Download PDF
Arkal Automotive Enhances FEA Data Creation Workflow with HyperMesh and CADdoctor
Applicable Industries
- Automotive
Use Cases
- Time Sensitive Networking
- Virtual Prototyping & Product Testing
The Challenge
Arkal Automotive, amidst its company growth and increased demand, was facing a significant challenge in its simulation department. The critical need was to reduce the preprocessing time, which was becoming a bottleneck in their operations. Interestingly, the issue was not related to the CPU time, but was primarily associated with the model preparation phase. The company was struggling to streamline and accelerate the creation of models, which was slowing down their overall workflow and affecting their productivity.
About The Customer
Arkal Automotive is a growing company in the automotive industry, facing increased demand for its products and services. The company has a simulation department that plays a crucial role in its operations. The department is responsible for the preprocessing of data, which includes the preparation of models. However, due to the company's growth and the increased demand, the simulation department was facing challenges in reducing the preprocessing time, particularly in the model preparation phase. The company needed a solution that could streamline and accelerate the model creation process, thereby enhancing their overall workflow and productivity.
The Solution
To address this challenge, Arkal Automotive collaborated with Altair and Elysium Co. Ltd. The joint effort was aimed at providing the required functionality to meet the customer needs. The solution relied on standardized, state-of-the-art tools, specifically the CADdoctor Translation and Simplification platforms. These platforms were used to reduce the time spent in creating simplified models. The solution involved creating a CAD model free of fillets, chamfers, ribs, and bosses, which was more suitable for HyperMesh to use in the creation of 2D and 3D meshes.
Operational Impact
Quantitative Benefit
Related Case Studies.
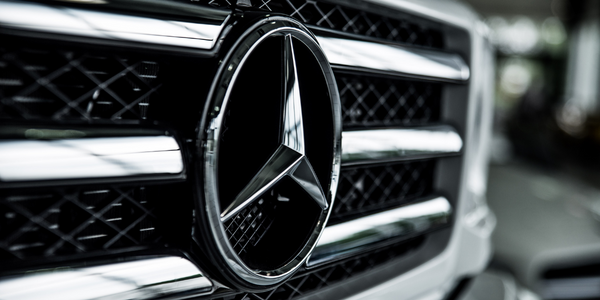
Case Study
Integral Plant Maintenance
Mercedes-Benz and his partner GAZ chose Siemens to be its maintenance partner at a new engine plant in Yaroslavl, Russia. The new plant offers a capacity to manufacture diesel engines for the Russian market, for locally produced Sprinter Classic. In addition to engines for the local market, the Yaroslavl plant will also produce spare parts. Mercedes-Benz Russia and his partner needed a service partner in order to ensure the operation of these lines in a maintenance partnership arrangement. The challenges included coordinating the entire maintenance management operation, in particular inspections, corrective and predictive maintenance activities, and the optimizing spare parts management. Siemens developed a customized maintenance solution that includes all electronic and mechanical maintenance activities (Integral Plant Maintenance).
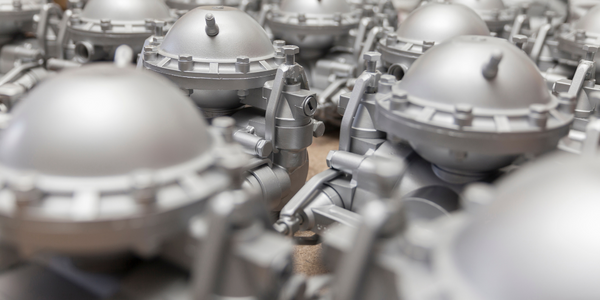
Case Study
Monitoring of Pressure Pumps in Automotive Industry
A large German/American producer of auto parts uses high-pressure pumps to deburr machined parts as a part of its production and quality check process. They decided to monitor these pumps to make sure they work properly and that they can see any indications leading to a potential failure before it affects their process.