下载PDF
Real-time, Automated Data Empowering the Precision Machining Industry
技术
- 功能应用 - 制造执行系统 (MES)
- 分析与建模 - 实时分析
- 应用基础设施与中间件 - 数据交换与集成
适用功能
- 质量保证
- 流程制造
用例
- 预测性维护
- 机器状态监测
- 过程控制与优化
服务
- 软件设计与工程服务
- 系统集成
挑战
A senior quality engineer for a leading machining company faced alarming scrap levels, with only hindsight data available to prevent it. Precision was crucial for the intricate manufactured components. The company had five work zones with a first-pass yield of only 40 percent, generating staggering annual scrap costs. Pertinent inspection data was manually collected and recorded, making it costly and difficult to manage. Weeks often passed before usable data became available, allowing defective products to pass through manufacturing processes with hidden issues. Identifying underlying issues required extensive efforts from Six Sigma Black Belts, often long after the fact.
关于客户
Hertzler Systems has been providing seamless, accurate data acquisition solutions for over 30 years. They serve a large and diverse customer base in service, transactional, and manufacturing environments, including companies like Consolidated Biscuit Company, Darden Restaurants, Pactiv Inc., McCormick & Company, and Hormel Foods. Customers invest in Hertzler Systems' software and services to easily acquire data in any process, analyze it in real-time, and instantly notify process owners of process variations. These capabilities help clients reduce costs, cycle time, errors, and defects, while increasing profitability and customer satisfaction.
解决方案
The quality engineer envisioned an automated data collection system that would seamlessly integrate with the company’s ERP system, gages, and coordinate measuring machines (CMM). Hertzler Systems provided the GainSeeker automated real-time data collection system, which collects data directly from all plant devices, including the scheduling system. This system was designed to be easy for machine operators to use, enabling them to take initial actions toward problem prevention. GainSeeker empowered operators to drill down into the data in real-time to see how a process was performing, significantly improving the company's operational efficiency.
运营影响
数量效益
相关案例.
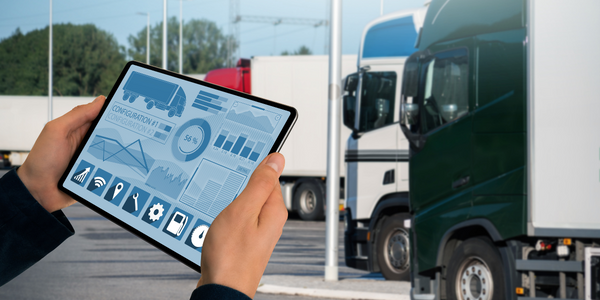
Case Study
IoT enabled Fleet Management with MindSphere
In view of growing competition, Gämmerler had a strong need to remain competitive via process optimization, reliability and gentle handling of printed products, even at highest press speeds. In addition, a digitalization initiative also included developing a key differentiation via data-driven services offers.
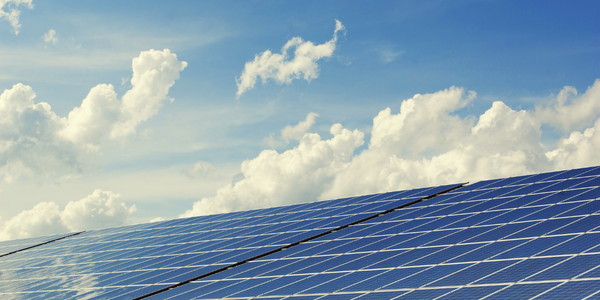
Case Study
Remote Monitoring & Predictive Maintenance App for a Solar Energy System
The maintenance & tracking of various modules was an overhead for the customer due to the huge labor costs involved. Being an advanced solar solutions provider, they wanted to ensure early detection of issues and provide the best-in-class customer experience. Hence they wanted to automate the whole process.
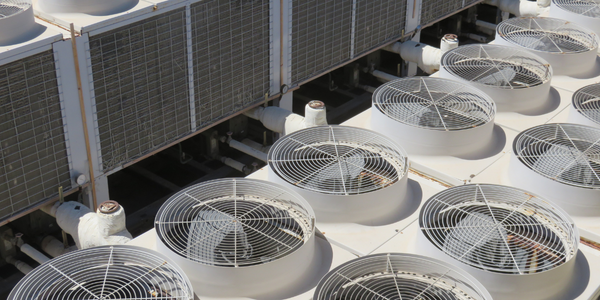
Case Study
Predictive Maintenance for Industrial Chillers
For global leaders in the industrial chiller manufacturing, reliability of the entire production process is of the utmost importance. Chillers are refrigeration systems that produce ice water to provide cooling for a process or industrial application. One of those leaders sought a way to respond to asset performance issues, even before they occur. The intelligence to guarantee maximum reliability of cooling devices is embedded (pre-alarming). A pre-alarming phase means that the cooling device still works, but symptoms may appear, telling manufacturers that a failure is likely to occur in the near future. Chillers who are not internet connected at that moment, provide little insight in this pre-alarming phase.
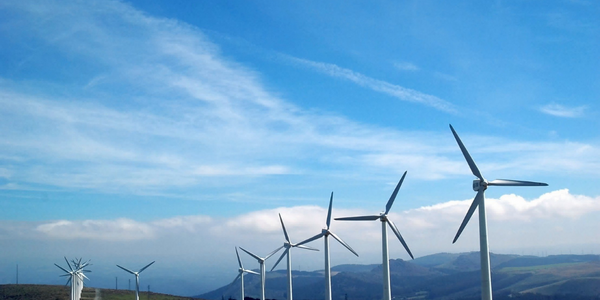
Case Study
Siemens Wind Power
Wind provides clean, renewable energy. The core concept is simple: wind turbines spin blades to generate power. However, today's systems are anything but simple. Modern wind turbines have blades that sweep a 120 meter circle, cost more than 1 million dollars and generate multiple megawatts of power. Each turbine may include up to 1,000 sensors and actuators – integrating strain gages, bearing monitors and power conditioning technology. The turbine can control blade speed and power generation by altering the blade pitch and power extraction. Controlling the turbine is a sophisticated job requiring many cooperating processors closing high-speed loops and implementing intelligent monitoring and optimization algorithms. But the real challenge is integrating these turbines so that they work together. A wind farm may include hundreds of turbines. They are often installed in difficult-to-access locations at sea. The farm must implement a fundamentally and truly distributed control system. Like all power systems, the goal of the farm is to match generation to load. A farm with hundreds of turbines must optimize that load by balancing the loading and generation across a wide geography. Wind, of course, is dynamic. Almost every picture of a wind farm shows a calm sea and a setting sun. But things get challenging when a storm goes through the wind farm. In a storm, the control system must decide how to take energy out of gusts to generate constant power. It must intelligently balance load across many turbines. And a critical consideration is the loading and potential damage to a half-billion-dollar installed asset. This is no environment for a slow or undependable control system. Reliability and performance are crucial.
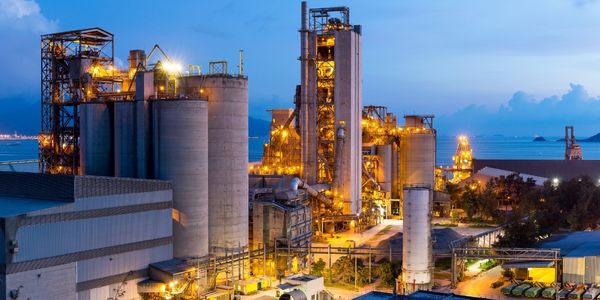
Case Study
System 800xA at Indian Cement Plants
Chettinad Cement recognized that further efficiencies could be achieved in its cement manufacturing process. It looked to investing in comprehensive operational and control technologies to manage and derive productivity and energy efficiency gains from the assets on Line 2, their second plant in India.
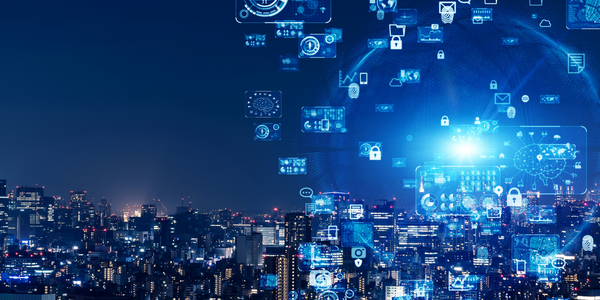
Case Study
Integration of PLC with IoT for Bosch Rexroth
The application arises from the need to monitor and anticipate the problems of one or more machines managed by a PLC. These problems, often resulting from the accumulation over time of small discrepancies, require, when they occur, ex post technical operations maintenance.