下载PDF
Petrochemical Production Facility Drives Value and Maximizes Return with Non-linear APC
技术
- 应用基础设施与中间件 - API 集成与管理
适用行业
- 化学品
适用功能
- 流程制造
用例
- 过程控制与优化
- 质量预测分析
服务
- 系统集成
- 软件设计与工程服务
挑战
The Siam Cement Group (SCG), the second largest company in Thailand, sought to enhance its existing production capabilities by implementing innovative non-linear Advanced Process Control (APC) software. The focus of this project was on the downstream petrochemical production lines of Thai Polyethylene Co., Ltd. & Thai Polypropylene Co., Ltd. These facilities produce a wide range of polyethylene, polypropylene, and high-value added products. The challenge was to drive enterprise value and maximize return on assets with non-linear APC and enable engineers to gain proficiency and extend APC applications across multiple polyolefin manufacturing units.
关于客户
The Siam Cement Group (SCG) is the second largest company in Thailand, manufacturing and supplying a full range of petrochemical products: upstream, intermediate, and downstream petrochemicals. The focus of this project was on the downstream petrochemical production lines of Thai Polyethylene Co., Ltd. & Thai Polypropylene Co., Ltd. These facilities produce a wide range of polyethylene, polypropylene, and high-value added products. SCG sought to enhance existing production capabilities by implementing innovative non-linear APC software from AspenTech.
解决方案
A standardized APC design was applied to all major units to utilize a collaborative implementation scheme to maximize knowledge transfer and replicate success in future developments. The software suite included Aspen Non-linear Controller, Polymer Inferential Properties, Recipe Management, Process Sequencer, and APC Performance Monitoring. SCG staff was intimately involved during development and commissioning, enabling engineers to obtain the skills required to design, maintain, and modify the APC controller when a process changes or new products are developed.
运营影响
数量效益
相关案例.
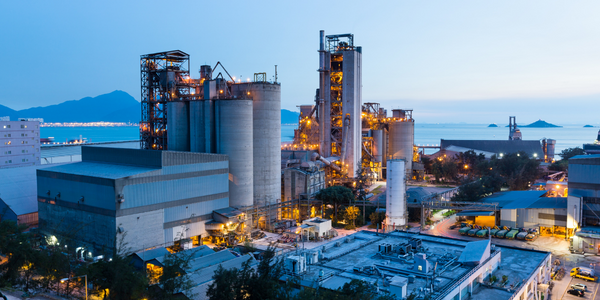
Case Study
Honeywell - Tata Chemicals Improves Data Accessibility with OneWireless
Tata was facing data accessibility challenges in the cement plant control room tapping signals from remote process control areas and other distant locations, including the gas scrubber. Tata needed a wireless solution to extend its control network securely to remote locations that would also provide seamless communication with existing control applications.
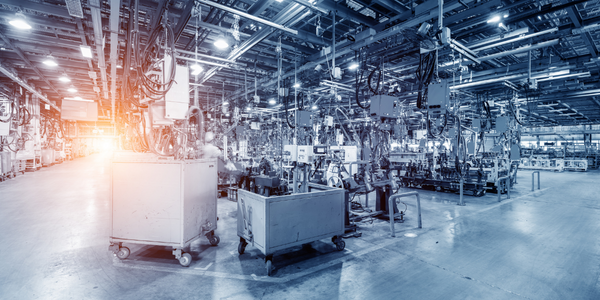
Case Study
Advanced Elastomer Systems Upgrades Production
In order to maintain its share of the international market for thermoplastic elastomers AES recently expanded its Florida plant by adding a new production line. While the existing lines were operating satisfactorily using a PROVOX distributed control system with traditional analog I/O, AES wanted advanced technology on the new line for greater economy, efficiency, and reliability. AES officials were anxious to get this line into production to meet incoming orders, but two hurricanes slowed construction.

Case Study
Wireless GPS Tracking & Security Monitoring
Enhancing the security of hazardous freight and ensuring compliance with Homeland Security’s Transportation Security Administration mandate that all trains carrying chemicals capable of creating a toxic inhalation condition are equipped with on-board safety monitoring systems.
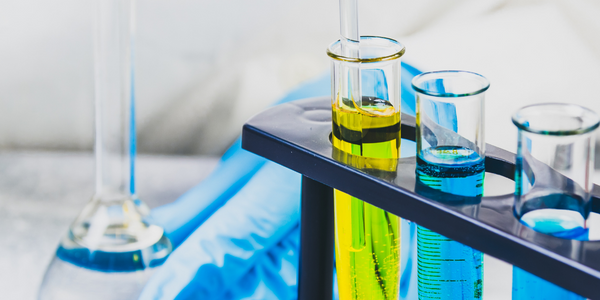
Case Study
Field Device Asset Management For Chemical Company in China
Chinese chemical subsidiary of multinational corporation serves customers throughout the world. Sales offices and research and technology centers are strategically located to provide rapid response to customer requests. Just two workers were assigned to maintain thousands of intelligent instruments in three production units, so they could do little more than react to device issues as they appeared. This costly maintenance method inevitably led to unexpected downtime when a critical instrument failed. Plant management recognized the need to change from reactive to predictive maintenance for all assets, including instruments and control valves, but help was needed in implementing such a technology-based initiative.
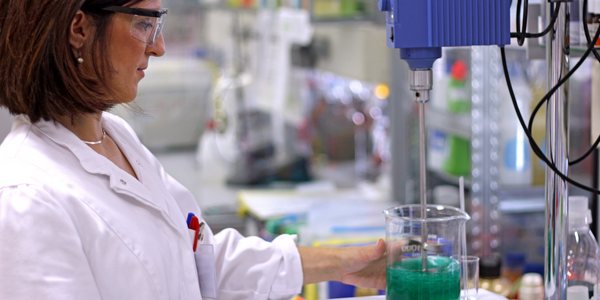
Case Study
Industrial Workforce Mobility for Improved Safety & Operations
Huntsman Corporation, a global manufacturer and marketer of differentiated chemicals, undertook an aggressive program to eliminate injuries, product defects, and environmental releases at their Port Neches facility. Termed “Project Zero”, this program required a completely mobile solution to empower operations and maintenance personnel to capture defects, track work progress and make process and safety related decisions in real-time.