下载PDF
PHC Northwest, Inc. Using SOLIDWORKS Solutions to Develop Products that Help People with Disabilities
技术
- 功能应用 - 产品生命周期管理系统 (PLM)
- 分析与建模 - 预测分析
- 功能应用 - 制造执行系统 (MES)
适用行业
- 消费品
- 医疗保健和医院
适用功能
- 产品研发
用例
- 自动化制造系统
- 预测性维护
服务
- 软件设计与工程服务
- 系统集成
挑战
Establish an efficient product development and manufacturing capability to create products and offer services that generate self-sustaining revenues to support its mission of providing educational, training, and job opportunities for people with disabilities.
关于客户
What began in 1951 as a small, private school for children with disabilities in Portland, Oregon, has blossomed into an expanding, self-sustaining enterprise that provides broad-based educational, training, and job opportunities for people with developmental, physical, and mental disabilities. PHC Northwest (PHCNW) has grown into a dynamic and forward-thinking industry leader. Its diversified business lines allow it to help employees develop the technical skills required to earn living wages in a variety of occupations, including product development, manufacturing, industrial, clerical, janitorial, warehousing, order fulfillment, and landscaping services. PHCNW focuses on empowerment—both as an enterprise and for the individuals it serves. The nonprofit organization is committed to generating its own revenue and receives no government funding. Because PHCNW empowers its 750 employees to work and pay taxes, they’re able to raise families, build careers, and live independently without having to rely on government-funded benefits.
解决方案
Choosing the right product design and manufacturing platform to launch new products was of paramount importance in helping PHCNW compete successfully. The organization chose SOLIDWORKS® solutions, implementing SOLIDWORKS Professional design, SOLIDWORKS Simulation Professional analysis, and SOLIDWORKS Electrical 3D™ electrical design software. PHCNW chose SOLIDWORKS solutions because they are easy to use, integrate directly with MasterCAM® manufacturing software, and provide the range of capabilities required to develop innovative products. Using SOLIDWORKS solutions, PHCNW has developed and launched the Beyond Limitations (BL) line of LED-based lighting products. The organization has expanded its product offering into five distinct lines, including indoor, outdoor, facility, and pool and fountain lighting, as well as a line of LED light engines. PHCNW products have done well in the market. PHCNW is not only a major supplier to the state of Oregon—supplying lighting for streets, parking garages, and other facilities—but also has installations around the world, including British Columbia, Texas, and the Doha International Airport in Qatar.
运营影响
数量效益
相关案例.
.png)
Case Study
Improving Vending Machine Profitability with the Internet of Things (IoT)
The vending industry is undergoing a sea change, taking advantage of new technologies to go beyond just delivering snacks to creating a new retail location. Intelligent vending machines can be found in many public locations as well as company facilities, selling different types of goods and services, including even computer accessories, gold bars, tickets, and office supplies. With increasing sophistication, they may also provide time- and location-based data pertaining to sales, inventory, and customer preferences. But at the end of the day, vending machine operators know greater profitability is driven by higher sales and lower operating costs.
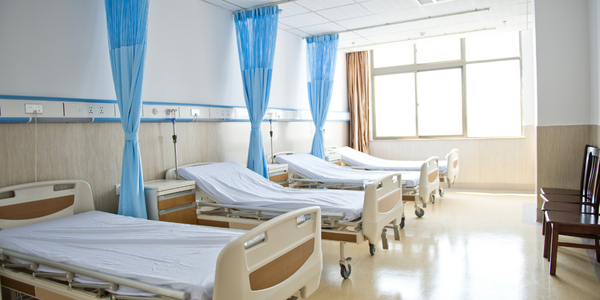
Case Study
Hospital Inventory Management
The hospital supply chain team is responsible for ensuring that the right medical supplies are readily available to clinicians when and where needed, and to do so in the most efficient manner possible. However, many of the systems and processes in use at the cancer center for supply chain management were not best suited to support these goals. Barcoding technology, a commonly used method for inventory management of medical supplies, is labor intensive, time consuming, does not provide real-time visibility into inventory levels and can be prone to error. Consequently, the lack of accurate and real-time visibility into inventory levels across multiple supply rooms in multiple hospital facilities creates additional inefficiency in the system causing over-ordering, hoarding, and wasted supplies. Other sources of waste and cost were also identified as candidates for improvement. Existing systems and processes did not provide adequate security for high-cost inventory within the hospital, which was another driver of cost. A lack of visibility into expiration dates for supplies resulted in supplies being wasted due to past expiry dates. Storage of supplies was also a key consideration given the location of the cancer center’s facilities in a dense urban setting, where space is always at a premium. In order to address the challenges outlined above, the hospital sought a solution that would provide real-time inventory information with high levels of accuracy, reduce the level of manual effort required and enable data driven decision making to ensure that the right supplies were readily available to clinicians in the right location at the right time.
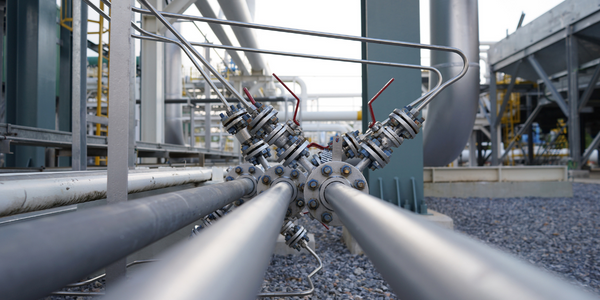
Case Study
Gas Pipeline Monitoring System for Hospitals
This system integrator focuses on providing centralized gas pipeline monitoring systems for hospitals. The service they provide makes it possible for hospitals to reduce both maintenance and labor costs. Since hospitals may not have an existing network suitable for this type of system, GPRS communication provides an easy and ready-to-use solution for remote, distributed monitoring systems System Requirements - GPRS communication - Seamless connection with SCADA software - Simple, front-end control capability - Expandable I/O channels - Combine AI, DI, and DO channels
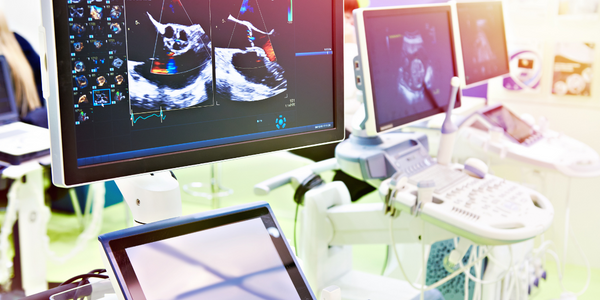
Case Study
Driving Digital Transformations for Vitro Diagnostic Medical Devices
Diagnostic devices play a vital role in helping to improve healthcare delivery. In fact, an estimated 60 percent of the world’s medical decisions are made with support from in vitrodiagnostics (IVD) solutions, such as those provided by Roche Diagnostics, an industry leader. As the demand for medical diagnostic services grows rapidly in hospitals and clinics across China, so does the market for IVD solutions. In addition, the typically high cost of these diagnostic devices means that comprehensive post-sales services are needed. Wanteed to improve three portions of thr IVD:1. Remotely monitor and manage IVD devices as fixed assets.2. Optimizing device availability with predictive maintenance.3. Recommending the best IVD solution for a customer’s needs.