下载PDF
Revving up Electrohydraulic Power Steering with Virtual Prototyping
技术
- 分析与建模 - 预测分析
- 分析与建模 - 实时分析
- 应用基础设施与中间件 - 数据可视化
适用行业
- 汽车
- 设备与机械
适用功能
- 产品研发
- 质量保证
用例
- 预测性维护
- 机器状态监测
- 虚拟原型与产品测试
服务
- 软件设计与工程服务
- 系统集成
- 测试与认证
挑战
Designing an electrohydraulic power steering (EHPS) system involves managing numerous interrelated components, where minor adjustments can significantly impact the system's function, efficiency, and reliability. The complexity of the system, which includes an electronic control unit (ECU), torque sensor, valve, and pipe system, requires a detailed understanding of how each part interacts. Traditional validation and physical testing methods are expensive and time-consuming, often taking up to six months. This slow process is not conducive to the fast-paced design cycles required in the automotive industry. Therefore, there is a need for a more efficient method to refine and optimize EHPS designs before moving to physical testing.
关于客户
FZB Technology, based in Plymouth, MI, specializes in research and development for the automotive market. The company focuses on developing advanced automotive components such as motors, sensors, keyless RFID ignition systems, and electrohydraulic power steering (EHPS) systems. FZB Technology employs a team of skilled engineers who frequently use advanced simulation tools to model and refine their designs. The company collaborates with major automotive manufacturers, including Chrysler, to ensure their products meet industry standards and requirements. FZB Technology is committed to innovation and efficiency, leveraging cutting-edge technology to stay ahead in the competitive automotive sector.
解决方案
FZB Technology employs multiphysics simulation using COMSOL Multiphysics® software to model and refine their EHPS designs. This approach allows them to understand the behavior of the system's components and move closer to a final design before physical testing. The team models major components such as the ECU, motor, fluid reservoir, and helical gear pump, performing both individual and multiphysics analyses. These simulations help solve issues related to thermal performance, dynamic motion control, fluid delivery, and noise, vibration, and harshness (NVH). By using simulation, FZB can expedite the design refinement process, reducing the time and cost associated with physical testing. The team also uses specialized software like PumpLinx® for fluid efficiency analysis and SOLIDWORKS® for geometry updates. This integrated approach enables them to make significant design improvements and meet automotive requirements more efficiently.
运营影响
数量效益
相关案例.
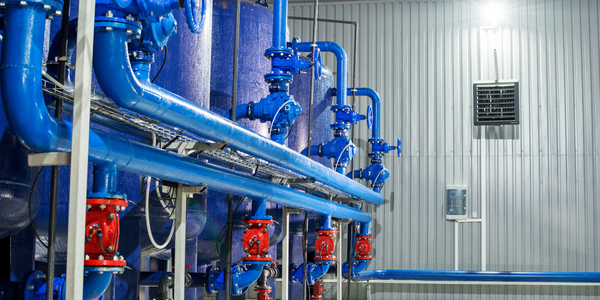
Case Study
Smart Water Filtration Systems
Before working with Ayla Networks, Ozner was already using cloud connectivity to identify and solve water-filtration system malfunctions as well as to monitor filter cartridges for replacements.But, in June 2015, Ozner executives talked with Ayla about how the company might further improve its water systems with IoT technology. They liked what they heard from Ayla, but the executives needed to be sure that Ayla’s Agile IoT Platform provided the security and reliability Ozner required.
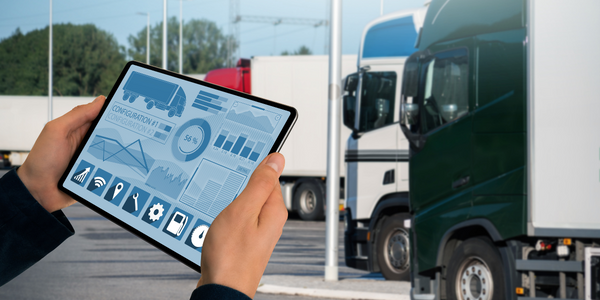
Case Study
IoT enabled Fleet Management with MindSphere
In view of growing competition, Gämmerler had a strong need to remain competitive via process optimization, reliability and gentle handling of printed products, even at highest press speeds. In addition, a digitalization initiative also included developing a key differentiation via data-driven services offers.
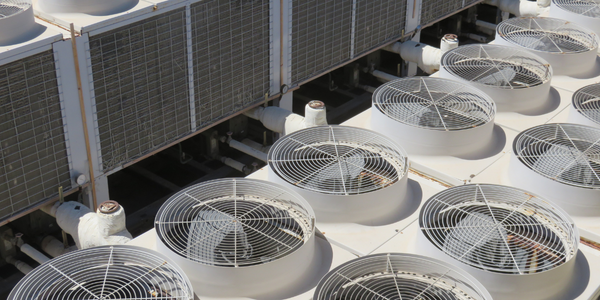
Case Study
Predictive Maintenance for Industrial Chillers
For global leaders in the industrial chiller manufacturing, reliability of the entire production process is of the utmost importance. Chillers are refrigeration systems that produce ice water to provide cooling for a process or industrial application. One of those leaders sought a way to respond to asset performance issues, even before they occur. The intelligence to guarantee maximum reliability of cooling devices is embedded (pre-alarming). A pre-alarming phase means that the cooling device still works, but symptoms may appear, telling manufacturers that a failure is likely to occur in the near future. Chillers who are not internet connected at that moment, provide little insight in this pre-alarming phase.
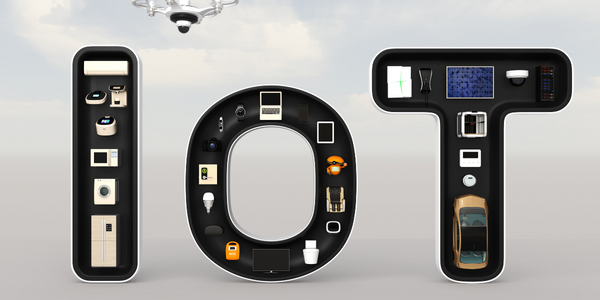
Case Study
Premium Appliance Producer Innovates with Internet of Everything
Sub-Zero faced the largest product launch in the company’s history:It wanted to launch 60 new products as scheduled while simultaneously opening a new “greenfield” production facility, yet still adhering to stringent quality requirements and manage issues from new supply-chain partners. A the same time, it wanted to increase staff productivity time and collaboration while reducing travel and costs.
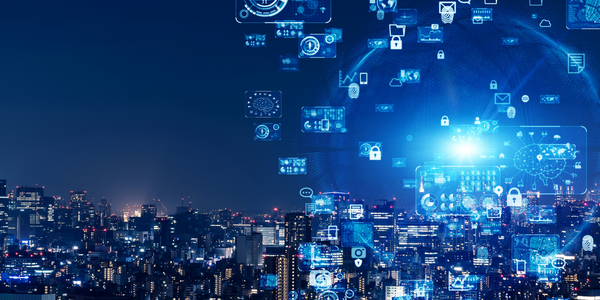
Case Study
Integration of PLC with IoT for Bosch Rexroth
The application arises from the need to monitor and anticipate the problems of one or more machines managed by a PLC. These problems, often resulting from the accumulation over time of small discrepancies, require, when they occur, ex post technical operations maintenance.
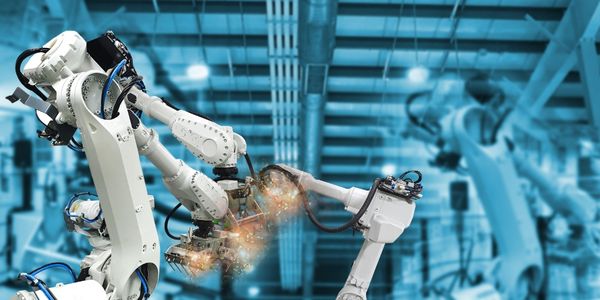
Case Study
Robot Saves Money and Time for US Custom Molding Company
Injection Technology (Itech) is a custom molder for a variety of clients that require precision plastic parts for such products as electric meter covers, dental appliance cases and spools. With 95 employees operating 23 molding machines in a 30,000 square foot plant, Itech wanted to reduce man hours and increase efficiency.