下载PDF
Cleveland Golf's Product Innovation Through Simulation and Optimization Using HyperWorks
技术
- 分析与建模 - 数字孪生/模拟
- 传感器 - 声学传感器
适用功能
- 产品研发
- 质量保证
用例
- 虚拟原型与产品测试
- 虚拟现实
服务
- 测试与认证
挑战
Cleveland Golf 是一家领先的高尔夫球杆制造商,面临着满足不断变化的高尔夫球杆设计法规的挑战,同时不断推出针对形状、感觉、平衡、声音和性能进行精确设计的新产品。美国高尔夫协会 (USGA) 对高尔夫球杆头施加了限制,包括挖起杆和铁杆中凹槽的尺寸、杆头尺寸以及球杆允许的恢复系数 (COR)(或弹性) 。随着俱乐部的进步,他们已经达到了这些极限,并且有能力超越它们。这构成了重大挑战,因为克利夫兰高尔夫需要弄清楚如何在不超过这些限制的情况下继续改进球杆。此外,美国高尔夫球协会最近更改了指定凹槽尺寸的规则,影响了未来球杆的设计方式。从经济角度来看,消费者不再像过去那样购买那么多球杆,因此克利夫兰高尔夫需要创造更多新的创新产品,而不仅仅是现有球杆的变体。
关于客户
克利夫兰高尔夫公司总部位于加利福尼亚州亨廷顿海滩,是市场领先的高尔夫球杆制造商,也是高级球杆设计和生产的先驱。该公司是高尔夫行业排名第一的挖起杆开发商。克利夫兰高尔夫公司的工程研究团队使用仿真来虚拟评估和调整前瞻性设计的性能,以开发市场领先的木杆、铁杆、挖起杆和推杆。该公司在艰难的监管和商业环境中运营,美国高尔夫协会 (USGA) 对高尔夫球杆头施加限制,消费者购买的球杆数量也不像过去那么多。
解决方案
Cleveland Golf 采用 HyperWorks 软件套件进行 CAE 设计仿真来应对这些挑战。研究团队使用该软件来平衡各种设计变量,包括材料、尺寸、形状、重量放置、厚度模式以及内部肋骨的放置,以实现耐用性、声音和感觉。他们还使用 HyperStudy 来优化材料特性,并使用 AcuSolve® 来探索球杆的空气动力学特性。除了评估原型的结构性能之外,Cleveland Golf 还利用 HyperWorks OptiStruct® 求解器进行模态分析,利用仿真来预测球杆头击球时发出的声音。他们在运行声音分析时将新的球杆设计与以前的零件进行比较,并使用能够一致击打高尔夫球的机器人,使工程师能够测试不同的设计迭代并测量来自球杆的声音。球员测试还用于获得声音和感觉的反馈,并将克利夫兰高尔夫球杆与市场上的其他高尔夫球杆进行比较。
运营影响
数量效益
相关案例.
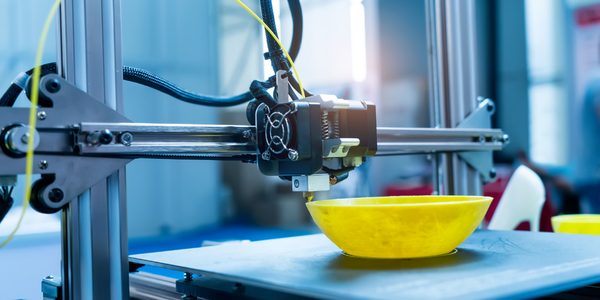
Case Study
Intralox Using Demo3D Case Study
Intralox strives to create significant economic value for our customers by optimizing their conveyance systems. Intralox wants to emulate real-world production environments for end users and OEMs working in multiple industries, including packaging, warehousing, parcel, beverage, brewery, food, tire, and consumer goods. They frequently had to perform physical tests to demonstrate to customers how ARB equipment would handle their products.
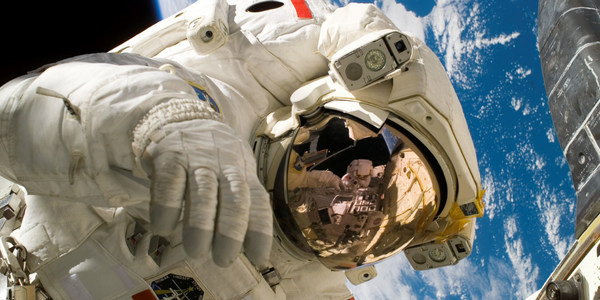
Case Study
General Dynamics Uses Wind River Simics to Meet NASA Challenge
In designing and building Fermi, the General Dynamics C4 Systems business unit was faced with a challenge: it needed to provide an environment that could support rigorous testing by multiple Fermi subsystem groups before the spacecraft hardware was available.
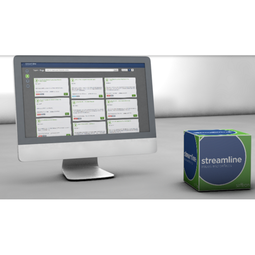
Case Study
Issue and Defect Resolution
One of the world's largest complex hardware manufacturers' business units, responsible for the post-product validation process, was looking to speed up its time to market and the time it took to identify and resolve process issues. Duplicate debugging hardware and software issues was eating up 70% of production time, slowing down time to market and costing money.