下载PDF
Revolutionizing Automotive Design: A Case Study on Technische Universität Dresden's Formula Student Team
技术
- 功能应用 - 制造执行系统 (MES)
适用行业
- 设备与机械
- 生命科学
适用功能
- 产品研发
用例
- 添加剂制造
- 制造过程模拟
挑战
德累斯顿工业大学的学生方程式团队面临着设计和制造新型学生方程式转向柱支架的挑战。现有的转向柱安装座很复杂,由不同角度的四个不同区域组成,因此很难使用 5 轴铣床进行生产。生产该部件的解决方案由四个不同的铣削铝部件组成,这些部件全部用螺栓固定在一起。该团队正在寻找一种方法来简化设计和生产过程、减轻零件重量并提高其性能特征。
关于客户
本案例中的客户是德累斯顿工业大学的学生方程式赛车团队,该团队参与学生方程式赛车零件的设计和制造。该团队由学生和研究人员组成,其中包括该大学的研究员 Michael Süß,他目前正在攻读博士学位,重点研究增材制造/电子束熔化的设计指南。 Michael 还与弗劳恩霍夫制造技术和先进材料研究所 IFAM 密切合作,该研究所是欧洲粘合剂技术、材料科学和制造技术领域领先的研究机构之一。该大学的在读学生卢卡斯·霍夫曼 (Lucas Hofman) 也参与了这个项目。
解决方案
该团队决定使用 SolidThinking Inspire 进行设计流程,并使用电子束熔化来生产新零件。 SolidThinking Inspire 因其易用性、集成分析工具和 PolyNURBS 功能而被选中,这些功能使团队能够快速获取优化结果并重建零件以进行制造。选择电子束熔化工艺是因为与其他制造方法相比,其设计自由且设计限制更少。该团队与弗劳恩霍夫制造技术和先进材料研究所 IFAM 合作,使用 Arcam A2X 电子束熔化机完成了制造。该零件采用钛合金制成,有助于显着减轻重量。
运营影响
数量效益
相关案例.
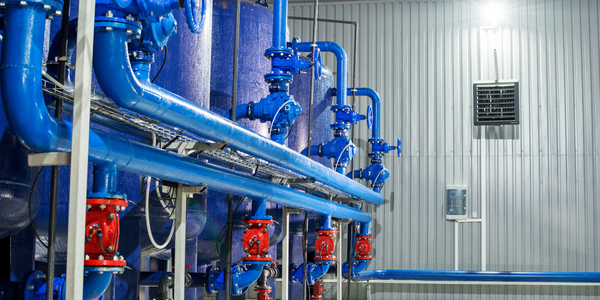
Case Study
Smart Water Filtration Systems
Before working with Ayla Networks, Ozner was already using cloud connectivity to identify and solve water-filtration system malfunctions as well as to monitor filter cartridges for replacements.But, in June 2015, Ozner executives talked with Ayla about how the company might further improve its water systems with IoT technology. They liked what they heard from Ayla, but the executives needed to be sure that Ayla’s Agile IoT Platform provided the security and reliability Ozner required.
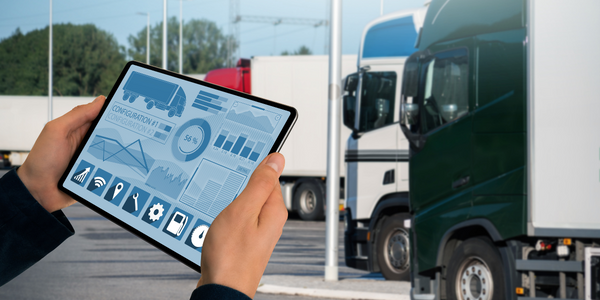
Case Study
IoT enabled Fleet Management with MindSphere
In view of growing competition, Gämmerler had a strong need to remain competitive via process optimization, reliability and gentle handling of printed products, even at highest press speeds. In addition, a digitalization initiative also included developing a key differentiation via data-driven services offers.
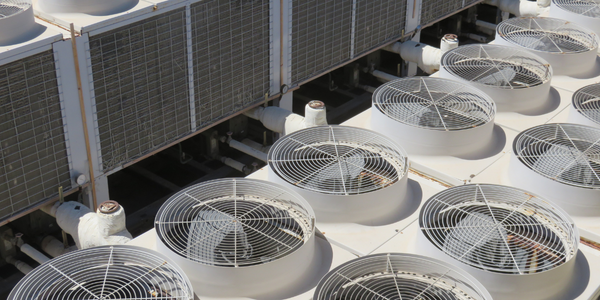
Case Study
Predictive Maintenance for Industrial Chillers
For global leaders in the industrial chiller manufacturing, reliability of the entire production process is of the utmost importance. Chillers are refrigeration systems that produce ice water to provide cooling for a process or industrial application. One of those leaders sought a way to respond to asset performance issues, even before they occur. The intelligence to guarantee maximum reliability of cooling devices is embedded (pre-alarming). A pre-alarming phase means that the cooling device still works, but symptoms may appear, telling manufacturers that a failure is likely to occur in the near future. Chillers who are not internet connected at that moment, provide little insight in this pre-alarming phase.
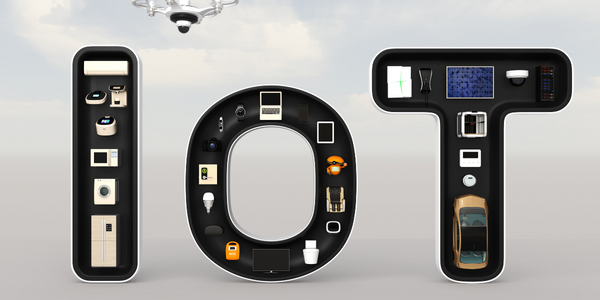
Case Study
Premium Appliance Producer Innovates with Internet of Everything
Sub-Zero faced the largest product launch in the company’s history:It wanted to launch 60 new products as scheduled while simultaneously opening a new “greenfield” production facility, yet still adhering to stringent quality requirements and manage issues from new supply-chain partners. A the same time, it wanted to increase staff productivity time and collaboration while reducing travel and costs.
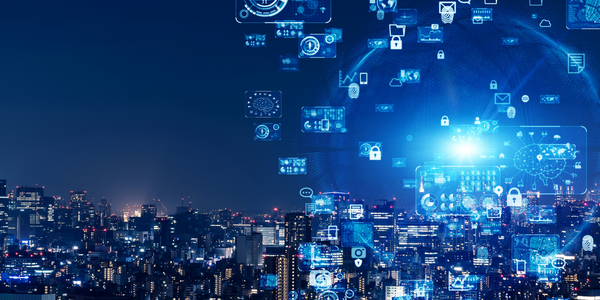
Case Study
Integration of PLC with IoT for Bosch Rexroth
The application arises from the need to monitor and anticipate the problems of one or more machines managed by a PLC. These problems, often resulting from the accumulation over time of small discrepancies, require, when they occur, ex post technical operations maintenance.
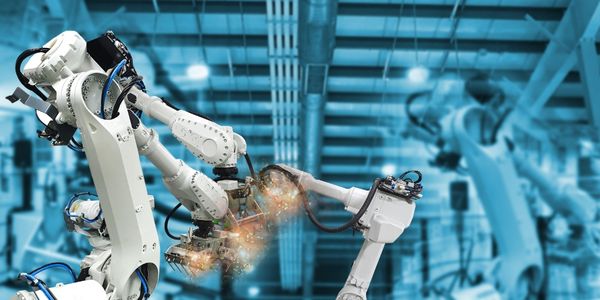
Case Study
Robot Saves Money and Time for US Custom Molding Company
Injection Technology (Itech) is a custom molder for a variety of clients that require precision plastic parts for such products as electric meter covers, dental appliance cases and spools. With 95 employees operating 23 molding machines in a 30,000 square foot plant, Itech wanted to reduce man hours and increase efficiency.