Download PDF
Ductile Fracture Modeling of High-Strength Galvanized Steels at Borçelik with Altair
Technology Category
- Analytics & Modeling - Machine Learning
- Robots - Autonomous Guided Vehicles (AGV)
Applicable Industries
- Automotive
- Metals
Applicable Functions
- Product Research & Development
Use Cases
- Time Sensitive Networking
- Vehicle Performance Monitoring
Services
- Testing & Certification
The Challenge
Borçelik, a leading galvanized steel producer in Turkey, was faced with the challenge of reducing emissions and fuel consumption in the automotive industry. This required the development of advanced materials and production processes. Fuel efficiency in vehicles largely depends on the successful design of the vehicle body structure and the development of technologies that can reduce its weight. However, while reducing the weight of the vehicle structure, it was crucial to maintain passenger safety. The main focus of this study was to investigate the ductile fracture behavior of the high-strength galvanized flat steel that forms the vehicle body structure.
About The Customer
Borçelik is a leading galvanized steel producer in Turkey, established in the early 1990s. The company operates as a partnership of Borusan Holding and ArcelorMittal, one of the world’s leading integrated steel and mining companies. Borçelik is engaged in manufacturing hot dip galvanized steel, cold-rolled steel, and hot-rolled (pickled and oiled) steel groups, all of which are industrial raw material inputs. The company offers a wide range of products, meeting manufacturer needs in industries like household appliances, automotive (OEM and Tier 1/2), panel radiators, construction, color coating, pipe and profile, packaging, metal goods, and steel service centers. Borçelik has a total production capacity of 1.5 million tons under the Borçelik brand and a metal processing capacity of 500 thousand tons under the Kerim Çelik brand.
The Solution
Borçelik utilized Altair® Radioss™ to perform in-depth simulations and fatigue analyses of designs. This software capitalizes on machine learning and optimization techniques. With this structural analysis software, users can predict part behavior under various loads. The data derived from experimental tests can be applied to numerical calculations using different fracture models relating variables like stress triaxiality, lode angle, or equivalent plastic strain to material fracture. The /FAIL/BIQUAD failure model was particularly useful as it provided fast and accurate results. Users could create a fracture locus for materials with data from material libraries using only tensile test results. A Hosford-Coulomb ductile material fracture could be modeled with the /FAIL/EMC failure criterion, which supports 3D elements, especially for detailed fracture modeling. The Johnson-Cook fracture criterion, widely used in the industry, could be used in numerical calculations using the /FAIL/JOHNSON failure card. The /FAIL/FLD failure model could be employed to define the forming limit diagram (FLD), which represents the formability of the material, especially in sheet metal forming analysis.
Operational Impact
Quantitative Benefit
Related Case Studies.
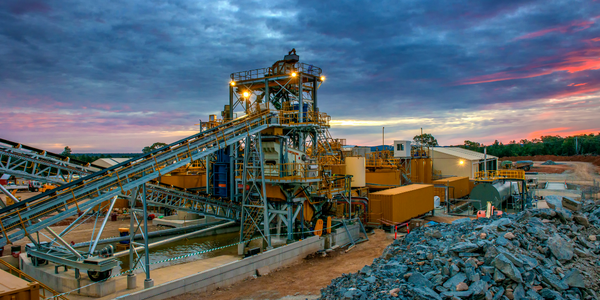
Case Study
Goldcorp: Internet of Things Enables the Mine of the Future
Goldcorp is committed to responsible mining practices and maintaining maximum safety for its workers. At the same time, the firm is constantly exploring ways to improve the efficiency of its operations, extend the life of its assets, and control costs. Goldcorp needed technology that can maximize production efficiency by tracking all mining operations, keep employees safe with remote operations and monitoring of hazardous work areas and control production costs through better asset and site management.
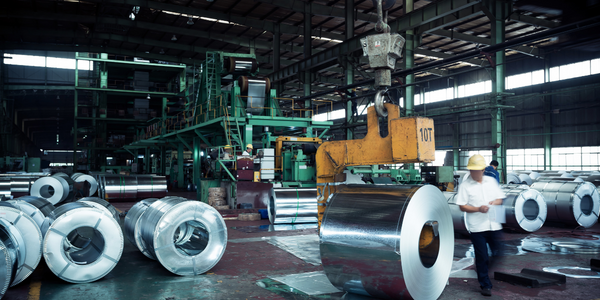
Case Study
KSP Steel Decentralized Control Room
While on-site in Pavlodar, Kazakhstan, the DAQRI team of Business Development and Solutions Architecture personnel worked closely with KSP Steel’s production leadership to understand the steel production process, operational challenges, and worker pain points.
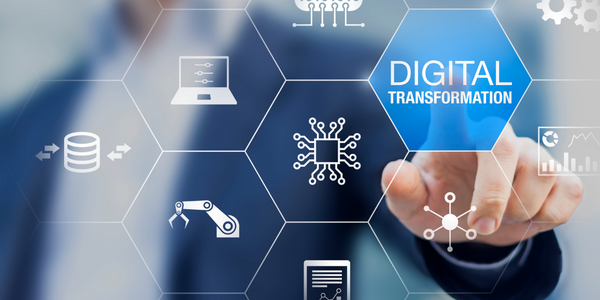
Case Study
Bluescope Steel on Path to Digitally Transform Operations and IT
Increasing competition and fluctuations in the construction market prompted BlueScope Steel to look toward digital transformation of its four businesses, including modern core applications and IT infrastructure. BlueScope needed to modernize its infrastructure and adopt new technologies to improve operations and supply chain efficiency while maintaining and updating an aging application portfolio.
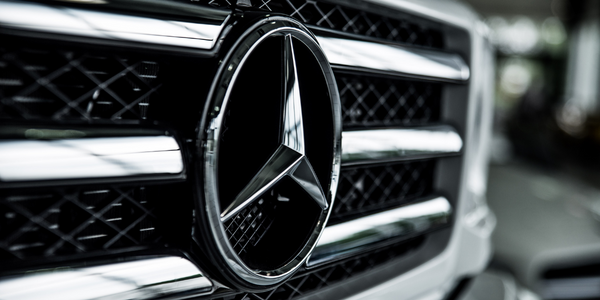
Case Study
Integral Plant Maintenance
Mercedes-Benz and his partner GAZ chose Siemens to be its maintenance partner at a new engine plant in Yaroslavl, Russia. The new plant offers a capacity to manufacture diesel engines for the Russian market, for locally produced Sprinter Classic. In addition to engines for the local market, the Yaroslavl plant will also produce spare parts. Mercedes-Benz Russia and his partner needed a service partner in order to ensure the operation of these lines in a maintenance partnership arrangement. The challenges included coordinating the entire maintenance management operation, in particular inspections, corrective and predictive maintenance activities, and the optimizing spare parts management. Siemens developed a customized maintenance solution that includes all electronic and mechanical maintenance activities (Integral Plant Maintenance).
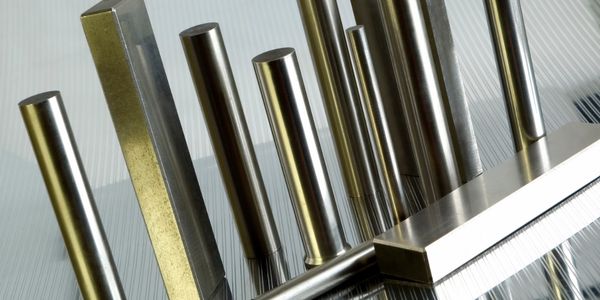
Case Study
RobotStudio Case Study: Benteler Automobiltechnik
Benteler has a small pipe business area for which they produce fuel lines and coolant lines made of aluminum for Porsche and other car manufacturers. One of the problems in production was that when Benteler added new products, production had too much downtime.