下载PDF
Print Goes Digital and Predictive with the Internet of Things
技术
- 分析与建模 - 实时分析
- 平台即服务 (PaaS) - 连接平台
适用行业
- 电子产品
适用功能
- 离散制造
- 维护
用例
- 预测性维护
- 实时定位系统 (RTLS)
- 供应链可见性(SCV)
服务
- 系统集成
- 软件设计与工程服务
挑战
The company, a global leader in imaging technology solutions and managed print services, was facing increased competition and service level agreement (SLA) compliance issues. There was a push for IoT-enablement and new device location tracking requirements. The company was also dealing with inefficient field maintenance and rising costs, and lacked real-time visibility into partner supply chains. In the case of on-site printer fleet repair and maintenance, the old way simply couldn’t cut it. Reactive failure reporting, multiple technician visits and manual parts ordering dragged down profits and aggravated customers. With tens of thousands of printers moved per week, and third-party supply chains to contend with, manual repair and maintenance led to SLA violations, billing headaches and logistical nightmares.
关于客户
The customer is a manufacturer recognized as a global leader in imaging technology solutions and managed print services. The company has thousands of employees who are responsible for billions in revenue from sales in almost every country in the world. The company has led the imaging solutions industry since its founding, but by the mid-2010s, it was facing increasing competition, mounting inefficiencies from manual processes, and the commoditization of previously lucrative contracts. The company's industry-leading innovation and expertise have earned it a world-class customer loyalty rate that most companies only dream of.
解决方案
The company partnered with Software AG to develop the location-based Operational Intelligence Platform (OIP) that could track live device movements, provide visibility into service and component supply-chain processes, and scale for continuous and batch data from millions of devices and their reference data input. The flexibility of webMethods BPMS enabled real-time, automated interaction with service partners. And the combined streaming and predictive analytics of Apama monitored sensor data to determine equipment condition, analyze and act on high-volume IoT streams, and ultimately leverage advanced predictive modeling to anticipate failures. The team’s OIP for streaming analytics was put in place, creating actionable intelligence on more than 1 million device status updates and real-time sensor data alerts per day. Working together, Software AG and partner Wipro implemented the solution in less than three months.
运营影响
数量效益
相关案例.
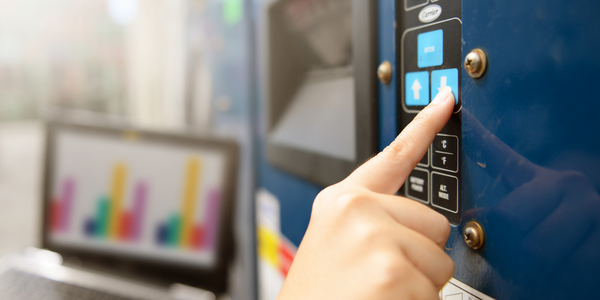
Case Study
Remote Temperature Monitoring of Perishable Goods Saves Money
RMONI was facing temperature monitoring challenges in a cold chain business. A cold chain must be established and maintained to ensure goods have been properly refrigerated during every step of the process, making temperature monitoring a critical business function. Manual registration practice can be very costly, labor intensive and prone to mistakes.
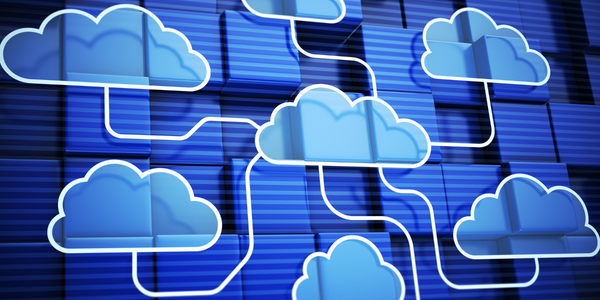
Case Study
Cloud Solution for Energy Management Platform-Schneider Electric
Schneider Electric required a cloud solution for its energy management platform to manage high computational operations, which were essential for catering to client requirements. As the business involves storage and analysis of huge amounts of data, the company also needed a convenient and scalable storage solution to facilitate operations efficiently.
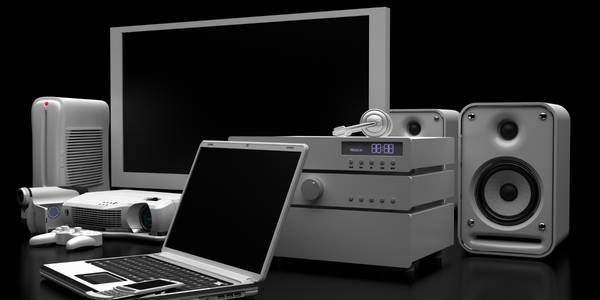
Case Study
Leveraging the IoT to Gain a Competitive Edge in International Competition
Many large manufacturers in and outside Japan are competing for larger market share in the same space, expecting a growing demand for projectors in the areas of entertainment, which requires glamor and strong visual performance as well as digital signage that can attract people’s attention. “It is becoming more and more difficult to differentiate ourselves with stand-alone hardware products,” says Kazuyuki Kitagawa, Director of Service & Support at Panasonic AVC Networks. “In order for Panasonic to grow market share and overall business, it is essential for us to develop solutions that deliver significant added value.” Panasonic believes projection failure and quality deterioration should never happen. This is what and has driven them to make their projectors IoT-enabled. More specifically, Panasonic has developed a system that collects data from projectors, visualizes detailed operational statuses, and predicts issues and address them before failure occurs. Their projectors are embedded with a variety of sensors that measure power supply, voltage, video input/ output signals, intake/exhaust air temperatures, cooling fan operations, and light bulb operating time. These sensors have been used to make the projector more intelligent, automatically suspending operation when the temperature rises excessively, and automatically switching light bulbs. Although this was a great first step, Panasonic projectors were still not equipped with any capability to send the data over a network.