下载PDF
Success Stories: Chempax a Time Saver for C&L Aqua Professionals, Inc.
技术
- 功能应用 - 库存管理系统
适用功能
- 物流运输
- 销售与市场营销
用例
- 库存管理
- 供应链可见性(SCV)
服务
- 软件设计与工程服务
- 系统集成
挑战
C & L Aqua Professionals, Inc. was using Peachtree Accounting for their software solution for 17 years. However, it was not industry-specific, forcing the company to re-key information and duplicate data into other software packages. This redundancy was a major challenge as it was inefficient and time-consuming. The company was in need of a software solution that was industry-specific and could eliminate these redundancies, allowing their staff to work more efficiently. They were looking for a software vendor that could offer a complete solution.
关于客户
C & L Aqua Professionals, Inc. is a locally owned and operated wholesale chemical distributor and manufacturer based in Sulphur, Louisiana. The company sells, manufactures, and delivers water treatment chemicals to over 500 rural customers within the State of Louisiana. C & L Aqua Pro was established in December 1995 when two existing chemical companies merged. They operate from one central location in Sulphur, Louisiana.
解决方案
C & L Aqua Professionals, Inc. chose Datacor and their Chempax software as their new software solution. The decision was made after demoing four software vendors and finding that Datacor was the only one that offered a complete solution. Chempax was able to eliminate the redundancies that were present with their previous system, Peachtree Accounting. The system automatically calculates and tracks information, streamlining their business and saving them time. The eChempax feature provided invaluable information to their sales representatives in the field, making customer information such as previous deliveries and GPS coordinates readily available.
运营影响
数量效益
相关案例.
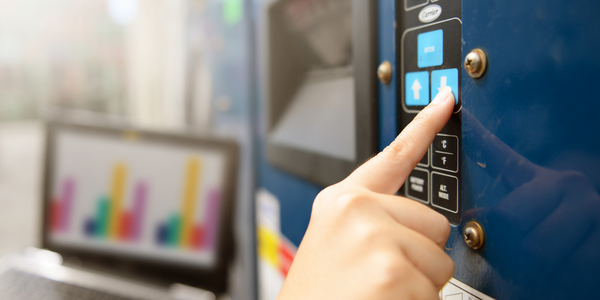
Case Study
Remote Temperature Monitoring of Perishable Goods Saves Money
RMONI was facing temperature monitoring challenges in a cold chain business. A cold chain must be established and maintained to ensure goods have been properly refrigerated during every step of the process, making temperature monitoring a critical business function. Manual registration practice can be very costly, labor intensive and prone to mistakes.
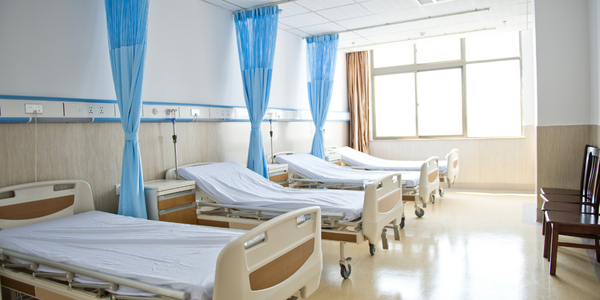
Case Study
Hospital Inventory Management
The hospital supply chain team is responsible for ensuring that the right medical supplies are readily available to clinicians when and where needed, and to do so in the most efficient manner possible. However, many of the systems and processes in use at the cancer center for supply chain management were not best suited to support these goals. Barcoding technology, a commonly used method for inventory management of medical supplies, is labor intensive, time consuming, does not provide real-time visibility into inventory levels and can be prone to error. Consequently, the lack of accurate and real-time visibility into inventory levels across multiple supply rooms in multiple hospital facilities creates additional inefficiency in the system causing over-ordering, hoarding, and wasted supplies. Other sources of waste and cost were also identified as candidates for improvement. Existing systems and processes did not provide adequate security for high-cost inventory within the hospital, which was another driver of cost. A lack of visibility into expiration dates for supplies resulted in supplies being wasted due to past expiry dates. Storage of supplies was also a key consideration given the location of the cancer center’s facilities in a dense urban setting, where space is always at a premium. In order to address the challenges outlined above, the hospital sought a solution that would provide real-time inventory information with high levels of accuracy, reduce the level of manual effort required and enable data driven decision making to ensure that the right supplies were readily available to clinicians in the right location at the right time.