下载PDF
Tyre Manufacturer Overcomes Suez Canal Blockade with IoT Solution
技术
- 分析与建模 - 预测分析
- 分析与建模 - 实时分析
适用行业
- 汽车
- 零售
适用功能
- 设施管理
用例
- 实时定位系统 (RTLS)
- 供应链可见性(SCV)
挑战
一家总部位于印度孟买、生产设施遍布全球的领先轮胎制造公司,由于 2021 年 3 月的苏伊士运河封锁而面临重大挑战。这次封锁是由一艘名为长荣 (Evergreen) 的摩天大楼大小的集装箱船造成的,导致约 200 艘船舶停运搁浅在运河两端,严重影响了全球贸易。封锁造成的财务影响是巨大的,封锁每天造成近 70 亿英镑的货物损失,或每小时约 2.9 亿英镑的损失。该轮胎制造商的西向和东向运输被暂停,影响了价值 1,850 万美元的货物。这导致成品交付延迟,影响了欧洲和美国的八名客户。此外,印度生产设施的原材料供应严重中断,导致生产周期严重中断。
关于客户
该客户是一家总部位于孟买的全球领先的轮胎制造商,其生产设施遍布以色列、中国、欧洲、印度、南非、美国和墨西哥。该公司专门生产汽车行业的专用轮胎和其他行业的多用途轮胎。该品牌受到 2021 年 3 月苏伊士运河封锁的严重影响,西行和东行货运均停止,价值 1,850 万美元的货物受到影响。封锁还导致向欧洲和美国的八个客户交付成品的延迟,并扰乱了其印度生产设施的原材料供应。
解决方案
为了应对这场危机,该公司寻求一种工具,能够提供对货物的位置、滞留时间的可视性,并提供丰富的分析来预测未来的情况。 GoComet 的 GoTrack 自动货运跟踪系统是我们选择的解决方案。 GoTrack 提供实时可视性,为途经南非的船只和等待运河重新开放的船只提供准确的见解。该系统还提供预测性和描述性数据,根据地面发展和高级数据分析来预测延误并更新预计到达时间。此外,GoTrack 还会自动生成有关运载公司货物的船舶状态的每日报告。该解决方案使该公司能够做出数据驱动的决策来应对危机、重新分配资源、更好地管理生产周期,并通过共享实时跟踪更新来增强客户体验。
运营影响
数量效益
相关案例.
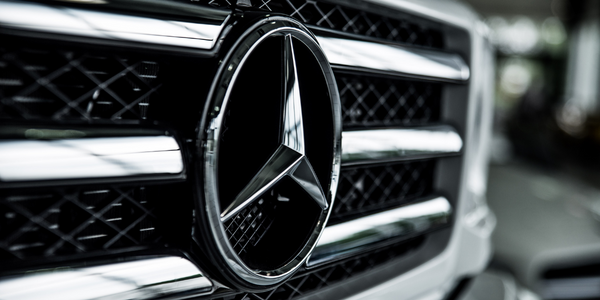
Case Study
Integral Plant Maintenance
Mercedes-Benz and his partner GAZ chose Siemens to be its maintenance partner at a new engine plant in Yaroslavl, Russia. The new plant offers a capacity to manufacture diesel engines for the Russian market, for locally produced Sprinter Classic. In addition to engines for the local market, the Yaroslavl plant will also produce spare parts. Mercedes-Benz Russia and his partner needed a service partner in order to ensure the operation of these lines in a maintenance partnership arrangement. The challenges included coordinating the entire maintenance management operation, in particular inspections, corrective and predictive maintenance activities, and the optimizing spare parts management. Siemens developed a customized maintenance solution that includes all electronic and mechanical maintenance activities (Integral Plant Maintenance).
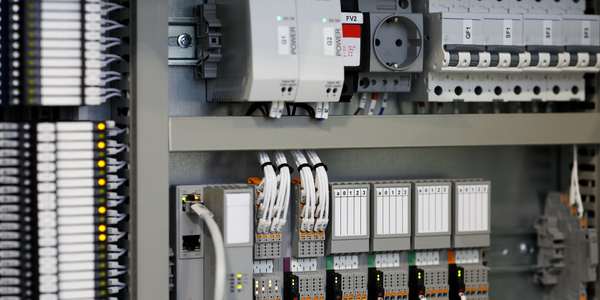
Case Study
Improving Production Line Efficiency with Ethernet Micro RTU Controller
Moxa was asked to provide a connectivity solution for one of the world's leading cosmetics companies. This multinational corporation, with retail presence in 130 countries, 23 global braches, and over 66,000 employees, sought to improve the efficiency of their production process by migrating from manual monitoring to an automatic productivity monitoring system. The production line was being monitored by ABB Real-TPI, a factory information system that offers data collection and analysis to improve plant efficiency. Due to software limitations, the customer needed an OPC server and a corresponding I/O solution to collect data from additional sensor devices for the Real-TPI system. The goal is to enable the factory information system to more thoroughly collect data from every corner of the production line. This will improve its ability to measure Overall Equipment Effectiveness (OEE) and translate into increased production efficiencies. System Requirements • Instant status updates while still consuming minimal bandwidth to relieve strain on limited factory networks • Interoperable with ABB Real-TPI • Small form factor appropriate for deployment where space is scarce • Remote software management and configuration to simplify operations