Download PDF
Cleveland Golf's Product Innovation Through Simulation and Optimization Using HyperWorks
Technology Category
- Analytics & Modeling - Digital Twin / Simulation
- Sensors - Acoustic Sensors
Applicable Functions
- Product Research & Development
- Quality Assurance
Use Cases
- Virtual Prototyping & Product Testing
- Virtual Reality
Services
- Testing & Certification
The Challenge
Cleveland Golf, a leading golf club manufacturer, faced the challenge of meeting changing regulations for golf club design while consistently introducing new products that are precisely engineered for shape, feel, balance, sound, and performance. The United States Golf Association (USGA) imposes limitations on golf club heads, including the size of the grooves in wedges and irons, the dimensions of the head, and the permitted coefficient of restitution (COR) – or springiness – that is allowed in clubs. As clubs have improved, they've reached these limits and have the capability to go beyond them. This posed a significant challenge as Cleveland Golf needed to figure out how to continue to improve clubs without exceeding these limits. Additionally, the USGA recently changed the rules specifying groove size, impacting how future clubs will be designed. From an economic standpoint, consumers were not buying as many clubs as they did in the past, so Cleveland Golf needed to create more new and innovative products, not just variations on existing clubs.
About The Customer
Cleveland Golf, based in Huntington Beach, Calif., is a market-leading golf club manufacturer and a pioneer in the design and production of advanced clubs. The company is the developer of the number-one wedge in the golf industry. Cleveland Golf's engineering research team uses simulation to virtually assess and tune the performance of forward-looking designs to develop market-leading woods, irons, wedges, and putters. The company operates in a difficult regulatory and business environment, with the United States Golf Association (USGA) imposing limitations on golf club heads and consumers not buying as many clubs as they did in the past.
The Solution
Cleveland Golf employed the HyperWorks suite of software for CAE design simulation to address these challenges. The research team used this software to balance a variety of design variables, including materials, size, shape, weight placement, thickness patterns, and placement of internal ribs for durability, sound, and feel. They also used HyperStudy to optimize material properties, along with AcuSolve® to explore the club’s aerodynamics. In addition to evaluating the structural performance of prototypes, Cleveland Golf used simulation to predict the sound that the club head makes when striking the ball, employing modal analysis using the HyperWorks OptiStruct® solver. They compared new club designs with previous parts in running their sound analyses and used a robot that strikes golf balls consistently, enabling the engineers to test different design iterations and to measure the sound coming from the club. Player testing was also used for feedback on sound and feel and to compare Cleveland Golf clubs with others in the market.
Operational Impact
Quantitative Benefit
Related Case Studies.
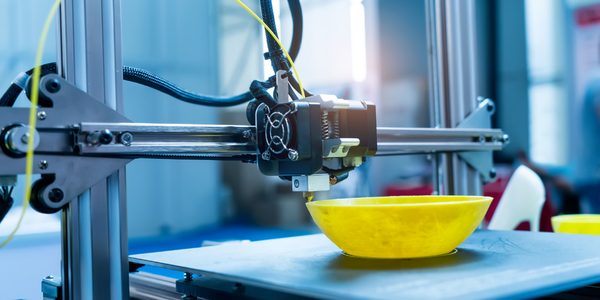
Case Study
Intralox Using Demo3D Case Study
Intralox strives to create significant economic value for our customers by optimizing their conveyance systems. Intralox wants to emulate real-world production environments for end users and OEMs working in multiple industries, including packaging, warehousing, parcel, beverage, brewery, food, tire, and consumer goods. They frequently had to perform physical tests to demonstrate to customers how ARB equipment would handle their products.
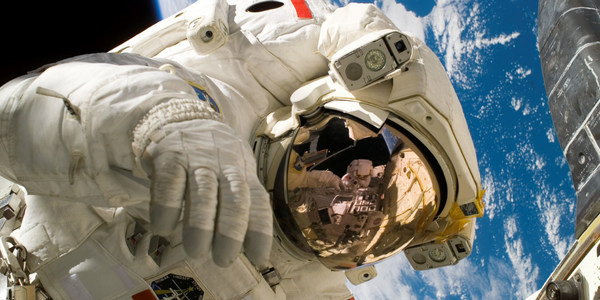
Case Study
General Dynamics Uses Wind River Simics to Meet NASA Challenge
In designing and building Fermi, the General Dynamics C4 Systems business unit was faced with a challenge: it needed to provide an environment that could support rigorous testing by multiple Fermi subsystem groups before the spacecraft hardware was available.
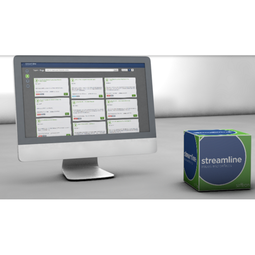
Case Study
Issue and Defect Resolution
One of the world's largest complex hardware manufacturers' business units, responsible for the post-product validation process, was looking to speed up its time to market and the time it took to identify and resolve process issues. Duplicate debugging hardware and software issues was eating up 70% of production time, slowing down time to market and costing money.