下载PDF
Virtual Material Design in 3D Printing Makes Headway with Multiscale Modeling
技术
- 分析与建模 - 数字孪生/模拟
- 分析与建模 - 预测分析
适用功能
- 产品研发
- 质量保证
用例
- 添加剂制造
- 数字孪生
- 质量预测分析
服务
- 软件设计与工程服务
- 系统集成
挑战
Anisotropic materials behave differently depending on the direction they are loaded, but current methods of material production offer limited control over anisotropy. This limitation makes it difficult to exploit the advantages of anisotropic materials for product design. Researchers at TNO aimed to develop a procedure for designing manufacturable anisotropic structures using stiffness and topology optimization techniques. They sought to create materials with specific properties, such as twice the stiffness in one planar direction compared to another, and to extend these capabilities to multimaterial structures. The challenge was to optimize the local distribution and orientation of materials at the microlevel and then scale these optimizations to larger devices while maintaining feasible computation times.
关于客户
The Netherlands Organization for Applied Scientific Research (TNO) is a prominent research institute that focuses on applied scientific research across various domains, including safety and security, energy, and manufacturing. TNO's work spans multiple subjects, and they are known for their innovative approaches to solving complex problems. The organization employs advanced techniques such as multiphysics simulation, multiscale modeling, and topology optimization to explore new frontiers in material design and additive manufacturing. TNO's research efforts are aimed at developing practical solutions that can be applied across different industries, making them a key player in the field of scientific research and technological innovation.
解决方案
Researchers at TNO used COMSOL Multiphysics® software to investigate and optimize the properties of anisotropic materials. They began by designing a single unit cell with specific stiffness characteristics and verified the simulation results with printed samples. The next step involved extending the simulation to multimaterial structures, optimizing the local distribution and orientation of materials to achieve desired properties. TNO implemented multiscale modeling to efficiently simulate both micromaterial and product scales simultaneously. This approach allowed them to design large, flexible organic LEDs (OLEDs) with improved light homogeneity by optimizing the metal grids in the transparent front-end electrodes. The team also applied their techniques to selective laser melting (SLM) 3D printing, developing unit cells that are stiff, printable, and contain holes for powder removal. They combined stiffness homogenization and topology optimization to create a polymer hammer handle with the correct stiffness and minimal material use, demonstrating the power and versatility of their approach.
运营影响
数量效益
相关案例.
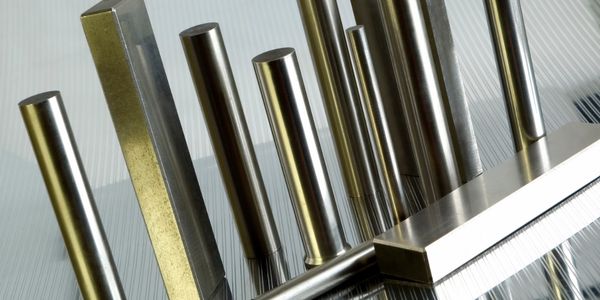
Case Study
RobotStudio Case Study: Benteler Automobiltechnik
Benteler has a small pipe business area for which they produce fuel lines and coolant lines made of aluminum for Porsche and other car manufacturers. One of the problems in production was that when Benteler added new products, production had too much downtime.
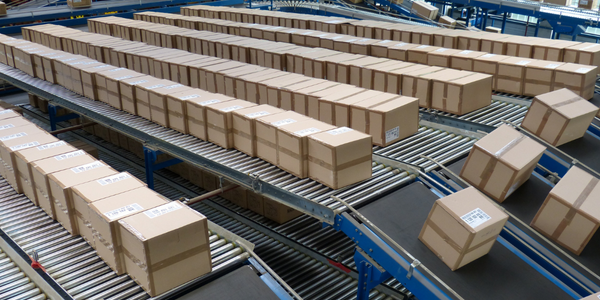
Case Study
IoT Data Analytics Case Study - Packaging Films Manufacturer
The company manufactures packaging films on made to order or configure to order basis. Every order has a different set of requirements from the product characteristics perspective and hence requires machine’s settings to be adjusted accordingly. If the film quality does not meet the required standards, the degraded quality impacts customer delivery causes customer dissatisfaction and results in lower margins. The biggest challenge was to identify the real root cause and devise a remedy for that.
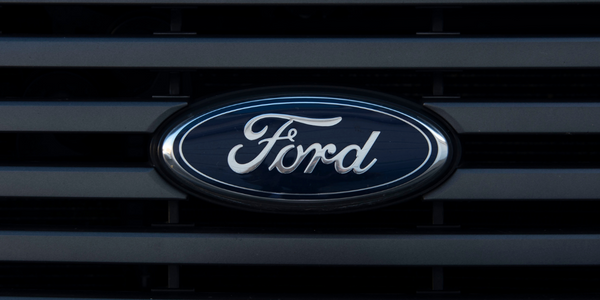
Case Study
Ford Motor Company on the Road to 3D Manufacturing
To date, key challenges have stood in the way of 3D printing becoming a manufacturing tool for the automaker. The first issue is a fundamental one — conventional 3D printing technologies make parts layer-by-layer, slowly crafting one layer at a time, creating parts that aren’t nearly as robust as those stamped or injection molded. While the slow speed of this process is a major drawback, the bigger problem is that the parts produced are not isotropic and not durable enough to be used in production vehicles. In addition, most parts used in vehicles today must withstand temperature extremes from the hottest desert to the coldest Arctic environments and still maintain their integrity. With only a handful of stock materials available for 3D printers, meeting the automaker’s unique demands has not been possible.
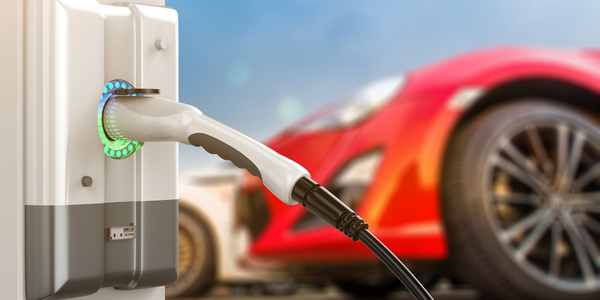
Case Study
Electric/Hybrid Vehicle Propulsion System
Tecnalia is experienced in the automotive sector and in the development of controllers embedded in powertrain ECUs. Implementing three models that emulate the unavailable functioning and communications electronic control units (ECUs) for an electric/hybrid vehicle propulsion system.