facility for testing, configuration setting, rework and rectification, leading to a longer search time to get each vehicle to its next process facility. The main goal is to minimize the vehicles' dwell time between end of line and the delivery chain which was previously a manually intensive process. Jaguar Land Rover's goal was to build on the success of an earlier RFID project and improve the efficiency of delivering vehicles to meet dealer orders.
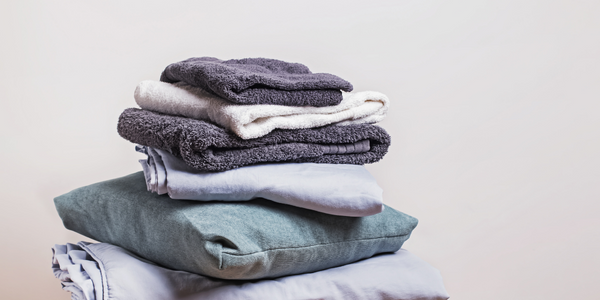
Case Study
Retail Uses RFID to Enable Cold Chain Monitoring
Like most grocery retailers, Hy-Vee is faced with the challenge of providing the highest quality products to its shoppers. Shoppers want the longest possible shelf life from perishable products and expect a consistent product experience each time they shop. Controlling the quality of products sold leads to shopper loyalty, which is of paramount importance to the success of Hy-Vee. Before products arrive in stores, Hy-Vee's distribution centers (DCs) handle items including dairy products, fresh meats, seafood, deli items, produce and frozen goods, all of which have different temperature needs and sensitivities. During transit from suppliers to DCs, Hy-Vee has limited visibility and temperature management abilities due to large amount of supplier managed transportation. For instance, during a week-long transit, a supplier's carrier equipment may malfunction, causing an item to thaw and then refreeze once repairs are made. Hy-Vee sought help from TempTRIP, an RFID solution provider that focuses on shipping, storage, receiving, and temperature control. TempTRIP's EPC RFID tags use Impinj chips to monitor and report temperature readings throughout the shipping and receiving process. The tags can also be re-configured and re-used, a unique feature within the current market of temperature monitoring devices.