Download PDF
Efficiency Improvement in Engine Design Analysis at Ford Motor Company with ANSYS Meshing Solution
Technology Category
- Sensors - Temperature Sensors
Applicable Industries
- Automotive
Applicable Functions
- Product Research & Development
Use Cases
- Mesh Networks
The Challenge
The Engine NVH Analysis Section at Ford Motor Company is tasked with providing CAE NVH design analysis support to various programs. The types of analysis performed include engine component and assembly modal & vibrational response analysis, engine component and assembly radiated noise analysis, crank/block dynamic interaction analysis, air intake system NVH analysis, and exhaust manifold radiated noise analysis. However, with program timing being regularly compressed, the demand for quick turnaround on design analysis is constantly growing. As the finite element models become larger, they tend to drive the analysis time longer. This creates a need for quick FE models that accurately represent the structures, with the smallest number of degrees of freedom being an absolute necessity. The parts that need to be meshed can range from simple stampings to complex castings of cylinder heads, blocks, and manifolds, to even more complex multi-piece composite intake manifolds.
About The Customer
Ford Motor Company is a leading automotive company based in the United States of America. The Engine NVH Analysis Section at Ford is responsible for providing CAE NVH design analysis support to the Advanced, V-Engine Component, and Engine Systems programs. The section performs various types of analysis, including engine component and assembly modal & vibrational response analysis, engine component and assembly radiated noise analysis, crank/block dynamic interaction analysis, air intake system NVH analysis, and exhaust manifold radiated noise analysis. The section deals with a wide range of parts, from simple stampings to complex castings of cylinder heads, blocks, and manifolds, to even more complex multi-piece composite intake manifolds.
The Solution
To address the challenge, Ford Motor Company implemented the ANSYS AI*Environment tet meshing solution. This solution allows the company to create meshed models that meet their element size and quality criteria. Most of the model data is imported directly from I-DEAS, but some of the data comes from X-ray scans. The ANSYS AI*Environment solution offers several benefits. It eliminates the need for rework of geometry to get it to mesh, allows fitting the mesh to different areas in the same geometry without creating too many elements, and enables the import of different types of data that describe the part to be modeled. Furthermore, it allows the creation of all models in a matter of hours, not days.
Operational Impact
Quantitative Benefit
Related Case Studies.
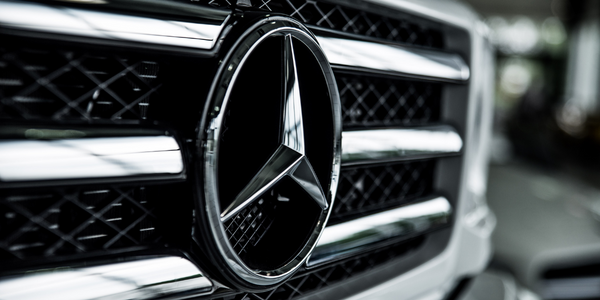
Case Study
Integral Plant Maintenance
Mercedes-Benz and his partner GAZ chose Siemens to be its maintenance partner at a new engine plant in Yaroslavl, Russia. The new plant offers a capacity to manufacture diesel engines for the Russian market, for locally produced Sprinter Classic. In addition to engines for the local market, the Yaroslavl plant will also produce spare parts. Mercedes-Benz Russia and his partner needed a service partner in order to ensure the operation of these lines in a maintenance partnership arrangement. The challenges included coordinating the entire maintenance management operation, in particular inspections, corrective and predictive maintenance activities, and the optimizing spare parts management. Siemens developed a customized maintenance solution that includes all electronic and mechanical maintenance activities (Integral Plant Maintenance).
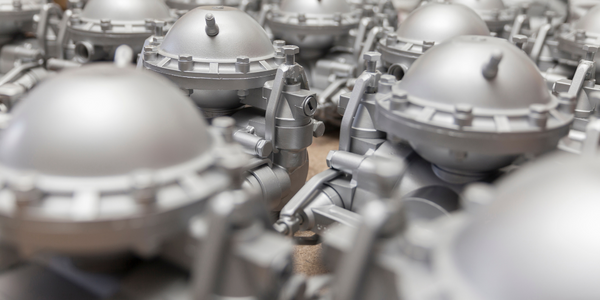
Case Study
Monitoring of Pressure Pumps in Automotive Industry
A large German/American producer of auto parts uses high-pressure pumps to deburr machined parts as a part of its production and quality check process. They decided to monitor these pumps to make sure they work properly and that they can see any indications leading to a potential failure before it affects their process.