下载PDF
Semiconductor Manufacturer Powers a Fast-Growth Business Through Digital Transformation
技术
- 分析与建模 - 预测分析
- 功能应用 - 企业资源规划系统 (ERP)
- 功能应用 - 制造执行系统 (MES)
适用行业
- 汽车
- 电子产品
- 半导体
适用功能
- 质量保证
用例
- 库存管理
- 预测性维护
- 供应链可见性(SCV)
- 资产跟踪
服务
- 云规划/设计/实施服务
- 软件设计与工程服务
- 系统集成
挑战
The semiconductor manufacturer faced significant challenges due to rapid growth through acquisitions, leading to increased manufacturing complexity and siloed data. The disparate manufacturing execution systems (MESs) from acquired companies created data silos, making it difficult to track products through the manufacturing and testing cycle. The company also experienced a dramatic increase in transaction volumes, nearly doubling in the preceding five years, which strained employee and system workloads. Additionally, the large number of lots moving through the network required close tracking for quality purposes and to minimize excess and obsolete inventory. The existing MES solution did not provide cross-factory visibility or traceability, necessitating a new solution to achieve end-to-end network visibility, enable multi-tier collaboration, and manage quality throughout every manufacturing phase.
关于客户
The customer is a leading manufacturer of complex electronic components, with a diverse portfolio that includes tens of thousands of products ranging from high-volume, general-purpose semiconductors to complex, application-specific components. The company serves virtually all industries, including industrial, medical, automotive, communications, computing, consumer, aerospace, and defense. It sells directly to manufacturers and through major distributors, with a significant portion of sales coming from the Asia-Pacific region. The company operates over 200 large-scale production sites globally and generates annual revenues exceeding $5 billion.
解决方案
To address its challenges, the semiconductor manufacturer selected e2open's Manufacturing Collaboration application. This solution provided the necessary lot tracking and genealogy, component track and traceability, and logistics visibility as products moved through the company's complex manufacturing and test processes. E2open's ability to horizontally integrate manufacturing sites and carry lot attributes to downstream sites was a key differentiator. The system connected various data sources to automatically assemble production, inventory, and quality information from across the company's entire supply network. This enabled real-time responses to quality issues and better service for the company's growing product lines and customer base. The semiconductor company implemented the solution using a phased rollout approach, starting with the retirement of the legacy mainframe platform and quickly onboarding internal manufacturing sites to e2open's network. The second phase involved connecting all internal and external sites to e2open's network and converting to attribute-based tracking and tracing.
运营影响
数量效益
相关案例.
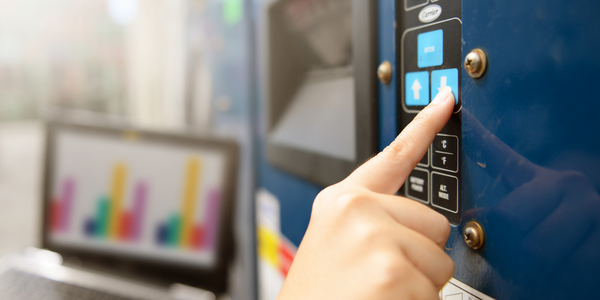
Case Study
Remote Temperature Monitoring of Perishable Goods Saves Money
RMONI was facing temperature monitoring challenges in a cold chain business. A cold chain must be established and maintained to ensure goods have been properly refrigerated during every step of the process, making temperature monitoring a critical business function. Manual registration practice can be very costly, labor intensive and prone to mistakes.
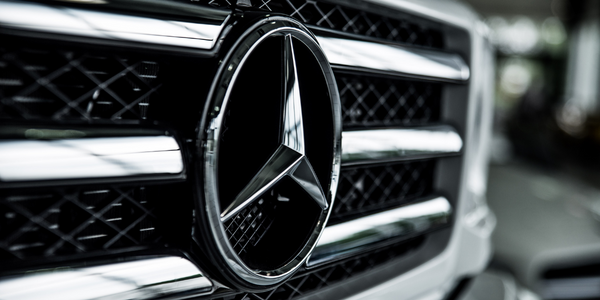
Case Study
Integral Plant Maintenance
Mercedes-Benz and his partner GAZ chose Siemens to be its maintenance partner at a new engine plant in Yaroslavl, Russia. The new plant offers a capacity to manufacture diesel engines for the Russian market, for locally produced Sprinter Classic. In addition to engines for the local market, the Yaroslavl plant will also produce spare parts. Mercedes-Benz Russia and his partner needed a service partner in order to ensure the operation of these lines in a maintenance partnership arrangement. The challenges included coordinating the entire maintenance management operation, in particular inspections, corrective and predictive maintenance activities, and the optimizing spare parts management. Siemens developed a customized maintenance solution that includes all electronic and mechanical maintenance activities (Integral Plant Maintenance).