下载PDF
Plastic Spoons Case study: Injection Moulding
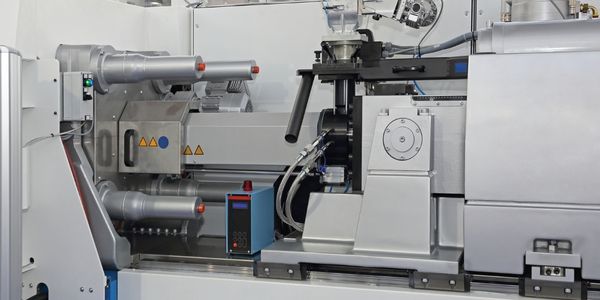
技术
- 机器人 - 关节机器人
适用行业
- 塑料
适用功能
- 离散制造
用例
- 自动化制造系统
挑战
为了满足客户的期望,提供各种各样的包装单元,每包 36 到 1000 个勺子,需要建造一条新的生产和包装线。 DeSter 希望通过这条新生产线实现更高的生产能力、更短的循环时间和高度的操作员友好性。
客户
德斯特
关于客户
DeSter 在塑料杯、马克杯、盘子和餐具方面处于世界领先地位,在全球拥有 1,000 多名员工。
解决方案
一条新的塑料勺生产线是根据市场需求建造的。生产线的核心是一台400吨的注塑机,配备144个复合模具。为了从模具中取出产品,使用了 6 轴 IRB 6600 机器人。
运营影响
数量效益
相关案例.
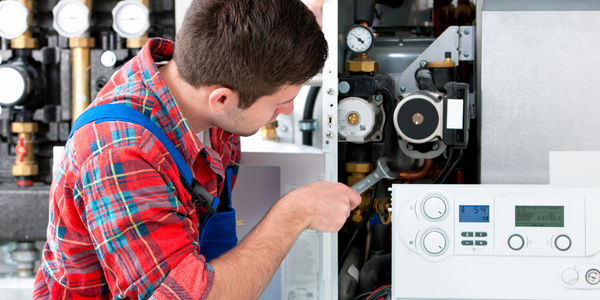
Case Study
Boiler Control System for Plastic Manufacturing Applications
Factory automation applications must be equipped to handle and monitor the myriads of information from attached devices. For plastic manufacturing applications, the boiler control system plays a critical role by gathering and regulating information to ensure production is accurate and smooth. In this particular case, the customer combines eight subsystems that include power meters, water meters, alarm output, displays, and I/O status to be controlled by several intelligent controllers with Modbus RTU interface. The Modbus TCP protocol is used for this application due to the distance. System Requirements: • Modbus serial to Modbus TCP translation • Multiple slaves/masters support • Automatic Modbus TCP response time detection
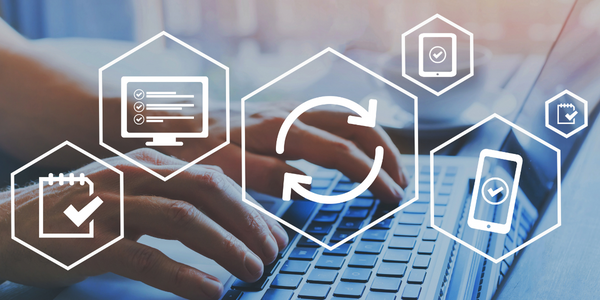
Case Study
Ascend Performance Materials Case Study
Ascend operations must access multiple software systems to manage day-to-day operations in an effective and secure manner. These systems generate large sets of data which contain critical information pertaining to management systems, planning and cost information in business systems and energy consumption. As a result, Ascend management was challenged with creating relevant reports reflecting performance measures in overall context of their operational process. The company’s previous process entailed collecting and analyzing data manually which was not effective, since the information collected was generated after the fact, and was too complex for collaborative use across the organization.
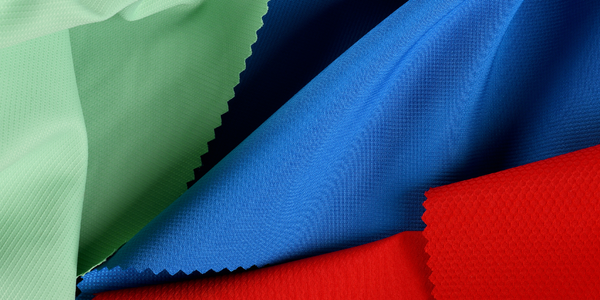
Case Study
Remake Enterprise-to-production System
The client was running a legacy material flow tracking system and wanted to replace the system with a more effective one as the system was increasingly expensive to maintain and support and also was not extendable. The client's IT landscape was filled with modern applications and it was difficult to interface the material flow tracking system with modern applications.
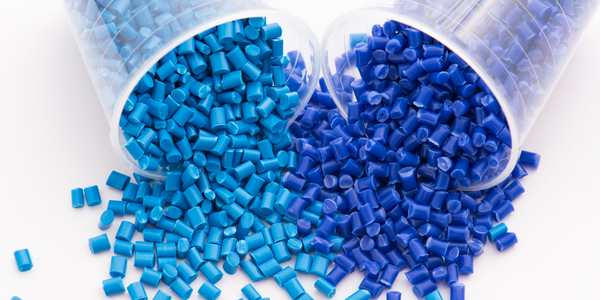
Case Study
CK Technologies: Leveraging QAD Explore for Continuous Improvement
CK Technologies, a leading thermoplastics solutions provider in the North American commercial heavy truck market, faced a significant challenge in maintaining continuous improvement in their business practices. This was particularly difficult due to the nature of their low volume, high variability business. The company produces a wide variety of parts for multiple customers, supplies parts for current truck models, and also the service parts for past design versions. They are also one of the first companies in the industry to supply parts in body color for each customer, approximately 1,400 colors a year, which have to be perfectly sequenced for shipment. This complexity in their operations made it challenging to stay informed and inspired to accomplish continuous improvement.