Download PDF
Dana's Adoption of Altair’s SimLab for Automated Meshing of Powertrain Models
Technology Category
- Analytics & Modeling - Digital Twin / Simulation
- Functional Applications - Manufacturing Execution Systems (MES)
Applicable Industries
- Automotive
Applicable Functions
- Facility Management
- Product Research & Development
Use Cases
- Manufacturing Process Simulation
- Virtual Prototyping & Product Testing
Services
- Testing & Certification
- Training
The Challenge
Dana Holding Corporation, a global leader in driveline, sealing, and thermal management technologies, faced a significant challenge in their product development process. The traditional method of transforming CAD designs into prototypes, analyzing the prototype for failure points, redesigning the prototype, and retesting until the product met specifications was proving to be time-consuming and costly. Particularly, the pre-processing for models of cylinder heads and engine blocks required the geometry to be imported from CAD and then cleaned up by engineers, a task that could take anywhere from one to four days. To speed up the design cycle, Dana decided to implement a 'first-time-right' design methodology, where analysis would be conducted before building a prototype. This new process demanded a faster way to pre-process simulation models.
About The Customer
Dana Holding Corporation is a world leader in driveline, sealing, and thermal management technologies that enhance fuel efficiency, reduce emissions, and lower the cost of ownership in passenger, commercial, and off-highway vehicles. With a workforce of 25,000 employees, Dana operates in 27 countries within a network of approximately 90 engineering, manufacturing, and distribution facilities. Computer simulation of powertrain components, involving the creation of very large models with 25,000 surfaces or more, has been a crucial aspect of Dana’s product development process.
The Solution
Dana adopted Altair’s SimLab, a tool that automates many of the pre-processing steps, to address their challenge. SimLab imports the native geometry from the CAD systems, carries out meshing, creates surface and node sets, and creates contact pairs, all with minimal user intervention. Altair worked closely with Dana to integrate SimLab into its processes, demonstrating how SimLab could reduce Dana’s modeling time and providing training for Dana to try out SimLab’s features. Altair also helped Dana create templates, a defined group of settings that Dana engineers could use for all the engine models and other components. This ensured that every engineer who did the meshing with these templates would obtain a similar mesh with the same attributes. Dana found SimLab to be user-friendly, highly flexible, and offering valuable post-processing capabilities.
Operational Impact
Quantitative Benefit
Related Case Studies.
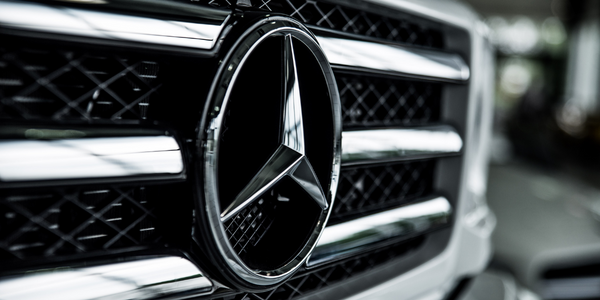
Case Study
Integral Plant Maintenance
Mercedes-Benz and his partner GAZ chose Siemens to be its maintenance partner at a new engine plant in Yaroslavl, Russia. The new plant offers a capacity to manufacture diesel engines for the Russian market, for locally produced Sprinter Classic. In addition to engines for the local market, the Yaroslavl plant will also produce spare parts. Mercedes-Benz Russia and his partner needed a service partner in order to ensure the operation of these lines in a maintenance partnership arrangement. The challenges included coordinating the entire maintenance management operation, in particular inspections, corrective and predictive maintenance activities, and the optimizing spare parts management. Siemens developed a customized maintenance solution that includes all electronic and mechanical maintenance activities (Integral Plant Maintenance).
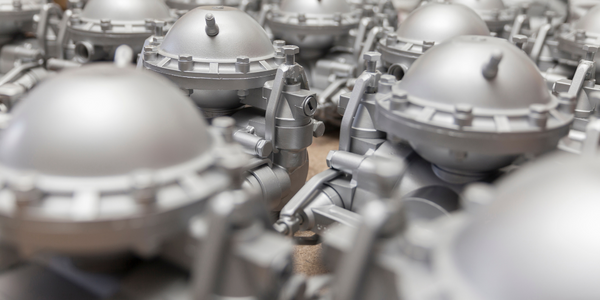
Case Study
Monitoring of Pressure Pumps in Automotive Industry
A large German/American producer of auto parts uses high-pressure pumps to deburr machined parts as a part of its production and quality check process. They decided to monitor these pumps to make sure they work properly and that they can see any indications leading to a potential failure before it affects their process.