Download PDF
E.T. Browne Drug Co. Achieves 5005% ROI with Nintex and Equilibrium Workflow Automation
Applicable Industries
- Packaging
- Pharmaceuticals
Applicable Functions
- Sales & Marketing
Use Cases
- Intelligent Packaging
- Time Sensitive Networking
The Challenge
E.T. Browne Drug Co., a leading manufacturer of treatment-oriented beauty products, faced a significant challenge in its label and packaging process. The company continually designs and redesigns its labels and packaging for new products, new formulations of existing products, and to meet new regulatory requirements in the 100 countries it operates in. This process involves multiple departments, including research and development, marketing, legal and compliance, and manufacturing. The review and approval process was manual, leading to delays and lack of visibility into the status of ongoing reviews. Documents could sit on a manager’s desk for days or weeks, delaying time to market. There were constant issues around whether someone had the correct version for review and no reminders to perform tasks. As the company started to automate the workflow, another issue emerged. The company was routing visual data and content, including the size, shape, color, and positioning of label and packaging materials. However, the Adobe Illustrator files in which that content was created weren’t supported by SharePoint, and the pre-rendering into PDFs lacked the precision needed for meaningful approvals.
About The Customer
E.T. Browne Drug Co. is a 180-year-old family business that prides itself as a leader in treatment-oriented beauty products. Its most popular product is Palmer’s Cocoa Butter, which is sold worldwide and is the #1 cocoa butter brand in the US. The company continually designs and redesigns its labels and packaging for new products and for new formulations of existing products, as well as to meet new regulatory requirements in each of the 100 countries in which it does business. The review and approval process for this content involves departments throughout the company, including research and development, marketing, legal and compliance, and manufacturing.
The Solution
E.T. Browne addressed these challenges by implementing an automated workflow solution based on Nintex Workflow and Nintex Forms, leveraging Equilibrium’s MediaRich® OneViewer™ technology. This solution supports over 450 file types and creates a secure universal viewing experience automatically inside of SharePoint. It enables all approvers to view the exact images in the AI files from a single source, directly from notification emails, at their desks or on their mobile devices – anywhere —and without the need for plug-ins, downloads or special applications such as Acrobat or Adobe Illustrator. The solution also allows for the implementation of multiple reviews simultaneously, sending reminders, and implementing “smart approvals” that automatically approve a review and move it to the next step after a specified number of days. This significantly sped up the approval process.
Operational Impact
Quantitative Benefit
Related Case Studies.
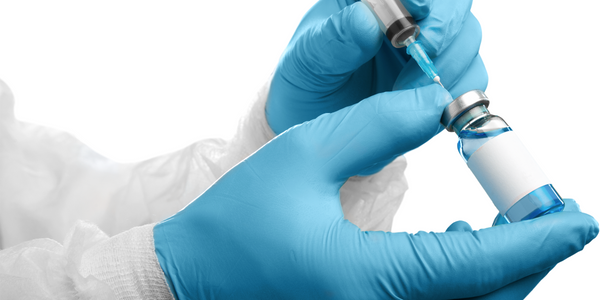
Case Study
Case Study: Pfizer
Pfizer’s high-performance computing software and systems for worldwide research and development support large-scale data analysis, research projects, clinical analytics, and modeling. Pfizer’s computing services are used across the spectrum of research and development efforts, from the deep biological understanding of disease to the design of safe, efficacious therapeutic agents.
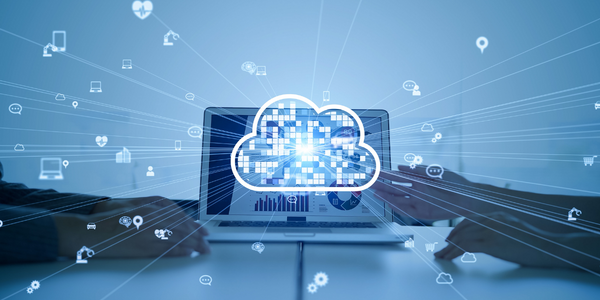
Case Study
Fusion Middleware Integration on Cloud for Pharma Major
Customer wanted a real-time, seamless, cloud based integration between the existing on premise and cloud based application using SOA technology on Oracle Fusion Middleware Platform, a Contingent Worker Solution to collect, track, manage and report information for on-boarding, maintenance and off-boarding of contingent workers using a streamlined and Integrated business process, and streamlining of integration to the back-end systems and multiple SaaS applications.
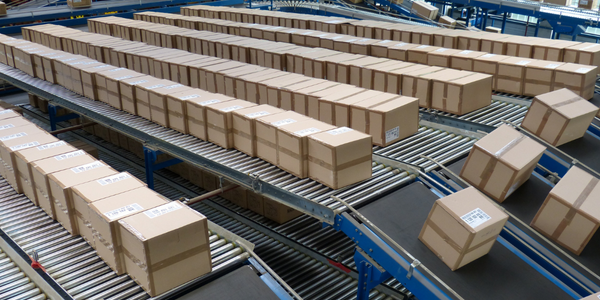
Case Study
IoT Data Analytics Case Study - Packaging Films Manufacturer
The company manufactures packaging films on made to order or configure to order basis. Every order has a different set of requirements from the product characteristics perspective and hence requires machine’s settings to be adjusted accordingly. If the film quality does not meet the required standards, the degraded quality impacts customer delivery causes customer dissatisfaction and results in lower margins. The biggest challenge was to identify the real root cause and devise a remedy for that.
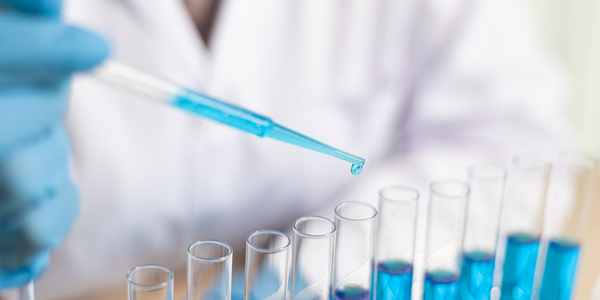
Case Study
Process Control System Support
In many automated production facilities, changes are made to SIMATIC PCS 7 projects on a daily basis, with individual processes often optimised by multiple workers due to shift changes. Documentation is key here, as this keeps workers informed about why a change was made. Furthermore, SIMATIC PCS 7 installations are generally used in locations where documentation is required for audits and certification. The ability to track changes between two software projects is not only an invaluable aid during shift changes, but also when searching for errors or optimising a PCS 7 installation. Every change made to the system is labour-intensive and time-consuming. Moreover, there is also the risk that errors may occur. If a change is saved in the project, then the old version is lost unless a backup copy was created in advance. If no backup was created, it will no longer be possible to return to the previous state if and when programming errors occur. Each backup denotes a version used by the SIMATIC PCS 7 system to operate an installation. To correctly interpret a version, information is required on WHO changed WHAT, WHERE, WHEN and WHY: - Who created the version/who is responsible for the version? - Who released the version? - What was changed in the version i.e. in which block or module of the SIMATIC PCS 7 installation were the changes made? - When was the version created? Is this the latest version or is there a more recent version? - Why were the changes made to the version? If they are part of a regular maintenance cycle, then is the aim to fix an error or to improve production processes? - Is this particular version also the version currently being used in production? The fact that SIMATIC PCS 7 projects use extremely large quantities of data complicates the situation even further, and it can take a long time to load and save information as a result. Without a sustainable strategy for operating a SIMATIC PCS 7 installation, searching for the right software version can become extremely time-consuming and the installation may run inefficiently as a result.
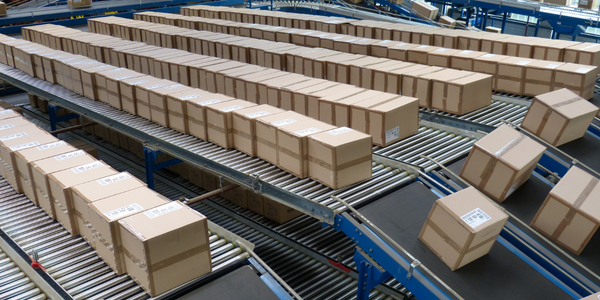
Case Study
Zenon the Ideal Basis for An Ergonomic HMI
KHS develops and produces machines and equipment for filling and packaging in the drinks industry. Because drinks manufacturing, filling and packaging consist of a number of highly complex processes, the user-friendly and intuitive operation of equipment is increasingly gaining in significance. In order to design these processes as simple as possible for the user, KHS decided to introduce a uniform, transparent and standardized solution to the company. The HMI interface should meet the requirement for people with different qualifications and enable them to work on a standard platform.