下载PDF
Maxima Racing Oils Case Study
技术
- 功能应用 - 企业资源规划系统 (ERP)
- 功能应用 - 仓库管理系统 (WMS)
适用行业
- 化学品
适用功能
- 物流运输
- 仓库和库存管理
用例
- 库存管理
- 供应链可见性(SCV)
服务
- 系统集成
挑战
Maxima Racing Oils, a renowned brand in the power sports racing industry, was grappling with warehouse management and inventory visibility issues due to its legacy ERP and paper-based spreadsheets. The company's sales surged during the COVID-19 pandemic, exacerbating these issues and highlighting the need for more modern ERP and WMS solutions. Maxima's operation was riddled with pain points, including the inability to generate reports without the system freezing, lack of visibility into raw material stock levels, stock committed, and stock allocated, and no live correlation of raw material inventory needed for a work order to produce finished goods. Other issues included the lack of automatic creation of bills of lading (BOLs) and the error-prone, human-based system of cycling through the oldest inventory first for both raw materials and finished goods.
关于客户
Maxima Racing Oils is a highly sought-after brand in the power sports racing industry. The company was established in 1979 and is based in Southern California. It operates seven warehouses and specializes in the formulation, development, manufacturing, and distribution of high-performance engine oils, suspension fluids, coolants, care products, and accessories for the sport and racing communities. Maxima's products are recognized for their quality and performance, making the brand a favorite among power sports racing enthusiasts.
解决方案
To address its warehouse and visibility issues, Maxima upgraded to NetSuite and implemented the ShipHawk WMS simultaneously. The company's management sought complete visibility into warehouse operations, including available warehouse space, rack availability, picker activity, and item outflow, and aimed to automate all associated administrative functions. Maxima's new ERP and WMS solution provided the visibility it lacked and automated transactions that drive and trigger other transactions. The company now has full visibility into the shipment and warehouse fulfillment process flows. Staff can create item fulfillments stored against sales orders, which are then turned into a shipped pallet or parcel shipment. This makes it easy to see how to allocate goods to meet customer priorities. The solution also simplifies the onboarding of new and temporary seasonal workers.
运营影响
相关案例.
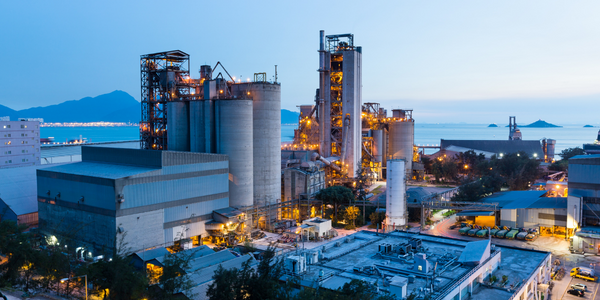
Case Study
Honeywell - Tata Chemicals Improves Data Accessibility with OneWireless
Tata was facing data accessibility challenges in the cement plant control room tapping signals from remote process control areas and other distant locations, including the gas scrubber. Tata needed a wireless solution to extend its control network securely to remote locations that would also provide seamless communication with existing control applications.
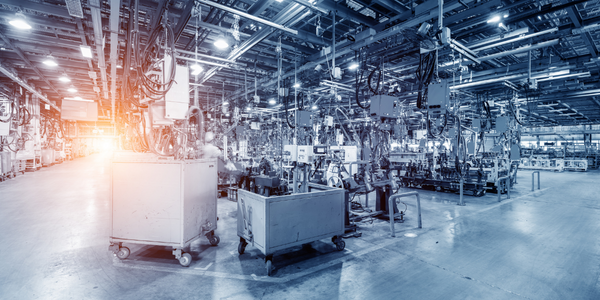
Case Study
Advanced Elastomer Systems Upgrades Production
In order to maintain its share of the international market for thermoplastic elastomers AES recently expanded its Florida plant by adding a new production line. While the existing lines were operating satisfactorily using a PROVOX distributed control system with traditional analog I/O, AES wanted advanced technology on the new line for greater economy, efficiency, and reliability. AES officials were anxious to get this line into production to meet incoming orders, but two hurricanes slowed construction.

Case Study
Wireless GPS Tracking & Security Monitoring
Enhancing the security of hazardous freight and ensuring compliance with Homeland Security’s Transportation Security Administration mandate that all trains carrying chemicals capable of creating a toxic inhalation condition are equipped with on-board safety monitoring systems.
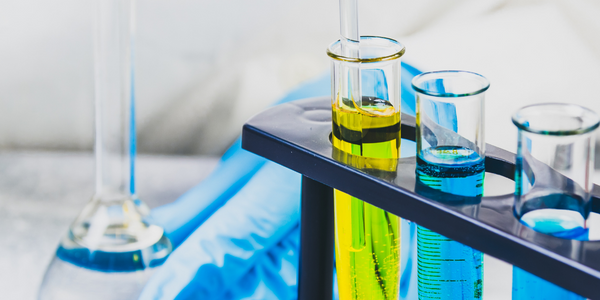
Case Study
Field Device Asset Management For Chemical Company in China
Chinese chemical subsidiary of multinational corporation serves customers throughout the world. Sales offices and research and technology centers are strategically located to provide rapid response to customer requests. Just two workers were assigned to maintain thousands of intelligent instruments in three production units, so they could do little more than react to device issues as they appeared. This costly maintenance method inevitably led to unexpected downtime when a critical instrument failed. Plant management recognized the need to change from reactive to predictive maintenance for all assets, including instruments and control valves, but help was needed in implementing such a technology-based initiative.
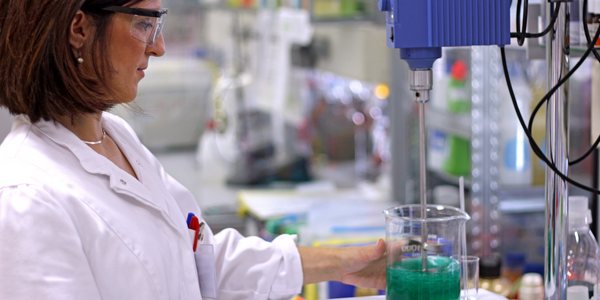
Case Study
Industrial Workforce Mobility for Improved Safety & Operations
Huntsman Corporation, a global manufacturer and marketer of differentiated chemicals, undertook an aggressive program to eliminate injuries, product defects, and environmental releases at their Port Neches facility. Termed “Project Zero”, this program required a completely mobile solution to empower operations and maintenance personnel to capture defects, track work progress and make process and safety related decisions in real-time.