下载PDF
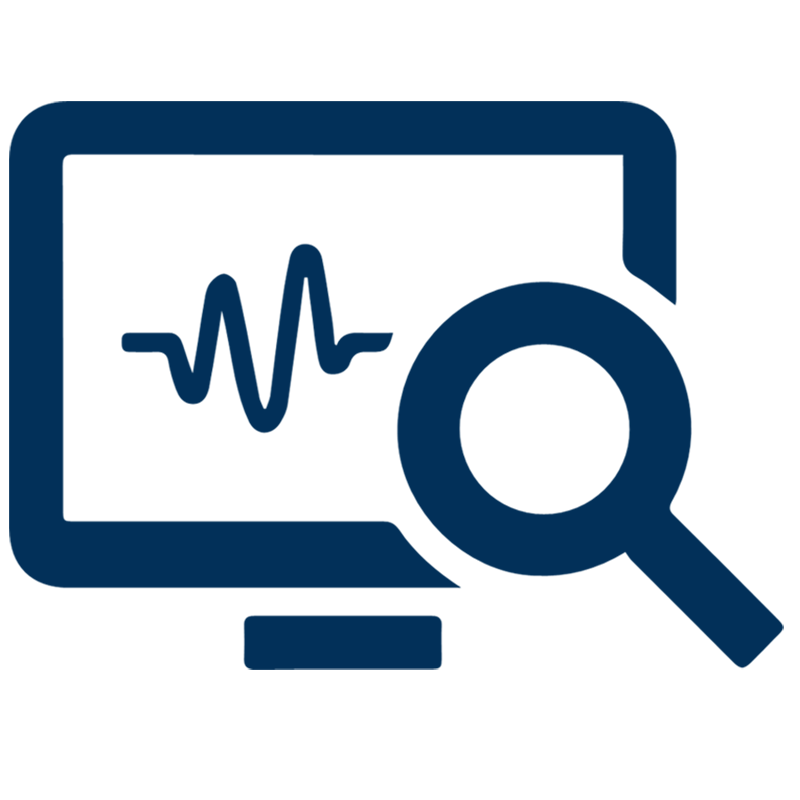
机器状态监测
概述
机器状态监测是监测振动和温度等参数的过程,以识别表明性能下降或即将发生故障的变化。它是预测性维护解决方案的必要组成部分,允许在发生故障之前安排维护,或采取其他措施来防止机器损坏和生产损失。除了改进维护计划之外,状态监测还提供了价值。例如,提高对机器操作的可见性可以指出产品缺陷的根本原因,并可以支持能源消耗的优化。
适用行业
- 设备与机械
适用功能
- 离散制造
- 维护
市场规模
2017 年机器状态监测市场价值 22.1 亿美元,预计到 2024 年将达到 35 亿美元,预测期内的复合年增长率为 6.7%。
到 2023 年,机器状态监测设备市场将突破 32 亿美元。
资料来源: P&S Intelligence
商业观点
机器状态监测的优势是什么?
- 提高机器可用性和可靠性
- 提高运营效率
- 改进风险管理(减少停机时间)
- 降低维护成本(更好的规划)
- 减少备件库存
- 提高安全性
- 提高了对机器状况的了解(可能的机器安全短期过载)
- 延长机器的使用寿命
- 改善客户关系(减少计划/计划外停机时间)
- 消除长期故障(根本原因分析和重新设计)
- 减少因维护或重新组装不当导致的大修后故障
部署挑战
在决定使用机器状态监控和故障诊断时必须权衡哪些缺点?
- 监控设备成本(通常很大)
- 运营成本(运行程序)
- 需要熟练的人员
- 需要强有力的管理承诺
- 通常需要大量的运行时间来收集机器历史和趋势
- 与增加的利润相比,降低的成本通常更难作为收益出售给管理层。
案例研究.
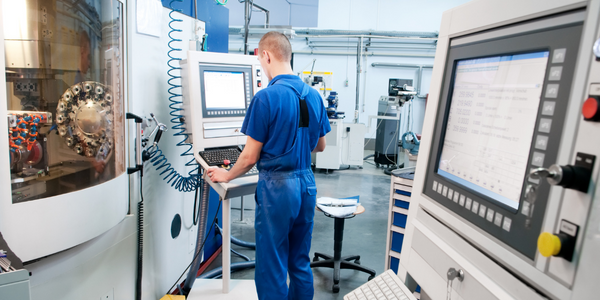
Case Study
MachineMetrics helped Carolina Precision saved over $1.5M on machine monitoring
Gary Bruner, the president of Carolina Precision Manufacturing, a contract manufacturer that specializes in small-diameter, close-tolerance CNC Swiss turned parts, had a problem. Over breakfast that morning, Gary had logged onto the MachineMetrics monitoring system on his laptop at home to check the status of his machines assigned to a lights-out operation, but saw immediately that two of his machines were not in production. “What’s wrong with machines 35 and 36?” he thought to himself. Upon arrival to the shop, Gary learned from his operator on duty that this type of hold up was nothing out of the ordinary, and was in fact a product of inefficient startup procedures that had simply never been analyzed or augmented previously. In an industry with razor thin margins, Gary understood that the keys to growth and success were in efficiency and quality. He understood the importance of keeping tabs on production stats, job status, uptime, and setup. However, there was no way to know how well machines were doing in real time. What was causing this additional downtime? Furthermore, CPM’s current methods of measurement and data collection were not only time consuming, but had quickly becoming outdated. Historically, CPM had an employee dedicated to the collection of utilization data. This employee would walk around to each of the machines, collect scrap tickets post-production, talk to operators, and record yesterday’s data into their current ERP system; not to mention that this manual data collection was prone to errors, and would take upwards of 2 hours per day. Without the ability to visualize their results, the recorded data was not very actionable.
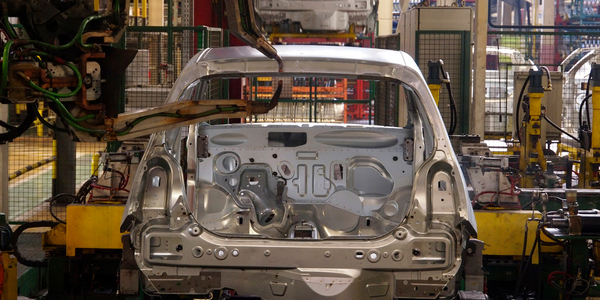
Case Study
Car Manufacturer Test IoT Solution on Test Vehicles
For each new model, Volvo Cars builds a number of test cars that are driven for a long time in a variety of locations around the world. The test cars gather data that are useful during the development of the car and Volvo Cars wanted online access to this data. Volvo Cars set a number of requirements for the solution: it had to be built on standards to allow for quick implementation and expansion, and it needed to maintain the highest security standards – an obvious requirement in light of the fierce competition in the automotive industry.