Download PDF
Accelerating automotive assembly and test system design with SolidWorks Premium
Technology Category
- Analytics & Modeling - Predictive Analytics
- Application Infrastructure & Middleware - Data Visualization
- Functional Applications - Product Lifecycle Management Systems (PLM)
Applicable Industries
- Automotive
Applicable Functions
- Product Research & Development
- Quality Assurance
Services
- Software Design & Engineering Services
- Training
The Challenge
AAA engineers routinely work with large assemblies of between 1,000 and 5,000 components. In 2004, the company decided to reevaluate its design platform, focusing on large-assembly design capabilities. They had previously used Autodesk Inventor but wanted to assess other options like SolidWorks, Solid Edge, and Pro/ENGINEER. The goal was to find a more intuitive and easier-to-use software that could also support assembly analysis. The company ran a benchmark project using both SolidWorks and Inventor to validate their assumptions.
About The Customer
Assembly & Test Worldwide (ATW) operates five separate divisions, including its Advanced Assembly Automation (AAA) division, which specializes in developing component assembly and testing systems for the automotive industry. AAA engineers first moved to a 3D development platform in 2001 when the company transitioned from AutoCAD® 2D software to the Autodesk Inventor® 3D CAD system. After using Inventor software for more than three years, management decided to reevaluate the company’s design platform in 2004, with a particular focus on assessing large-assembly design capabilities.
The Solution
AAA decided to transition to SolidWorks software after a successful benchmark project. The company initially implemented 20 seats of SolidWorks Professional and later added more seats, including SolidWorks Premium. The transition included basic and advanced modeling as well as SolidWorks Simulation training. The move to SolidWorks provided an impetus for process improvement, standardization, and automation. AAA engineers completed all new projects using SolidWorks software, which helped in reducing design costs and rework, thereby boosting throughput. The integrated assembly analysis capabilities of SolidWorks Simulation allowed AAA to optimize designs and reduce material usage.
Operational Impact
Quantitative Benefit
Related Case Studies.
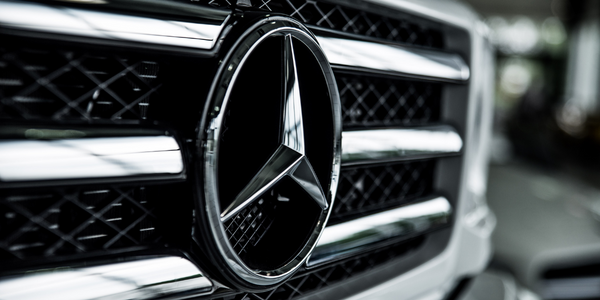
Case Study
Integral Plant Maintenance
Mercedes-Benz and his partner GAZ chose Siemens to be its maintenance partner at a new engine plant in Yaroslavl, Russia. The new plant offers a capacity to manufacture diesel engines for the Russian market, for locally produced Sprinter Classic. In addition to engines for the local market, the Yaroslavl plant will also produce spare parts. Mercedes-Benz Russia and his partner needed a service partner in order to ensure the operation of these lines in a maintenance partnership arrangement. The challenges included coordinating the entire maintenance management operation, in particular inspections, corrective and predictive maintenance activities, and the optimizing spare parts management. Siemens developed a customized maintenance solution that includes all electronic and mechanical maintenance activities (Integral Plant Maintenance).
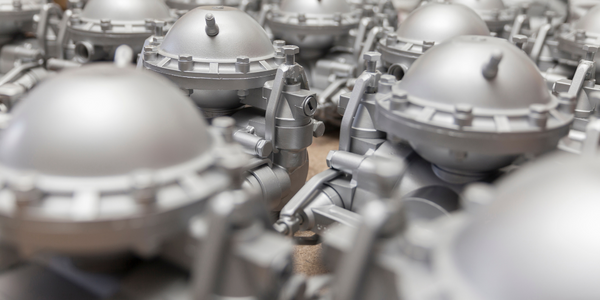
Case Study
Monitoring of Pressure Pumps in Automotive Industry
A large German/American producer of auto parts uses high-pressure pumps to deburr machined parts as a part of its production and quality check process. They decided to monitor these pumps to make sure they work properly and that they can see any indications leading to a potential failure before it affects their process.