Download PDF
Building an Efficient CAE Simulation Platform at the Pan Asia Automotive Technology Center
Technology Category
- Analytics & Modeling - Digital Twin / Simulation
- Platform as a Service (PaaS) - Application Development Platforms
Applicable Industries
- Automotive
- Cement
Applicable Functions
- Maintenance
- Product Research & Development
Use Cases
- Virtual Prototyping & Product Testing
- Virtual Reality
Services
- System Integration
The Challenge
The Pan Asia Automotive Technology Center (PATAC), a joint venture between General Motors and SAIC Motor, was facing challenges in managing its computer-aided engineering (CAE) simulation technology. As PATAC's analytical technology improved, the volume of its CAE analysis tasks increased, and the subject and application fields expanded. Engineers needed a system to store, reuse, and share models, and synchronize iterative design schemes in different simulation fields for collaboration. Additionally, PATAC was promoting the digital transformation of its research and development system. The company needed a simulation management platform to manage daily analysis work, structure CAE data systematically, improve visualization of results and processes, and track analysis cases more easily.
About The Customer
The Pan Asia Automotive Technology Center (PATAC) is a joint venture between General Motors and SAIC Motor. The company is involved in the design and development of vehicles and automotive systems. With the advancement of technology and increasing competition, PATAC is constantly innovating in the automotive industry. The company is also promoting the digital transformation of its research and development system. PATAC has been using Altair products since Altair entered the Chinese market and has accumulated a lot of experience in the application of Altair HyperWorks®, Altair PBS Works™, and other products.
The Solution
PATAC partnered with Altair to design, build, and implement a custom CAE simulation management platform. The platform was designed to cover all areas of vehicle and subsystem analysis. The construction of the platform began in 2017, and by the second half of 2018, the framework design and first phase of construction were completed. The system was put into practical application in areas including vehicle safety, NVH, vehicle dynamics, and structural and fluid analysis. The platform includes five main modules: HWI – full-vehicle rapid modeling module, Model Builder – master model management module, Simulation Manager – CAE data and load case management module, Process Manager – CAE project management module, and Dashboard – collaborative statistical data dashboard. The platform also integrates with PATAC’s project management system and seamlessly integrates with PBS Professional.
Operational Impact
Quantitative Benefit
Related Case Studies.
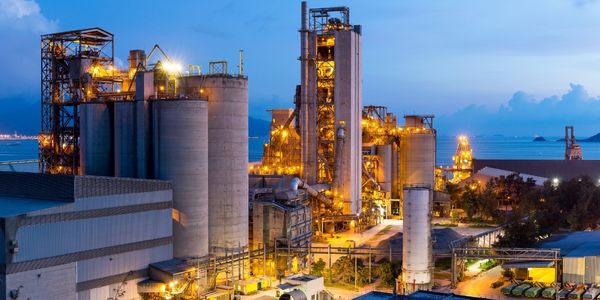
Case Study
System 800xA at Indian Cement Plants
Chettinad Cement recognized that further efficiencies could be achieved in its cement manufacturing process. It looked to investing in comprehensive operational and control technologies to manage and derive productivity and energy efficiency gains from the assets on Line 2, their second plant in India.
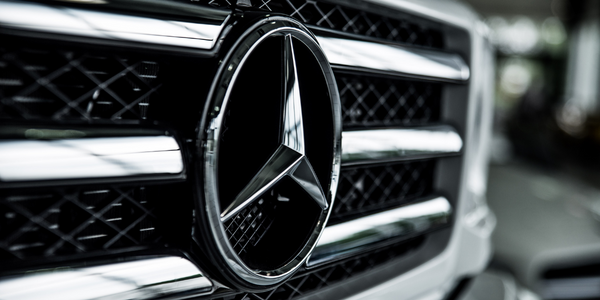
Case Study
Integral Plant Maintenance
Mercedes-Benz and his partner GAZ chose Siemens to be its maintenance partner at a new engine plant in Yaroslavl, Russia. The new plant offers a capacity to manufacture diesel engines for the Russian market, for locally produced Sprinter Classic. In addition to engines for the local market, the Yaroslavl plant will also produce spare parts. Mercedes-Benz Russia and his partner needed a service partner in order to ensure the operation of these lines in a maintenance partnership arrangement. The challenges included coordinating the entire maintenance management operation, in particular inspections, corrective and predictive maintenance activities, and the optimizing spare parts management. Siemens developed a customized maintenance solution that includes all electronic and mechanical maintenance activities (Integral Plant Maintenance).
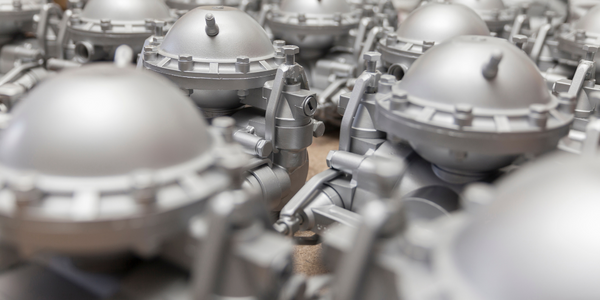
Case Study
Monitoring of Pressure Pumps in Automotive Industry
A large German/American producer of auto parts uses high-pressure pumps to deburr machined parts as a part of its production and quality check process. They decided to monitor these pumps to make sure they work properly and that they can see any indications leading to a potential failure before it affects their process.