下载PDF
WD-40 keeps business running smoothly with QlikView
技术
- 分析与建模 - 实时分析
适用行业
- 消费品
适用功能
- 销售与市场营销
- 采购
用例
- 供应链可见性(SCV)
- 补货预测
服务
- 数据科学服务
挑战
WD-40, a global consumer products organization, was facing challenges in analyzing reported data and gaining insights into customer behavior. The company was relying on hard copy weekly reports to provide crucial business detail, which was putting increasing pressure on the IT department to produce more meaningful sales information in a user-friendly, real-time application. The traditional reports created by the company’s previous ERP system were both costly to produce and lacked important detail. A data analysis tool was needed to support WD-40’s growing business and to ease the pressure on IT resources. The company also needed applications that would support, speed up and simplify financial reporting to its parent in the US, a logistics application for better order-to-delivery efficiency and pan-European sales analysis for proactive management.
关于客户
WD-40 Company is a global consumer products organization, renowned for its range of popular household brands, which are found under the sink, in the garage and in the toolboxes of homes throughout the world. Its products are now sold in more than 160 countries worldwide. The company recorded sales of $242.5 million in 2004. WD-40 has grown to more than 254 employees worldwide, employing 42 at its UK headquarters in Milton Keynes.
解决方案
WD-40 deployed QlikView to 35 employees in less than two weeks. QlikView now supports the company’s sales, supply chain, and finance departments, enabling WD-40 to deliver data reports faster, reduce the time between order and delivery, and streamline pan-European sales analyses. Plus, with QlikView Server, WD-40 easily handles the large data volume of 500,000 order lines of point-of-sale records. The software integrated easily with WD-40’s source system, Scala, and simply read in data from the database and held it there ready for analysis, as and when it was needed. WD-40’s IT department did not require any specialist training. The team was able to identify the data it needed to access easily via QlikView.
运营影响
相关案例.
.png)
Case Study
Improving Vending Machine Profitability with the Internet of Things (IoT)
The vending industry is undergoing a sea change, taking advantage of new technologies to go beyond just delivering snacks to creating a new retail location. Intelligent vending machines can be found in many public locations as well as company facilities, selling different types of goods and services, including even computer accessories, gold bars, tickets, and office supplies. With increasing sophistication, they may also provide time- and location-based data pertaining to sales, inventory, and customer preferences. But at the end of the day, vending machine operators know greater profitability is driven by higher sales and lower operating costs.
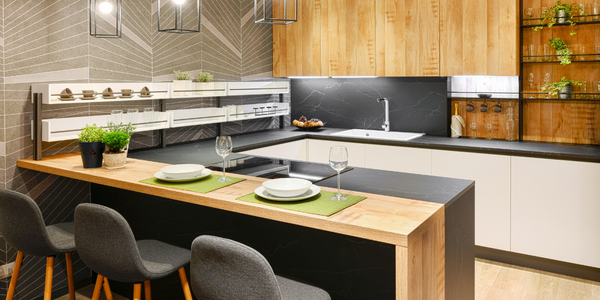
Case Study
Series Production with Lot-size-1 Flexibility
Nobilia manufactures customized fitted kitchens with a lot size of 1. They require maximum transparency of tracking design data and individual processing steps so that they can locate a particular piece of kitchen furniture in the sequence of processes.
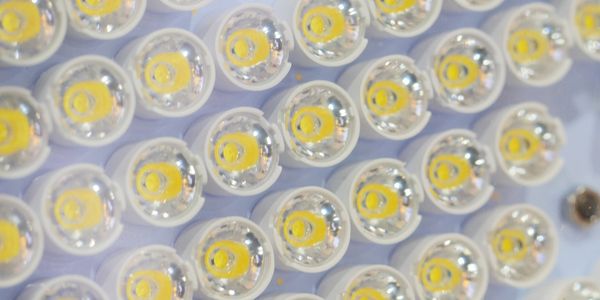
Case Study
American Eagle Achieves LEED with GE LED Lighting Fixtures
American Eagle Outfitters (AEO) was in the process of building a new distribution center. The AEO facility management team decided to look at alternate options for lighting layout that could provide energy and maintenance savings. AEO would need a full-time maintenance employee just to replace burned-out fluorescent tubes.
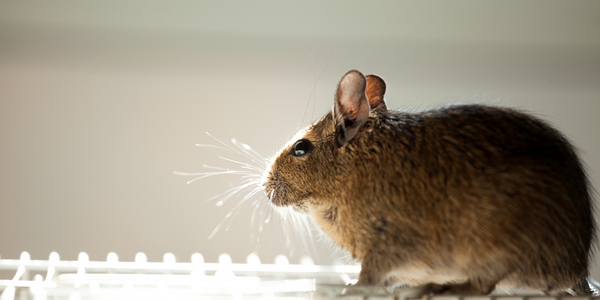
Case Study
Revolutionizing Rodent Control
From pet- and child-safe traps, to touch-free and live-catch rodent control solutions, Victor continues to stay committed to producing superior products that meet the varying needs of today’s pest control professionals. And, with a long standing history supporting customers in the food processing, service, and retail settings, Victor knew that strict regulations were costing organizations thousands of dollars in excess overhead trying to manage their rodent-control solutions. Trap inspections in these environments are often difficult and time consuming, requiring personnel to manually check a trap’s status multiple times per day, amounting to over six hours of manual labor. Victor is looking for an innovative way to increase operational efficiencies with the use of technology.