Download PDF
Developing a Customized IoT Solution to Reduce Pre-processing Activities in Consumer Goods Industry
Technology Category
- Analytics & Modeling - Digital Twin / Simulation
- Cybersecurity & Privacy - Identity & Authentication Management
Applicable Industries
- Consumer Goods
- Packaging
Applicable Functions
- Procurement
- Product Research & Development
Use Cases
- Mesh Networks
- Time Sensitive Networking
Services
- Testing & Certification
The Challenge
Mabe, a Mexico-based company that designs, produces, and distributes appliances globally, was facing a significant challenge in its product development process. The company conducts various analysis studies on its products, including refrigerators, washing machines, and dryers, to improve their performance and quality. A critical part of these studies is the Refrigerator Door Foam Modeling (RDFM) process, which involves modeling the foam within the refrigerator that helps maintain the internal temperature and absorb shock during a drop situation. However, due to the complexity and time-consuming nature of this process, it was often overlooked or skipped entirely. This led to two major issues: the computer-aided engineering (CAE) results were not matching the actual results 100%, and the energy usage was not being measured appropriately. Mabe wanted to perform RDFM more routinely but needed a more efficient way forward.
About The Customer
Mabe is a Mexico-based company that designs, produces, and distributes appliances to more than 70 countries around the world. The company is focused on improving the performance and quality of their products, and conducts various analysis studies on its products, including refrigerators, washing machines, and dryers. Mabe operates in a fast-paced and highly competitive consumer goods industry, where the demand for “smarter” products is high and the timeline for production is shrinking. To remain competitive, Mabe must innovate and develop new products quickly.
The Solution
To address this challenge, Mabe collaborated with Altair ProductDesign, with whom they had a longstanding relationship. Altair ProductDesign proposed a highly customized solution based on its Impact Simulation Director. This solution would take the finite element (FE) models of the interior and exterior door components and fill the void automatically before taking the faces that contact the foam and extending those elements to fill the void. The process flow developed by the Altair ProductDesign team started with freezing the advanced geometry assembly of the refrigerator and cleaning the surfaces of the mesh. They used the Identification Parallel Gap function to create a solid joint in the gap areas, then started looking at the foam development and how it would interact with the doors and internal cabinets by creating a two-dimensional mesh. Once the areas where the foam would contact the doors were clearly identified, they could perform FE meshing of the product, the RDFM meshing, and the three-dimensional component meshing of the internal plastic and external steel, with the surfaces extended to minimize the void.
Operational Impact
Quantitative Benefit
Related Case Studies.
.png)
Case Study
Improving Vending Machine Profitability with the Internet of Things (IoT)
The vending industry is undergoing a sea change, taking advantage of new technologies to go beyond just delivering snacks to creating a new retail location. Intelligent vending machines can be found in many public locations as well as company facilities, selling different types of goods and services, including even computer accessories, gold bars, tickets, and office supplies. With increasing sophistication, they may also provide time- and location-based data pertaining to sales, inventory, and customer preferences. But at the end of the day, vending machine operators know greater profitability is driven by higher sales and lower operating costs.
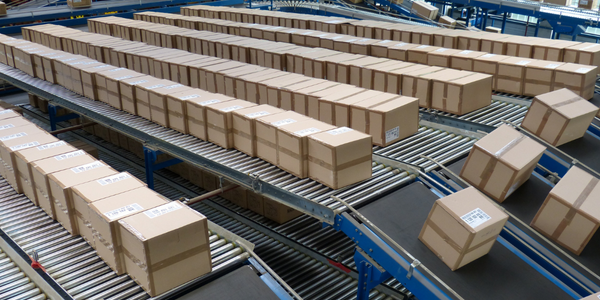
Case Study
IoT Data Analytics Case Study - Packaging Films Manufacturer
The company manufactures packaging films on made to order or configure to order basis. Every order has a different set of requirements from the product characteristics perspective and hence requires machine’s settings to be adjusted accordingly. If the film quality does not meet the required standards, the degraded quality impacts customer delivery causes customer dissatisfaction and results in lower margins. The biggest challenge was to identify the real root cause and devise a remedy for that.
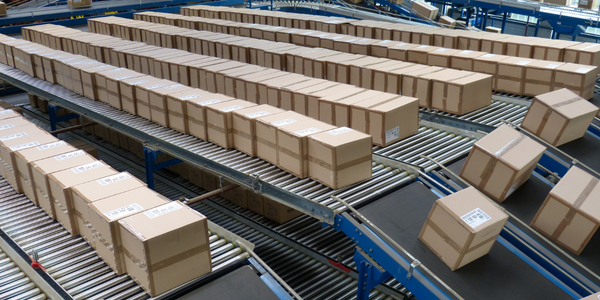
Case Study
Zenon the Ideal Basis for An Ergonomic HMI
KHS develops and produces machines and equipment for filling and packaging in the drinks industry. Because drinks manufacturing, filling and packaging consist of a number of highly complex processes, the user-friendly and intuitive operation of equipment is increasingly gaining in significance. In order to design these processes as simple as possible for the user, KHS decided to introduce a uniform, transparent and standardized solution to the company. The HMI interface should meet the requirement for people with different qualifications and enable them to work on a standard platform.
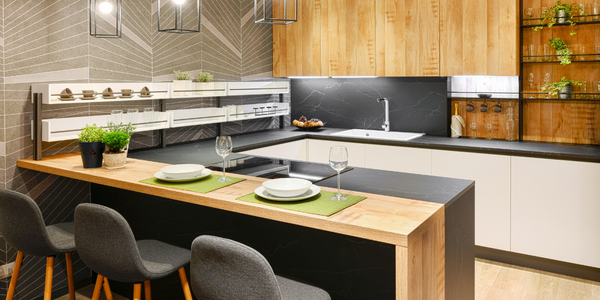
Case Study
Series Production with Lot-size-1 Flexibility
Nobilia manufactures customized fitted kitchens with a lot size of 1. They require maximum transparency of tracking design data and individual processing steps so that they can locate a particular piece of kitchen furniture in the sequence of processes.