Download PDF
Customer Spotlight
Technology Category
- Functional Applications - Enterprise Resource Planning Systems (ERP)
- Functional Applications - Computerized Maintenance Management Systems (CMMS)
Applicable Functions
- Business Operation
- Quality Assurance
Use Cases
- Inventory Management
- Predictive Maintenance
- Process Control & Optimization
Services
- System Integration
- Software Design & Engineering Services
The Challenge
PD Peterka & Associates operates four distinct businesses under one roof, each with unique operational challenges and customer requirements. The company was using an outdated, homegrown system along with four other database and accounting applications that couldn't be integrated. This setup required each profit center to be managed separately, leading to inefficiencies. The primary challenges included managing materials flow, resourcing raw materials for short runs, ensuring on-time delivery, and maintaining quality at a competitive price. The company needed a single ERP solution that could handle the diverse needs of all four businesses, including robust Material Requirements Planning (MRP) capabilities and tight inventory control.
About The Customer
PD Peterka & Associates is a versatile manufacturer based in Saukville, Wisconsin. The company operates four unique businesses or 'profit centers' under a single roof: a job-shop, a complex railroad fastener manufacturing business, a die-cutting business, and a subcontracting business. Each of these businesses has its own set of operational challenges and customer requirements. The company was managing these diverse operations with an antiquated, homegrown Lotus-based system and four other database and accounting applications, none of which could be integrated. This setup required each profit center to be managed separately, leading to inefficiencies and a lack of integration across the organization.
The Solution
PD Peterka & Associates implemented OmegaCube’s PowerERP, a flexible, fully integrated ERP solution designed for small and midsize businesses. PowerERP was chosen for its ability to meet the diverse needs of all four businesses economically. The system provides robust scheduling capabilities, immediate visibility into machine utilization, and available capacity, enabling the company to evaluate alternative production scenarios. PowerERP's MRP functionality offers unprecedented control over inventory, scheduling, and complex BOMs, helping the company balance, plan, and schedule ordering and inventory movements. The system also tracks costs and bottlenecks in the production process, including machine downtime and inefficiencies. PowerERP instills process discipline across the organization, enhancing product quality and increasing sales. The system traces each job from the initial quotation through the manufacturing cycle, into the warehouse, out the door, and into the billing process. It also provides distinct reports for each profit center, allowing the company president to view individual performance or compile them into a single report.
Operational Impact
Quantitative Benefit
Related Case Studies.
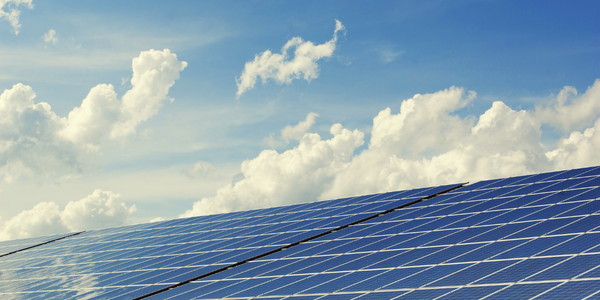
Case Study
Remote Monitoring & Predictive Maintenance App for a Solar Energy System
The maintenance & tracking of various modules was an overhead for the customer due to the huge labor costs involved. Being an advanced solar solutions provider, they wanted to ensure early detection of issues and provide the best-in-class customer experience. Hence they wanted to automate the whole process.
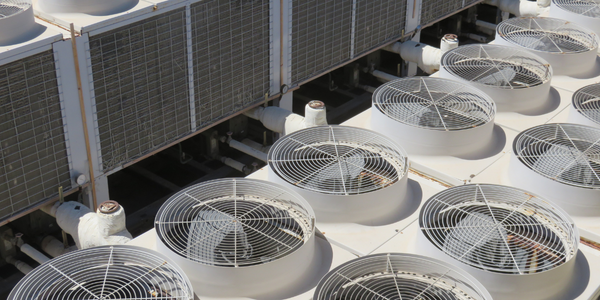
Case Study
Predictive Maintenance for Industrial Chillers
For global leaders in the industrial chiller manufacturing, reliability of the entire production process is of the utmost importance. Chillers are refrigeration systems that produce ice water to provide cooling for a process or industrial application. One of those leaders sought a way to respond to asset performance issues, even before they occur. The intelligence to guarantee maximum reliability of cooling devices is embedded (pre-alarming). A pre-alarming phase means that the cooling device still works, but symptoms may appear, telling manufacturers that a failure is likely to occur in the near future. Chillers who are not internet connected at that moment, provide little insight in this pre-alarming phase.
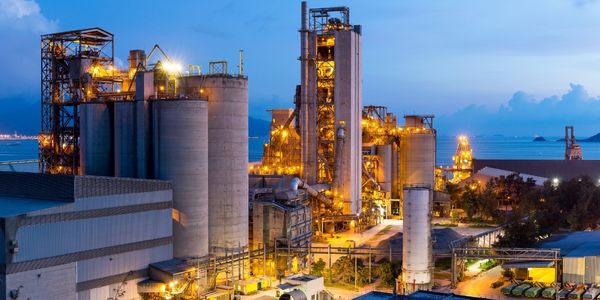
Case Study
System 800xA at Indian Cement Plants
Chettinad Cement recognized that further efficiencies could be achieved in its cement manufacturing process. It looked to investing in comprehensive operational and control technologies to manage and derive productivity and energy efficiency gains from the assets on Line 2, their second plant in India.
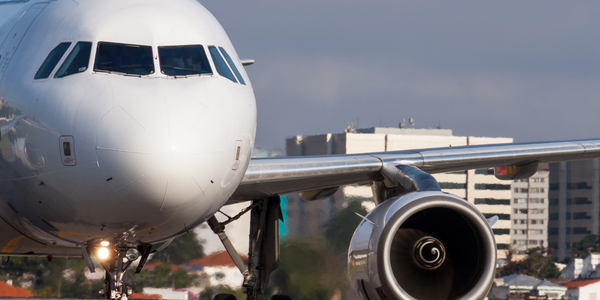
Case Study
Airbus Soars with Wearable Technology
Building an Airbus aircraft involves complex manufacturing processes consisting of thousands of moving parts. Speed and accuracy are critical to business and competitive advantage. Improvements in both would have high impact on Airbus’ bottom line. Airbus wanted to help operators reduce the complexity of assembling cabin seats and decrease the time required to complete this task.
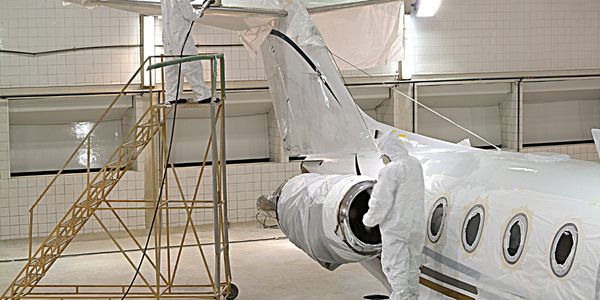
Case Study
Aircraft Predictive Maintenance and Workflow Optimization
First, aircraft manufacturer have trouble monitoring the health of aircraft systems with health prognostics and deliver predictive maintenance insights. Second, aircraft manufacturer wants a solution that can provide an in-context advisory and align job assignments to match technician experience and expertise.