下载PDF
Villa Maria: Streamlining Operations with IoT
适用功能
- 质量保证
用例
- 人员跟踪与监控
- 质量预测分析
服务
- 测试与认证
挑战
Villa Maria 是新西兰最受赞誉的葡萄酒公司,在管理其跨多个地点的运营和不断变化的劳动力方面面临着重大挑战。该公司在五个主要酒庄、超过 14 个葡萄园、国内销售办事处和海外市场开展业务,并拥有不断壮大的出口经理团队。员工人数从 300 名长期员工到葡萄收获期的 500 名不等。挑战在于从质量控制转向质量保证,重点关注单个团队、专家和部门所有权。这需要一个易于使用的系统,不仅可以捕获信息,还可以捕获审计所需的任何更改。该公司需要确保无压力的审核、ISO 9001 以及健康与安全合规性、改进流程所有权和授权,以及简化流程和变更管理。
关于客户
Villa Maria 是新西兰获奖最多的葡萄酒公司。这家家族拥有的酒庄在五个主要酒庄、超过 14 个葡萄园、国内销售办事处以及拥有不断壮大的出口经理团队的海外市场开展业务。该公司的员工队伍不稳定,在葡萄收获期,固定员工人数从 300 人到 500 人不等。 Villa Maria 致力于在整个运营过程中保持高标准的质量和合规性,并寻求一种解决方案来帮助其更有效和高效地管理其流程。
解决方案
Villa Maria 采用两阶段方法实施了流程管理软件 Nintex Promapp。该软件为知识获取提供了中心位置,并为流程文档提供了更一致的方法。它的设计易于使用,使公司不仅能够捕获信息,还能够捕获审计所需的任何更改。两个实施阶段之间的协同作用意味着 Villa Maria 获得了比其他阶段更广泛的应用和采用。该解决方案还促进了不同地点之间的知识共享和最佳实践,简化了管理多个地点和劳动力波动的复杂性。 Nintex Promapp 的实施帮助 Villa Maria 专注于单个团队、专家和部门所有权,鼓励从质量控制转向质量保证。
运营影响
相关案例.
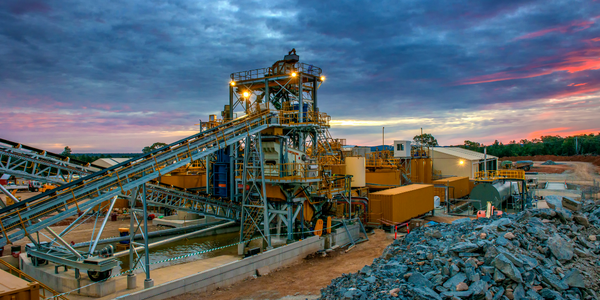
Case Study
Goldcorp: Internet of Things Enables the Mine of the Future
Goldcorp is committed to responsible mining practices and maintaining maximum safety for its workers. At the same time, the firm is constantly exploring ways to improve the efficiency of its operations, extend the life of its assets, and control costs. Goldcorp needed technology that can maximize production efficiency by tracking all mining operations, keep employees safe with remote operations and monitoring of hazardous work areas and control production costs through better asset and site management.
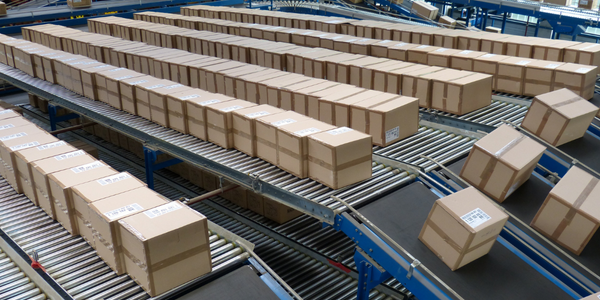
Case Study
IoT Data Analytics Case Study - Packaging Films Manufacturer
The company manufactures packaging films on made to order or configure to order basis. Every order has a different set of requirements from the product characteristics perspective and hence requires machine’s settings to be adjusted accordingly. If the film quality does not meet the required standards, the degraded quality impacts customer delivery causes customer dissatisfaction and results in lower margins. The biggest challenge was to identify the real root cause and devise a remedy for that.
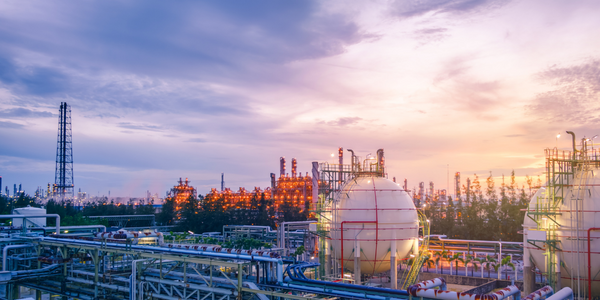
Case Study
Cisco Kinetic for Oil and Gas: Refineries and Plants
The plant manager and safety teams needed a solution that provided near real-time visibility of gas detection and personnel location, with easy to understand visualization and alerting dashboards. This would enable them to improve productivity through decreasing the time taken to start work, optimize evacuation route planning, and to meet critical staff safety and compliance goals.
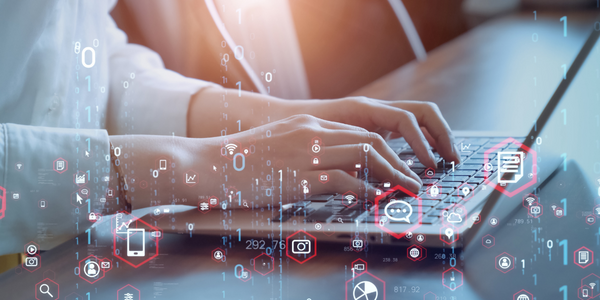
Case Study
Digital Transformation of Atlanta Grout & Tile: An IoT Case Study
Atlanta Grout & Tile, a Tile, Stone & Grout restoration company based in Woodstock, Georgia, was facing challenges with its traditional business model. Despite steady growth over the years, the company was falling behind the web revolution and missing out on the opportunity to tap into a new consumer base. They were using independent software from different vendors for each of their department information and workforce management. This resulted in a lot of manual work on excel and the need to export/import data between different systems. This not only increased overhead costs but also slowed down their response to clients. The company also had to prepare numerous reports manually and lacked access to customer trends for effective business decision-making.
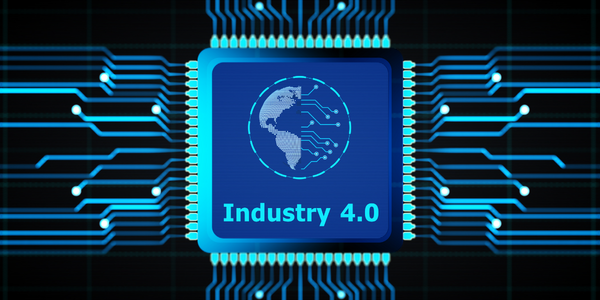
Case Study
Industry 4.0 at ALPLA: Enhancing Factory Efficiency with IoT
ALPLA, a global leader in packaging solutions, faced several challenges as the complexity of their production machinery increased. The need for highly trained specialists in each factory led to higher personnel costs, difficulties in recruiting experienced talent at each location, and costly personnel turnover. Furthermore, less experienced operators running the machines sub-optimally impacted resource consumption and overall equipment effectiveness (OEE). ALPLA also faced the challenge of monitoring visual inspection systems in every line of their plants, which was almost impossible to do manually. In 2016, ALPLA decided to use data from the 900 different types of embedded sensors in each factory to address these issues. However, their initial choice of SQL Server as the data store for the sensor data proved inadequate, as it was unable to cope with their data requirements.
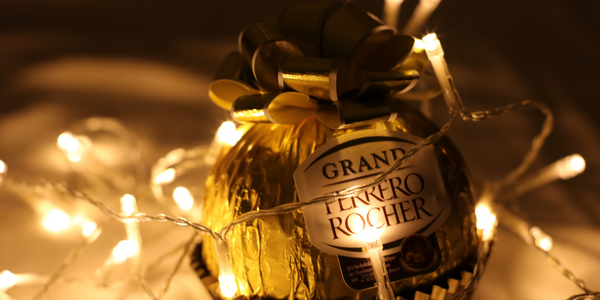
Case Study
Automated Headcounts Brings Security for Ferrero
Accounting for more than 1200 personnel, as well as visitors, at any given time is an arduous task, and even harder in the chaotic environment of an emergency. Every second counts when it comes to the safe evacuation of individuals in such events.Ferrero needed a way to confirm that all its employees could be safely accounted when an emergency evacuation was underway. The manual method had gotten out of date -- tracking each individual through manual counting was time-consuming and introduced potential for errors. Even if all personnel appeared at the dedicated mustering points, the employee roster for any given day could not be accurately obtained, especially when visitors were also in the building.Ferrero takes safety for these employees seriously and was recently seeing a solution that leveraged the latest that technology has to offer. The company’s internal audit system requires employee headcounts fast. After all, seconds can be critical when an emergency takes place and people need to be accounted for.