Download PDF
Collaborative Approach and Technology Investment: A Case Study of MBMO Architects and Sydney Adventist Hospital
Technology Category
- Infrastructure as a Service (IaaS) - Private Cloud
- Infrastructure as a Service (IaaS) - Public Cloud
Applicable Industries
- Healthcare & Hospitals
- Retail
Applicable Functions
- Product Research & Development
- Quality Assurance
Use Cases
- Construction Management
- Construction Site Monitoring
Services
- Testing & Certification
The Challenge
MBMO Architects, a leading studio in Sydney, has been involved in several significant projects, including the major redevelopment of the Sydney Adventist Hospital (San), Notre Dame University Clinical Education Centre, and various mixed-use residential and student accommodation developments. The challenge for MBMO was to maintain their commitment to early project involvement and collaboration with all stakeholders while delivering excellent design and commercial outcomes. The Sydney Adventist Hospital project, in particular, was a $200 million redevelopment, which required a high level of collaboration and technological support to ensure a successful outcome. The project involved seven sub-projects, including a 13-storey clinical tower, a multi-deck car park, a new entry building, and a student accommodation building, among others. The project's success was crucial for the hospital, which is Sydney's largest and oldest private hospital.
About The Customer
The customer in this case study is the Sydney Adventist Hospital (San), the largest and oldest private hospital in Sydney. The hospital was undergoing a major $200 million redevelopment, which involved seven sub-projects, including a 13-storey clinical tower, a multi-deck car park, a new entry building, and a student accommodation building, among others. The hospital's executive board was part of 'The San Alliance', a collaborative group that was formed to ensure the project's success. The hospital's principles remain centered on the health and wellness of people, and the redevelopment project was crucial for the hospital to continue providing high-quality healthcare services to its patients.
The Solution
MBMO Architects have been using Archicad in their projects since 1996, and it has been a key factor in their continued success. Archicad is used for everything from concept design to 1:1 3D detailing. It is considered the market leader in 3D technology due to its intuitive design, ease of use, and ability to export into mobile media platforms. Its documentation tool is very effective, as it links everything from details to finishes schedules into the Archicad model, which minimizes errors and double-ups, thus reducing risk. For the Sydney Adventist Hospital project, Archicad's high-quality rendering capability and mobile visualization app, BIMx, enabled the client to visualize exactly what each design was going to look like. This made changes to the design easy and quick. The project was also supported by the formation of 'The San Alliance', a collaborative group consisting of MBMO Architects, Buildcorp (Head Contractor), Johnstaff (Project Manager), and the Sydney Adventist Hospital Executive Board.
Operational Impact
Quantitative Benefit
Related Case Studies.
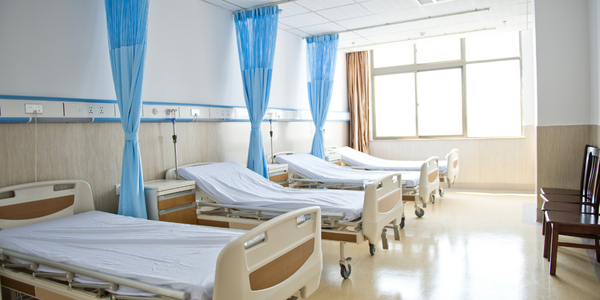
Case Study
Hospital Inventory Management
The hospital supply chain team is responsible for ensuring that the right medical supplies are readily available to clinicians when and where needed, and to do so in the most efficient manner possible. However, many of the systems and processes in use at the cancer center for supply chain management were not best suited to support these goals. Barcoding technology, a commonly used method for inventory management of medical supplies, is labor intensive, time consuming, does not provide real-time visibility into inventory levels and can be prone to error. Consequently, the lack of accurate and real-time visibility into inventory levels across multiple supply rooms in multiple hospital facilities creates additional inefficiency in the system causing over-ordering, hoarding, and wasted supplies. Other sources of waste and cost were also identified as candidates for improvement. Existing systems and processes did not provide adequate security for high-cost inventory within the hospital, which was another driver of cost. A lack of visibility into expiration dates for supplies resulted in supplies being wasted due to past expiry dates. Storage of supplies was also a key consideration given the location of the cancer center’s facilities in a dense urban setting, where space is always at a premium. In order to address the challenges outlined above, the hospital sought a solution that would provide real-time inventory information with high levels of accuracy, reduce the level of manual effort required and enable data driven decision making to ensure that the right supplies were readily available to clinicians in the right location at the right time.
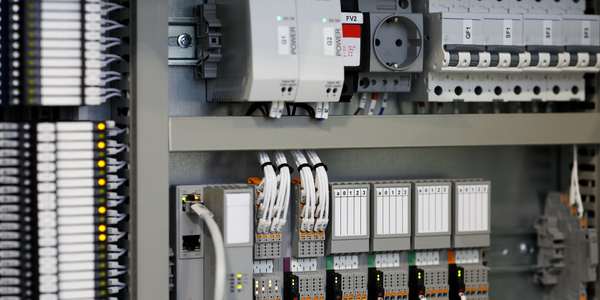
Case Study
Improving Production Line Efficiency with Ethernet Micro RTU Controller
Moxa was asked to provide a connectivity solution for one of the world's leading cosmetics companies. This multinational corporation, with retail presence in 130 countries, 23 global braches, and over 66,000 employees, sought to improve the efficiency of their production process by migrating from manual monitoring to an automatic productivity monitoring system. The production line was being monitored by ABB Real-TPI, a factory information system that offers data collection and analysis to improve plant efficiency. Due to software limitations, the customer needed an OPC server and a corresponding I/O solution to collect data from additional sensor devices for the Real-TPI system. The goal is to enable the factory information system to more thoroughly collect data from every corner of the production line. This will improve its ability to measure Overall Equipment Effectiveness (OEE) and translate into increased production efficiencies. System Requirements • Instant status updates while still consuming minimal bandwidth to relieve strain on limited factory networks • Interoperable with ABB Real-TPI • Small form factor appropriate for deployment where space is scarce • Remote software management and configuration to simplify operations
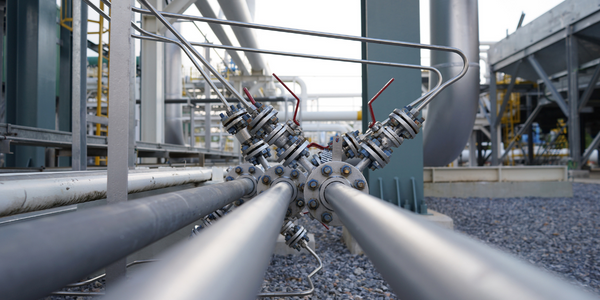
Case Study
Gas Pipeline Monitoring System for Hospitals
This system integrator focuses on providing centralized gas pipeline monitoring systems for hospitals. The service they provide makes it possible for hospitals to reduce both maintenance and labor costs. Since hospitals may not have an existing network suitable for this type of system, GPRS communication provides an easy and ready-to-use solution for remote, distributed monitoring systems System Requirements - GPRS communication - Seamless connection with SCADA software - Simple, front-end control capability - Expandable I/O channels - Combine AI, DI, and DO channels
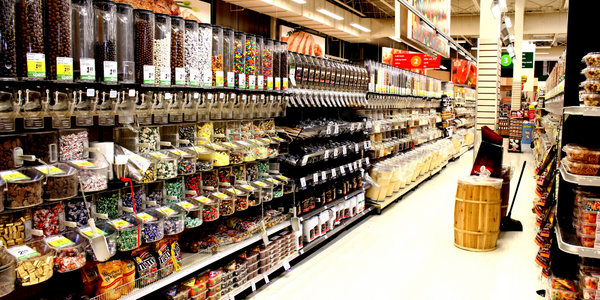
Case Study
How Sirqul’s IoT Platform is Crafting Carrefour’s New In-Store Experiences
Carrefour Taiwan’s goal is to be completely digital by end of 2018. Out-dated manual methods for analysis and assumptions limited Carrefour’s ability to change the customer experience and were void of real-time decision-making capabilities. Rather than relying solely on sales data, assumptions, and disparate systems, Carrefour Taiwan’s CEO led an initiative to find a connected IoT solution that could give the team the ability to make real-time changes and more informed decisions. Prior to implementing, Carrefour struggled to address their conversion rates and did not have the proper insights into the customer decision-making process nor how to make an immediate impact without losing customer confidence.