Download PDF
Boosting Employee Productivity at PayNet with Nintex K2 Five
Applicable Functions
- Product Research & Development
Use Cases
- Inventory Management
- Time Sensitive Networking
Services
- System Integration
The Challenge
PayNet, a leading financial services company in Malaysia, was grappling with cumbersome internal processes that were diverting time and resources away from customers. The basic leave management system (LMS) for employees was creating difficulties for HR and supervisors in tracking leave records and their statuses, affecting resource allocation. Major workflows such as the incident management system (IMS) and change management system (CMS) were also affected. PayNet’s helpdesk team and change management secretariat had to consolidate, monitor and analyze all the different information needed to manage customer requests. The challenge was to deliver a simplified process for all of this manual work.
About The Customer
PayNet is a leading financial services company in Malaysia that builds and operates world-class payment systems and financial market infrastructures. These systems and infrastructures safely, reliably and efficiently enable the functioning and development of Malaysia’s financial system, as well as the economy as a whole. PayNet administers e-payments and money transfers for its customers, requiring all internal processes to work together seamlessly. The company is committed to improving its internal processes to ensure business success and customer satisfaction.
The Solution
PayNet implemented Nintex K2 Five to automate business-critical processes while providing the flexibility needed to improve an already-siloed environment. They wanted flexibility to customize workflow systems to suit user and business requirements, as well as streamline standalone systems for efficiency. PayNet also recruited the professional services team to help get its solutions up and running more quickly. Nintex K2 Five experts educated the PayNet team on form development, showing how data can be extracted from different sources and displayed on a single page, as well as how to address delivery cycle requirements. Since May 2014, when PayNet began its automation journey by integrating Nintex K2 Five workflows with Microsoft SharePoint 2013, there have been efficiency improvements across all departments.
Operational Impact
Quantitative Benefit
Related Case Studies.
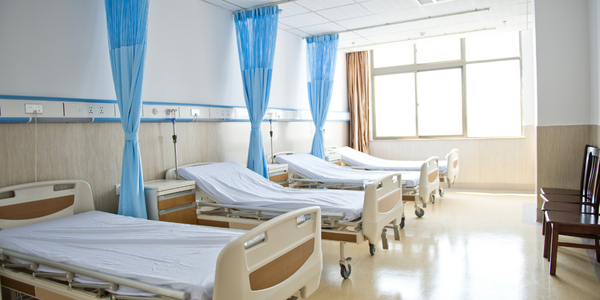
Case Study
Hospital Inventory Management
The hospital supply chain team is responsible for ensuring that the right medical supplies are readily available to clinicians when and where needed, and to do so in the most efficient manner possible. However, many of the systems and processes in use at the cancer center for supply chain management were not best suited to support these goals. Barcoding technology, a commonly used method for inventory management of medical supplies, is labor intensive, time consuming, does not provide real-time visibility into inventory levels and can be prone to error. Consequently, the lack of accurate and real-time visibility into inventory levels across multiple supply rooms in multiple hospital facilities creates additional inefficiency in the system causing over-ordering, hoarding, and wasted supplies. Other sources of waste and cost were also identified as candidates for improvement. Existing systems and processes did not provide adequate security for high-cost inventory within the hospital, which was another driver of cost. A lack of visibility into expiration dates for supplies resulted in supplies being wasted due to past expiry dates. Storage of supplies was also a key consideration given the location of the cancer center’s facilities in a dense urban setting, where space is always at a premium. In order to address the challenges outlined above, the hospital sought a solution that would provide real-time inventory information with high levels of accuracy, reduce the level of manual effort required and enable data driven decision making to ensure that the right supplies were readily available to clinicians in the right location at the right time.
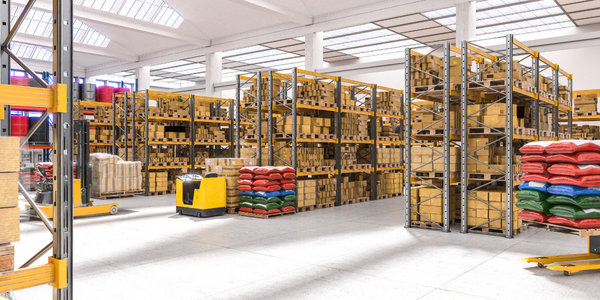
Case Study
Hardware Retailer Uses Data Warehouse to Track Inventory
Ace tracked which products retailers ordered, when they were ordered and shipped. However, the company could not track or forecast actual sales. Data used for reporting was up to a one-week old, owing to performance and data cleansing issues. Requirement to integrate wholesale and inventory data with POS data to help drive key business decisions, improve category management, lower inventory costs and optimize pricing. Reliance on custom coding to integrate POS data was excessively resource intensive and led to major performance constraints.
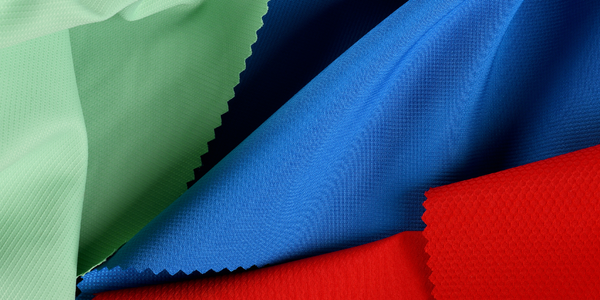
Case Study
Remake Enterprise-to-production System
The client was running a legacy material flow tracking system and wanted to replace the system with a more effective one as the system was increasingly expensive to maintain and support and also was not extendable. The client's IT landscape was filled with modern applications and it was difficult to interface the material flow tracking system with modern applications.