Download PDF
Asset Management software helps leading NASCAR team Drive Down Costs and Optimize Performance
Technology Category
- Functional Applications - Enterprise Resource Planning Systems (ERP)
Applicable Industries
- Automotive
Applicable Functions
- Discrete Manufacturing
- Warehouse & Inventory Management
Use Cases
- Track & Trace of Assets
- Inventory Management
Services
- System Integration
The Challenge
Hendrick Motorsports’ manufacturing complex contains six buildings, each with its own inventory warehouse. These include separate buildings for each individual racing team’s facilities. As each car is tested and modified for optimum performance on varying racetracks, its crews use parts from these buildings. Documenting the performance of each part in each possible race car configuration is important. Hendrick Motorsports (HMS) had been tracking these activities manually, which was tedious, time consuming, and costly. Scott Lampe, chief financial officer for HMS, is responsible for optimizing resource use for both on-track performance and cost. Toward this end, he implemented the Microsoft’s Business Solutions-Dynamics SL financial program, which he wanted to integrate into a single, compatible system to manage inventory, track parts usage, and maintain a historical profile of car performance. This integration required overcoming the following challenges: Coordinating information across 6 warehouses that are operated as independent entities, Tracking usage of approximately 150 components on each car, Monitoring performance reliability, Getting the system up and running within 4 months.
About The Customer
Hendrick Motorsports (HMS) is a leading NASCAR team based in Charlotte, North Carolina. The company operates a 65-acre racing complex where it designs, tests, and builds race cars for notable NASCAR drivers such as Jeff Gordon, Terry Labonte, and Jimmie Johnson. Since its inception in 1984, Hendrick has grown from a one-car race team to a six-team operation that has won five of the last eleven NASCAR Nextel Cup Championships. These include four consecutive titles – the sports first-ever. The manufacturing complex of Hendrick Motorsports contains six buildings, each with its own inventory warehouse. These include separate buildings for each individual racing team’s facilities, such as the 24/48 Shop, which supports Jeff Gordon and Jimmie Johnson and the 5/25 Shop, which supports Kyle Bush and Brian Vickers. There is also an engine shop, body shop, and chassis shop.
The Solution
After reviewing EAM alternatives, HMS chose the AVEVA EAM solution. AVEVA’ Industrial Rapid Implementation Methodology (InRIM) enabled HMS to install the EAM software in about half the industry standard implementation time. Having met the first critical milestone, which was for centralizing purchasing and warehousing, HMS and AVEVA turned their focus to monitoring parts usage. Approximately 150 components on each car are monitored by condition, such as time-to-failure or usage. Collecting accurate data is critical because HMS builds cars specifically for individual racetracks and tests configurations for each. The AVEVA software helps track the configurations for each race, including changes made during practice. The AVEVA solution also helps HMS track parts usage to assure reliability. With the first phase successfully completed, HMS has recently launched two new initiatives using AVEVA capabilities. HMS also upgraded to Avantis.PRO Enterprise Asset Management with multi-site asset management capabilities. Previously, to track inventory in all six warehouses HMS had to work with multiple instances. Now they can manage and monitor six warehouses from a single instance, which significantly contributes to their corporate directive to streamline operations and standardize parts.
Operational Impact
Quantitative Benefit
Related Case Studies.
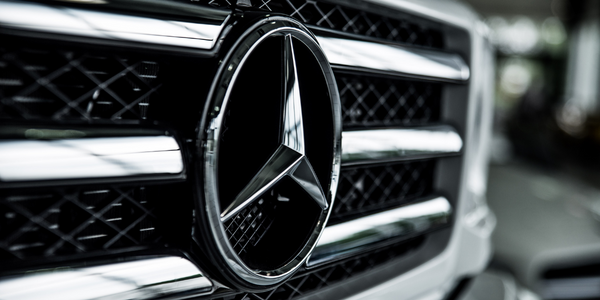
Case Study
Integral Plant Maintenance
Mercedes-Benz and his partner GAZ chose Siemens to be its maintenance partner at a new engine plant in Yaroslavl, Russia. The new plant offers a capacity to manufacture diesel engines for the Russian market, for locally produced Sprinter Classic. In addition to engines for the local market, the Yaroslavl plant will also produce spare parts. Mercedes-Benz Russia and his partner needed a service partner in order to ensure the operation of these lines in a maintenance partnership arrangement. The challenges included coordinating the entire maintenance management operation, in particular inspections, corrective and predictive maintenance activities, and the optimizing spare parts management. Siemens developed a customized maintenance solution that includes all electronic and mechanical maintenance activities (Integral Plant Maintenance).
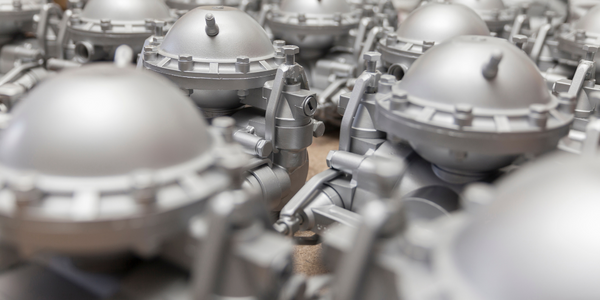
Case Study
Monitoring of Pressure Pumps in Automotive Industry
A large German/American producer of auto parts uses high-pressure pumps to deburr machined parts as a part of its production and quality check process. They decided to monitor these pumps to make sure they work properly and that they can see any indications leading to a potential failure before it affects their process.