下载PDF
Packaging Company Achieves 58% Reduction in Lost-Time Accidents with Intelex Safety Incident Software
技术
- 功能应用 - 远程监控系统
适用行业
- 包装
适用功能
- 质量保证
用例
- 远程资产管理
服务
- 系统集成
- 培训
挑战
The Smurfit Kappa Group, a global leader in the paper-based packaging industry, was facing a challenge with its safety incident tracking system. The company operates dozens of manufacturing sites across the UK, each using their own variation of a paper-based safety incident tracking system. This disjointed approach was inefficient and inconsistent. The company wanted to implement a web-based, user-friendly software system to track and manage their safety incidents consistently across their UK manufacturing sites. The system needed to be accessible to all employees at each site and allow them to easily record incidents, hazards and near-misses. Management also required monthly reports from each site containing metrics such as Days Since Lost Time Injury and Accident Frequency and Severity Rates.
关于客户
The Smurfit Kappa Group is a world leader in the paper-based packaging industry. The company produces over 12 million tons of paper annually and operates over 300 plants and mills worldwide. Headquartered in Dublin, Ireland, The Smurfit Kappa Group employs more than 40,000 employees with operations in Europe, Latin America, Canada, Singapore, USA and South Africa. The products manufactured by the company include containerboard, corrugated containers, boxboard, solidboard, graphicboard, and other paper-based packaging products.
解决方案
The Smurfit Kappa Group implemented the Intelex Safety Incidents Reporting application, which operates on a web-based platform. This provided a centralized reporting system, accessible via the web by any employee at any location. Employee IDs were imported into the system and Smurfit Kappa’s paper incident form was translated into an easy-to-complete digital version. A simple user interface was configured so that upon logging in, users are presented with the incident form, ready to be completed and submitted. An initial Intelex training session for Safety and Environmental Managers from each geographic location was conducted, after which they were able to train the users at their respected locations. As user confidence has grown more modules are set to be launched to improve other aspects of the company and further drive forward continual improvement.
运营影响
数量效益
相关案例.
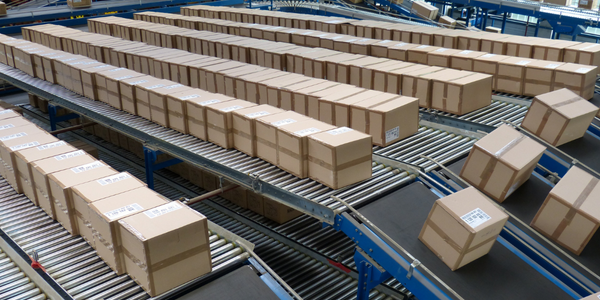
Case Study
IoT Data Analytics Case Study - Packaging Films Manufacturer
The company manufactures packaging films on made to order or configure to order basis. Every order has a different set of requirements from the product characteristics perspective and hence requires machine’s settings to be adjusted accordingly. If the film quality does not meet the required standards, the degraded quality impacts customer delivery causes customer dissatisfaction and results in lower margins. The biggest challenge was to identify the real root cause and devise a remedy for that.
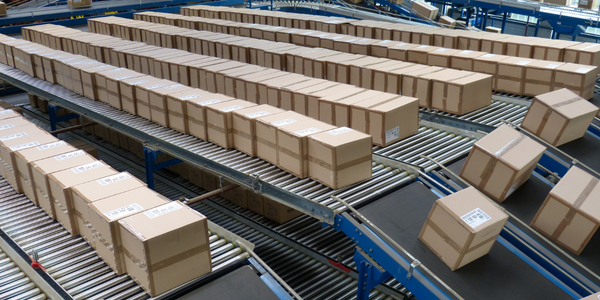
Case Study
Zenon the Ideal Basis for An Ergonomic HMI
KHS develops and produces machines and equipment for filling and packaging in the drinks industry. Because drinks manufacturing, filling and packaging consist of a number of highly complex processes, the user-friendly and intuitive operation of equipment is increasingly gaining in significance. In order to design these processes as simple as possible for the user, KHS decided to introduce a uniform, transparent and standardized solution to the company. The HMI interface should meet the requirement for people with different qualifications and enable them to work on a standard platform.
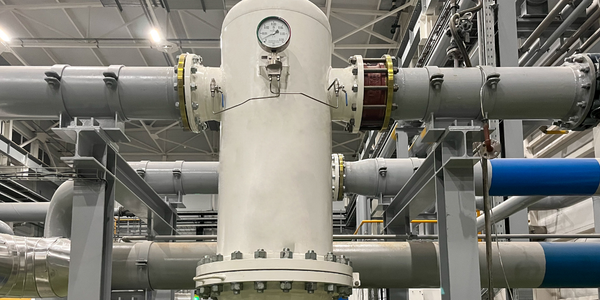
Case Study
Sparks Dynamics Assists Atlas Container Secure a $15,000 BGE Energy Rebate
The ReMASTER Compressed Air Monitoring system was installed in 2015. This system is capable of monitoring compressed air system parameters on a continuous basis and transferring that information to a cloud server which can be accessed by Atlas Container personnel, Industrial Diagnostics and Sparks Dynamics. This information was collected into a database which can be exported to an Excel spreadsheet or displayed graphically using Sparks Dynamics ViewMaster Software. The average annual compressed air electricity expense was estimated to be approximately $116,000. This is based on an incremental $/KWh electric rate of $.091 per KWh and an estimated compressed air energy consumption of 1,279,200 KWH. The implementation phase of Energy Conservation Measures (ECMs) for the Compressed Air System included: • Identification and repair of compressed air leaks • Understanding of compressed air usage per manufacturing machine and installation of shut off valves when the machines are no longer in production mode • Identification of misapplications of compressed air to include blow offs, venturis, and cooling scenarios • Understand system pressure requirements and potential installation of point of use pressure regulation.
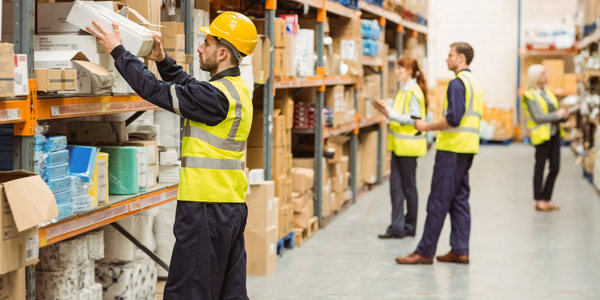
Case Study
Automated Pallet Labeling Solution for SPR Packaging
SPR Packaging, an American supplier of packaging solutions, was in search of an automated pallet labeling solution that could meet their immediate and future needs. They aimed to equip their lines with automatic printer applicators, but also required a solution that could interface with their accounting software. The challenge was to find a system that could read a 2D code on pallets at the stretch wrapper, track the pallet, and flag any pallets with unread barcodes for inspection. The pallets could be single or double stacked, and the system needed to be able to differentiate between the two. SPR Packaging sought a system integrator with extensive experience in advanced printing and tracking solutions to provide a complete traceability system.
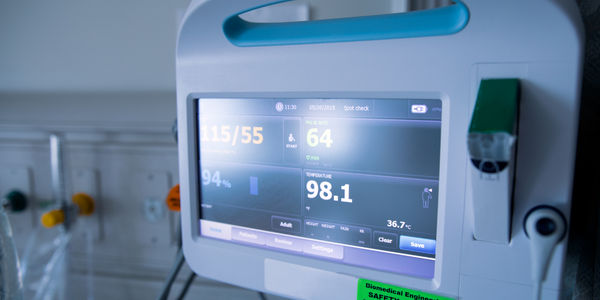
Case Study
Mondi Implements Statistics-Based Health Monitoring and Predictive Maintenance
The extrusion and other machines at Mondi’s plant are large and complex, measuring up to 50 meters long and 15 meters high. Each machine is controlled by up to five programmable logic controllers (PLCs), which log temperature, pressure, velocity, and other performance parameters from the machine’s sensors. Each machine records 300–400 parameter values every minute, generating 7 gigabytes of data daily.Mondi faced several challenges in using this data for predictive maintenance. First, the plant personnel had limited experience with statistical analysis and machine learning. They needed to evaluate a variety of machine learning approaches to identify which produced the most accurate results for their data. They also needed to develop an application that presented the results clearly and immediately to machine operators. Lastly, they needed to package this application for continuous use in a production environment.
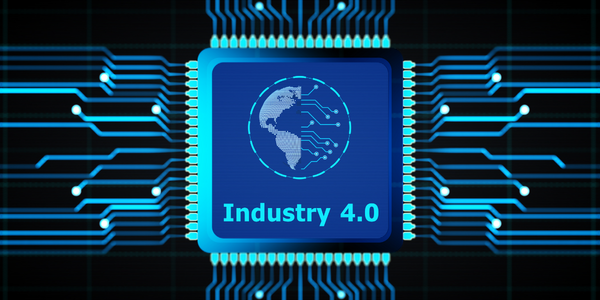
Case Study
Industry 4.0 at ALPLA: Enhancing Factory Efficiency with IoT
ALPLA, a global leader in packaging solutions, faced several challenges as the complexity of their production machinery increased. The need for highly trained specialists in each factory led to higher personnel costs, difficulties in recruiting experienced talent at each location, and costly personnel turnover. Furthermore, less experienced operators running the machines sub-optimally impacted resource consumption and overall equipment effectiveness (OEE). ALPLA also faced the challenge of monitoring visual inspection systems in every line of their plants, which was almost impossible to do manually. In 2016, ALPLA decided to use data from the 900 different types of embedded sensors in each factory to address these issues. However, their initial choice of SQL Server as the data store for the sensor data proved inadequate, as it was unable to cope with their data requirements.