Download PDF
Advanced Simulation of Seaflex Mooring System with ProteusDS
Technology Category
- Infrastructure as a Service (IaaS) - Virtual Private Cloud
- Wearables - Virtual Reality Glasses, Headsets & Controllers
Applicable Industries
- Marine & Shipping
- Renewable Energy
Applicable Functions
- Product Research & Development
Use Cases
- Virtual Reality
- Virtual Training
Services
- System Integration
- Training
The Challenge
Dynamic Systems Analysis Ltd. (DSA) has been providing custom software solutions for the ocean engineering industry for over a decade. Their software, ProteusDS and ShipMo3D, are used to test virtual prototypes of vessels and equipment operating in ocean conditions. The challenge was to understand the dynamic effects of ocean current, wind, and waves on the Seaflex mooring system, a product of Seaflex AB. This system is custom made for each location based on the expected forces and conditions. The Seaflex system is used in a variety of applications including marinas, wave attenuators, navigational buoys, residential pontoons/docks, floating helicopter platforms, seaplane terminals, floating fish farms, floating solar energy parks, floating houses, wave energy converters, and more. The challenge was to estimate the effect of current, wind, and waves on the mooring and to predict the exact response of the mooring installation a priori to satisfy insurers or engineers.
About The Customer
Seaflex AB is the maker of the Seaflex mooring system, an engineered mooring system that is custom made for each particular location based on the expected forces and conditions. The Seaflex system can be used for a variety of applications including marinas, wave attenuators, navigational buoys, residential pontoons/docks, floating helicopter platforms, seaplane terminals, floating fish farms, floating solar energy parks, floating houses, wave energy converters, and more. The unique construction of the system offers unsurpassed dampening of forces which aids in the longevity of the structures it is anchoring. Inhouse engineers at Seaflex AB help design the best solution for all requirements.
The Solution
DSA developed a simulation capability for the Seaflex mooring system in ProteusDS. This allowed them to create virtual prototypes of marine structures to answer questions related to engineering design, planning, training, operations, and safety. The simulation capability helped in understanding the dynamic effects of ocean current, wind, and waves on the Seaflex mooring system. This significantly reduced the risk and uncertainty of vessel motions and loads on equipment in an ocean environment, resulting in safer designs and lower risk and project cost. The model was successfully implemented, and the response of the Seaflex system can now be predicted using the full capabilities of the wind, wave, and current models in ProteusDS. The Seaflex team now has the capabilities in-house to model a wide range of applications and has access to support from the DSA team for all of their projects.
Operational Impact
Related Case Studies.
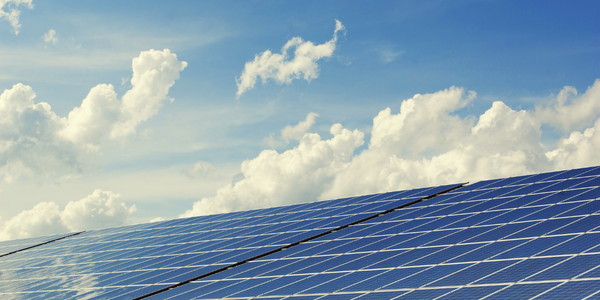
Case Study
Remote Monitoring & Predictive Maintenance App for a Solar Energy System
The maintenance & tracking of various modules was an overhead for the customer due to the huge labor costs involved. Being an advanced solar solutions provider, they wanted to ensure early detection of issues and provide the best-in-class customer experience. Hence they wanted to automate the whole process.
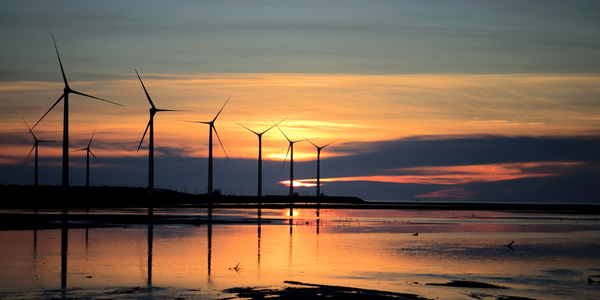
Case Study
Vestas: Turning Climate into Capital with Big Data
Making wind a reliable source of energy depends greatly on the placement of the wind turbines used to produce electricity. Turbulence is a significant factor as it strains turbine components, making them more likely to fail. Vestas wanted to pinpoint the optimal location for wind turbines to maximize power generation and reduce energy costs.
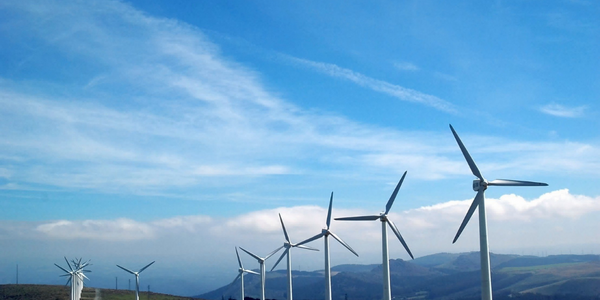
Case Study
Siemens Wind Power
Wind provides clean, renewable energy. The core concept is simple: wind turbines spin blades to generate power. However, today's systems are anything but simple. Modern wind turbines have blades that sweep a 120 meter circle, cost more than 1 million dollars and generate multiple megawatts of power. Each turbine may include up to 1,000 sensors and actuators – integrating strain gages, bearing monitors and power conditioning technology. The turbine can control blade speed and power generation by altering the blade pitch and power extraction. Controlling the turbine is a sophisticated job requiring many cooperating processors closing high-speed loops and implementing intelligent monitoring and optimization algorithms. But the real challenge is integrating these turbines so that they work together. A wind farm may include hundreds of turbines. They are often installed in difficult-to-access locations at sea. The farm must implement a fundamentally and truly distributed control system. Like all power systems, the goal of the farm is to match generation to load. A farm with hundreds of turbines must optimize that load by balancing the loading and generation across a wide geography. Wind, of course, is dynamic. Almost every picture of a wind farm shows a calm sea and a setting sun. But things get challenging when a storm goes through the wind farm. In a storm, the control system must decide how to take energy out of gusts to generate constant power. It must intelligently balance load across many turbines. And a critical consideration is the loading and potential damage to a half-billion-dollar installed asset. This is no environment for a slow or undependable control system. Reliability and performance are crucial.
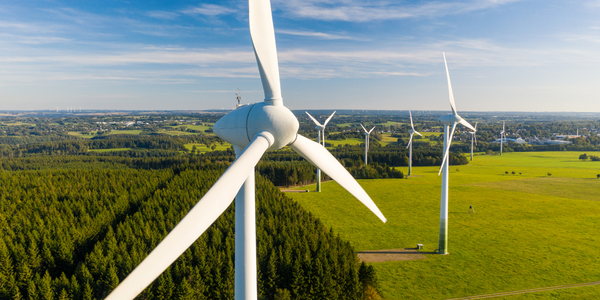
Case Study
Remote Monitoring and Control for a Windmill Generator
As concerns over global warming continue to grow, green technologies are becoming increasingly popular. Wind turbine companies provide an excellent alternative to burning fossil fuels by harnessing kinetic energy from the wind and converting it into electricity. A typical wind farm may include over 80 wind turbines so efficient and reliable networks to manage and control these installations are imperative. Each wind turbine includes a generator and a variety of serial components such as a water cooler, high voltage transformer, ultrasonic wind sensors, yaw gear, blade bearing, pitch cylinder, and hub controller. All of these components are controlled by a PLC and communicate with the ground host. Due to the total integration of these devices into an Ethernet network, one of our customers in the wind turbine industry needed a serial-to-Ethernet solution that can operate reliably for years without interruption.
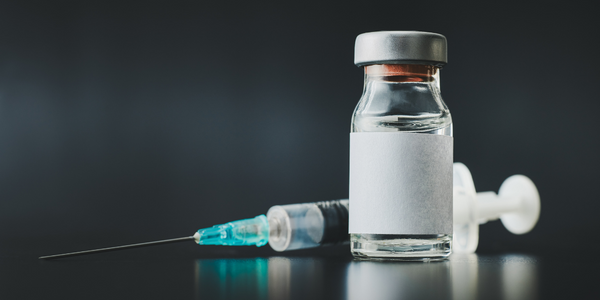
Case Study
Temperature monitoring for vaccine fridges
Dulas wanted a way to improve the reliability of the cold chain, facilitating maintenance and ensuring fewer vaccines are spoiled. Dulas wanted an M2M solution which would enable them to record and report the temperature inside vaccine refrigerators.
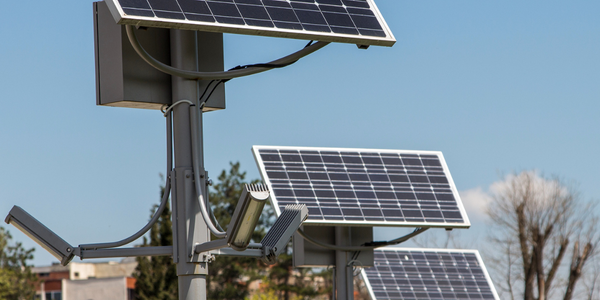
Case Study
IoT Powering A New Way to Light Streets with Bifacial Solar Panels
When James Meringer’s commercial contracting business experienced a rapid increase in solar projects, he also saw an opportunity to extend the benefits of solar by using the bifacial solar panels he’d become familiar with in new ways. Bifacial solar panels enable sunlight from both sides of the panel, making it a more efficient harvest of solar power. Seeing the panel’s power, James and his team set out to use the same technology for street lighting. Until now, solar street lights have served as utilitarian solutions that force designers to choose between form and function. The Mira Bella Energy team has changed that.