Download PDF
Digitizing Processes with Dozuki Saves Thousands Per Hour for Leading Equipment Manufacturer
Technology Category
- Functional Applications - Manufacturing Execution Systems (MES)
- Sensors - Gas Sensors
Applicable Industries
- Equipment & Machinery
- Mining
Applicable Functions
- Facility Management
- Maintenance
Use Cases
- Time Sensitive Networking
- Virtual Training
Services
- System Integration
- Training
The Challenge
For nearly a century, a leading manufacturer of construction and mining equipment, diesel and natural gas engines, industrial gas turbines, and diesel-electric locomotives has been striving to digitize and standardize its processes to minimize waste and control machine setups and changeovers. However, the company faced significant challenges in achieving this goal. The existing documentation was limited, making it difficult for frontline workers to share feedback to improve operations. The company was using Excel to create and store process information, which often contained over fifty pages of information that workers had to read and retain. This method also lacked the ability to gather and implement frontline feedback, leading to missed opportunities for operational improvements. The company also faced inconsistencies in production, competency gaps among employees due to job shadowing as a primary training method, and safety concerns. The introduction of new automation technology also posed a challenge as the company needed to ensure that standards were properly distributed to frontline operators.
About The Customer
The customer is a leading manufacturer of construction and mining equipment, diesel and natural gas engines, industrial gas turbines, and diesel-electric locomotives. With a history spanning almost 100 years, the company has established a strong presence in the equipment manufacturing space. Through its subsidiaries and dealers, the company markets and sells its products worldwide. The company was seeking to digitize and standardize its processes to minimize waste and control machine setups and changeovers. However, it faced challenges in achieving this goal due to limited existing documentation, difficulties in gathering and implementing frontline feedback, inconsistencies in production, competency gaps among employees, and safety concerns.
The Solution
The company turned to Dozuki to address these challenges. Dozuki was initially piloted at one facility, and after seeing positive results, it was rolled out at other facilities. Dozuki allowed the company to rapidly create, digitize, and deploy standards in a format that all employees could easily understand. It also addressed the issue of unrestricted access to documentation, which had previously led to duplication, accidental deletion, and extra document handling. With Dozuki, operators could access content directly from the floor with a QR code scan, even in the extreme environment of the forge. This ensured that the right content was always in front of the operators, reducing mistakes and quality issues. Dozuki also provided a purpose-built document control system that allowed operations stakeholders to see the full list of process documentation that needed approval, enabling them to quickly update content and instantly distribute it to frontline operators. It also included a built-in audit trail to track all changes.
Operational Impact
Quantitative Benefit
Related Case Studies.
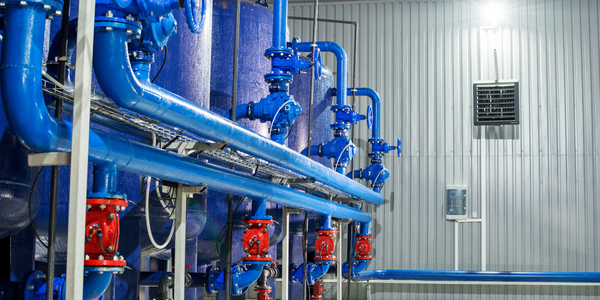
Case Study
Smart Water Filtration Systems
Before working with Ayla Networks, Ozner was already using cloud connectivity to identify and solve water-filtration system malfunctions as well as to monitor filter cartridges for replacements.But, in June 2015, Ozner executives talked with Ayla about how the company might further improve its water systems with IoT technology. They liked what they heard from Ayla, but the executives needed to be sure that Ayla’s Agile IoT Platform provided the security and reliability Ozner required.
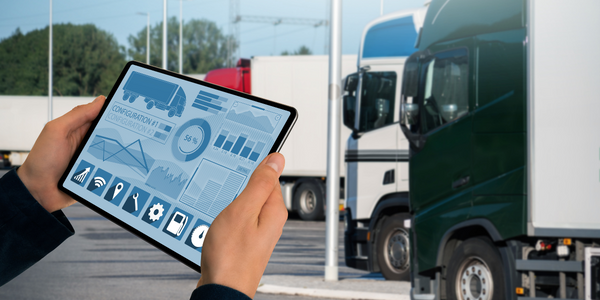
Case Study
IoT enabled Fleet Management with MindSphere
In view of growing competition, Gämmerler had a strong need to remain competitive via process optimization, reliability and gentle handling of printed products, even at highest press speeds. In addition, a digitalization initiative also included developing a key differentiation via data-driven services offers.
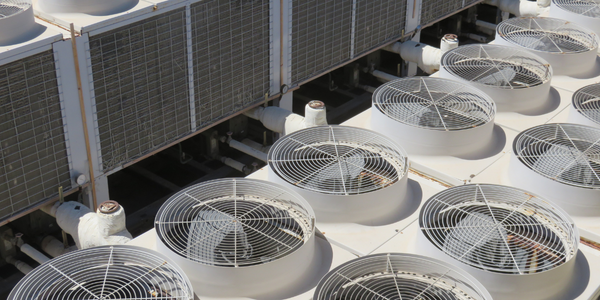
Case Study
Predictive Maintenance for Industrial Chillers
For global leaders in the industrial chiller manufacturing, reliability of the entire production process is of the utmost importance. Chillers are refrigeration systems that produce ice water to provide cooling for a process or industrial application. One of those leaders sought a way to respond to asset performance issues, even before they occur. The intelligence to guarantee maximum reliability of cooling devices is embedded (pre-alarming). A pre-alarming phase means that the cooling device still works, but symptoms may appear, telling manufacturers that a failure is likely to occur in the near future. Chillers who are not internet connected at that moment, provide little insight in this pre-alarming phase.
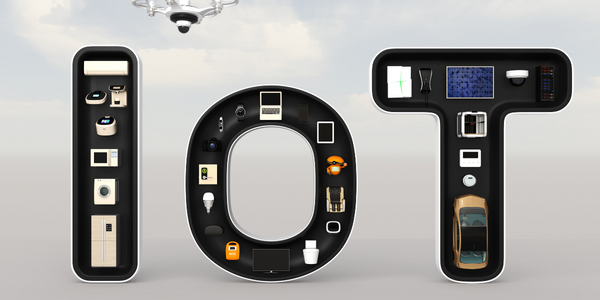
Case Study
Premium Appliance Producer Innovates with Internet of Everything
Sub-Zero faced the largest product launch in the company’s history:It wanted to launch 60 new products as scheduled while simultaneously opening a new “greenfield” production facility, yet still adhering to stringent quality requirements and manage issues from new supply-chain partners. A the same time, it wanted to increase staff productivity time and collaboration while reducing travel and costs.
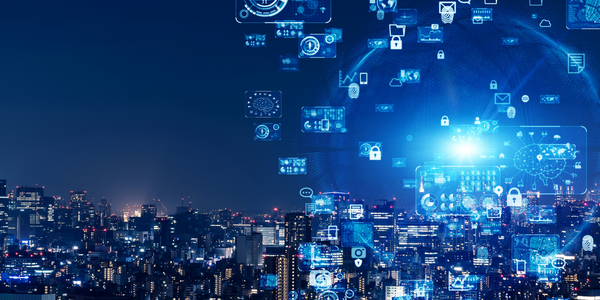
Case Study
Integration of PLC with IoT for Bosch Rexroth
The application arises from the need to monitor and anticipate the problems of one or more machines managed by a PLC. These problems, often resulting from the accumulation over time of small discrepancies, require, when they occur, ex post technical operations maintenance.
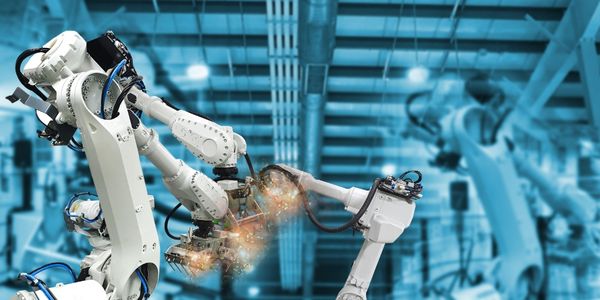
Case Study
Robot Saves Money and Time for US Custom Molding Company
Injection Technology (Itech) is a custom molder for a variety of clients that require precision plastic parts for such products as electric meter covers, dental appliance cases and spools. With 95 employees operating 23 molding machines in a 30,000 square foot plant, Itech wanted to reduce man hours and increase efficiency.