下载PDF
Motoring toward the Internet-of-Things era
技术
- 分析与建模 - 实时分析
- 平台即服务 (PaaS) - 连接平台
适用行业
- 汽车
- 医疗保健和医院
适用功能
- 产品研发
- 质量保证
用例
- 预测性维护
- 实时定位系统 (RTLS)
- 远程资产管理
服务
- 软件设计与工程服务
- 系统集成
挑战
ASPINA, a century-old manufacturer, was looking to embrace the data revolution and the Internet-of-Things era. The company had a new business development unit based in California, which was investigating ways to package hardware and software together. The company was considering building a homegrown IoT solution and was looking for a partner to power this intelligent transformation. They needed a solution that could provide fast visibility over remote assets, was cost-competitive, and offered edge computation. The company was also looking to target customers whose future products would live or die through connectivity, particularly companies developing IoT-enabled medical devices.
关于客户
ASPINA is a global precision manufacturer that designs, develops, and supplies motors and other top-quality components to business customers across a range of industries. Headquartered in Ueda, Japan, it was established in 1918 as a silk yarn manufacturer. In September 2019, Shinano Kenshi migrated its corporate brand to ASPINA to continue to strive for even greater contributions on a global scale. Following its mission statement, “Shaping the hopes for tomorrow and providing comfort to the world’s people,” the company focuses on how it can help better the lives of people through its technology. With a team of 5,000 employees across Asia, North America, and Europe its 2018 sales reached over $400 million.
解决方案
ASPINA chose Cumulocity IoT, Software AG’s industry-leading, open IoT platform, to power its intelligent transformation. Cumulocity offered the best mix of essential features, including the power to provide fast visibility over remote assets, a simple architecture, cost competitiveness, and edge computation. After signing a deal in 2018, ASPINA’s business development unit began building a sample smart device to test its newfound capabilities. After three months, it had a product—a dashboard-connected prototype industrial blower. ASPINA is now in advanced stages of discussion with three companies over what it hopes will soon become commercialized smart products—including a wearable blood pressure monitor that creates models to predict when a patient is about to undergo heart failure.
运营影响
数量效益
相关案例.
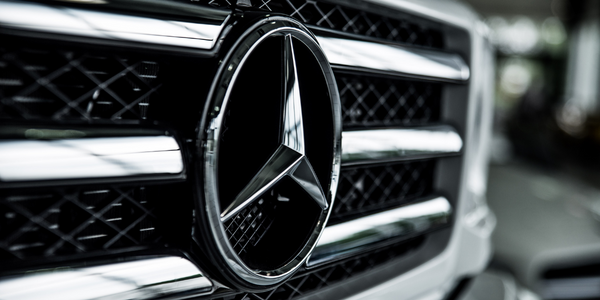
Case Study
Integral Plant Maintenance
Mercedes-Benz and his partner GAZ chose Siemens to be its maintenance partner at a new engine plant in Yaroslavl, Russia. The new plant offers a capacity to manufacture diesel engines for the Russian market, for locally produced Sprinter Classic. In addition to engines for the local market, the Yaroslavl plant will also produce spare parts. Mercedes-Benz Russia and his partner needed a service partner in order to ensure the operation of these lines in a maintenance partnership arrangement. The challenges included coordinating the entire maintenance management operation, in particular inspections, corrective and predictive maintenance activities, and the optimizing spare parts management. Siemens developed a customized maintenance solution that includes all electronic and mechanical maintenance activities (Integral Plant Maintenance).
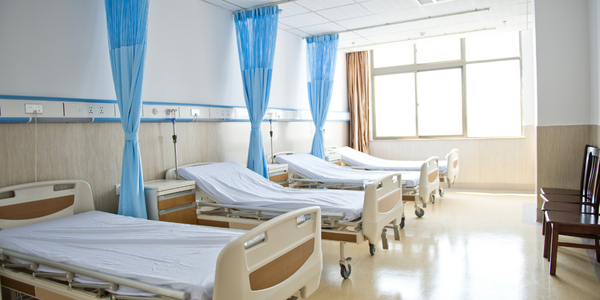
Case Study
Hospital Inventory Management
The hospital supply chain team is responsible for ensuring that the right medical supplies are readily available to clinicians when and where needed, and to do so in the most efficient manner possible. However, many of the systems and processes in use at the cancer center for supply chain management were not best suited to support these goals. Barcoding technology, a commonly used method for inventory management of medical supplies, is labor intensive, time consuming, does not provide real-time visibility into inventory levels and can be prone to error. Consequently, the lack of accurate and real-time visibility into inventory levels across multiple supply rooms in multiple hospital facilities creates additional inefficiency in the system causing over-ordering, hoarding, and wasted supplies. Other sources of waste and cost were also identified as candidates for improvement. Existing systems and processes did not provide adequate security for high-cost inventory within the hospital, which was another driver of cost. A lack of visibility into expiration dates for supplies resulted in supplies being wasted due to past expiry dates. Storage of supplies was also a key consideration given the location of the cancer center’s facilities in a dense urban setting, where space is always at a premium. In order to address the challenges outlined above, the hospital sought a solution that would provide real-time inventory information with high levels of accuracy, reduce the level of manual effort required and enable data driven decision making to ensure that the right supplies were readily available to clinicians in the right location at the right time.
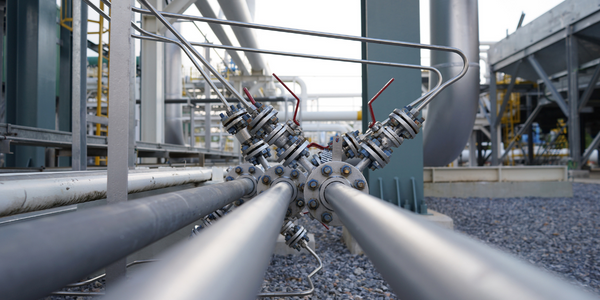
Case Study
Gas Pipeline Monitoring System for Hospitals
This system integrator focuses on providing centralized gas pipeline monitoring systems for hospitals. The service they provide makes it possible for hospitals to reduce both maintenance and labor costs. Since hospitals may not have an existing network suitable for this type of system, GPRS communication provides an easy and ready-to-use solution for remote, distributed monitoring systems System Requirements - GPRS communication - Seamless connection with SCADA software - Simple, front-end control capability - Expandable I/O channels - Combine AI, DI, and DO channels