Download PDF
3D Printed Prototypes Streamline Equipment Introduction
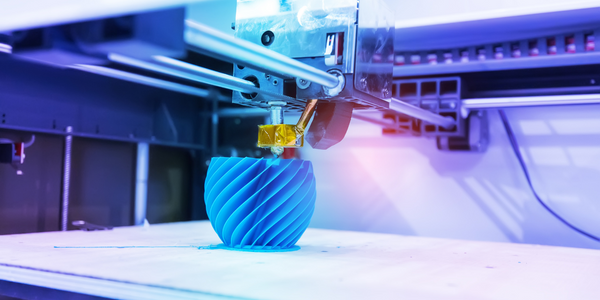
Applicable Industries
- Automotive
Applicable Functions
- Product Research & Development
Use Cases
- Additive Manufacturing
Services
- Hardware Design & Engineering Services
The Challenge
Vauxhall set out to introduce a modified process hanger with a new part that would be used to support each vehicle body throughout the production process. This part is a critical piece and had to perfectly fit both the machinery and the auto body to create correct clearances and avoid damage during production.
The Customer
Vauxhall Motors
About The Customer
Vauxhall Motors is a British automotive manufacturing and distribution company headquartered in Luton, with more than 4,000 employees.
The Solution
InfusionTech advised that 3D printed tools using the ProJet 660 Color Jet printing in combination with their infusion machine would deliver the accuracy and strength required to lift entire vehicles down the line during testing.
Operational Impact
Quantitative Benefit
Related Case Studies.
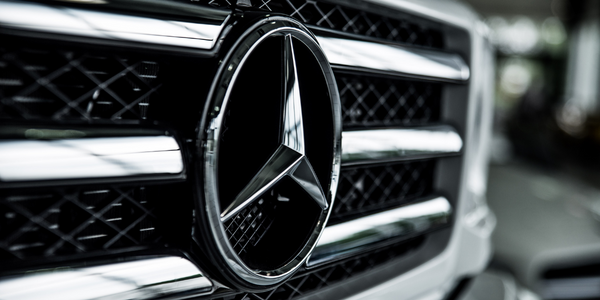
Case Study
Integral Plant Maintenance
Mercedes-Benz and his partner GAZ chose Siemens to be its maintenance partner at a new engine plant in Yaroslavl, Russia. The new plant offers a capacity to manufacture diesel engines for the Russian market, for locally produced Sprinter Classic. In addition to engines for the local market, the Yaroslavl plant will also produce spare parts. Mercedes-Benz Russia and his partner needed a service partner in order to ensure the operation of these lines in a maintenance partnership arrangement. The challenges included coordinating the entire maintenance management operation, in particular inspections, corrective and predictive maintenance activities, and the optimizing spare parts management. Siemens developed a customized maintenance solution that includes all electronic and mechanical maintenance activities (Integral Plant Maintenance).
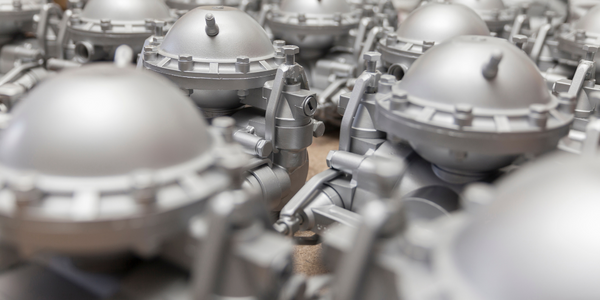
Case Study
Monitoring of Pressure Pumps in Automotive Industry
A large German/American producer of auto parts uses high-pressure pumps to deburr machined parts as a part of its production and quality check process. They decided to monitor these pumps to make sure they work properly and that they can see any indications leading to a potential failure before it affects their process.