Download PDF
Farm Bureau Insurance Improves Profitability With Better Business Intelligence
Technology Category
- Analytics & Modeling - Real Time Analytics
- Analytics & Modeling - Predictive Analytics
Applicable Functions
- Business Operation
Use Cases
- Predictive Maintenance
- Real-Time Location System (RTLS)
Services
- Data Science Services
The Challenge
Farm Bureau Insurance, a leading insurer in Tennessee, was faced with a significant challenge in 2011 when two devastating storms resulted in a year's worth of claims in just two months. The company's existing reporting processes were cumbersome and could not provide the real-time data, drill-down functionality, and ad hoc capabilities that managers required to effectively handle the situation. The company needed better access to data and improved reporting capabilities for a clearer view into its operational performance and financial metrics. The turmoil from these unexpected events became the driving force for Farm Bureau Insurance to gain a clearer view into its operational performance and financial metrics.
About The Customer
Farm Bureau Insurance is offered through the Tennessee Farmers Insurance Companies, a group of affiliated companies working together to provide insurance services to Tennesseans. It covers more homes and autos than any other insurer in Tennessee, and is the state’s second-largest writer of individual life policies. In April and May of 2011, two devastating storms left the company reeling as its personnel struggled under the deluge of a year’s worth of claims in just two months. Hampered by limited time and resources, financial managers scrambled to line up re-insurers while claims processors, already swamped with active claims from the April storm, saw claims from the May event come pouring in.
The Solution
Farm Bureau Insurance turned to WebFOCUS to replace an existing Crystal Reports framework with new reports and dashboards for on-demand reporting. The company rolled out new business intelligence (BI) capabilities throughout the company with advanced dashboards and reports for corporate management, claims statistics, claims audit, storm event notification, risk management, re-insurance, sales, project management, call center log, and others. The company also used WebFOCUS risk management dashboard that provides powerful analytics and easy-to-create reports based on a variety of criteria. The company also plans to use the WebFOCUS Web Services Adapter to pull in GPS data, weather data, maps, and other information that will help the company track and manage claims.
Operational Impact
Related Case Studies.
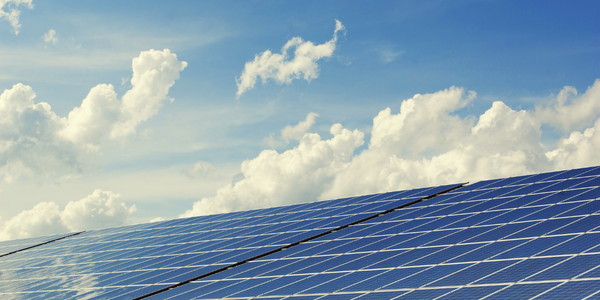
Case Study
Remote Monitoring & Predictive Maintenance App for a Solar Energy System
The maintenance & tracking of various modules was an overhead for the customer due to the huge labor costs involved. Being an advanced solar solutions provider, they wanted to ensure early detection of issues and provide the best-in-class customer experience. Hence they wanted to automate the whole process.
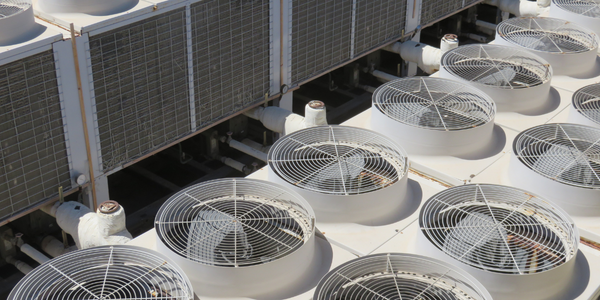
Case Study
Predictive Maintenance for Industrial Chillers
For global leaders in the industrial chiller manufacturing, reliability of the entire production process is of the utmost importance. Chillers are refrigeration systems that produce ice water to provide cooling for a process or industrial application. One of those leaders sought a way to respond to asset performance issues, even before they occur. The intelligence to guarantee maximum reliability of cooling devices is embedded (pre-alarming). A pre-alarming phase means that the cooling device still works, but symptoms may appear, telling manufacturers that a failure is likely to occur in the near future. Chillers who are not internet connected at that moment, provide little insight in this pre-alarming phase.
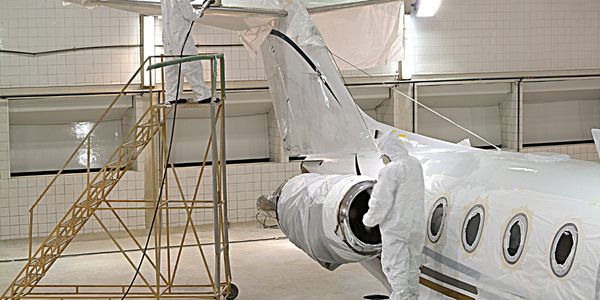
Case Study
Aircraft Predictive Maintenance and Workflow Optimization
First, aircraft manufacturer have trouble monitoring the health of aircraft systems with health prognostics and deliver predictive maintenance insights. Second, aircraft manufacturer wants a solution that can provide an in-context advisory and align job assignments to match technician experience and expertise.
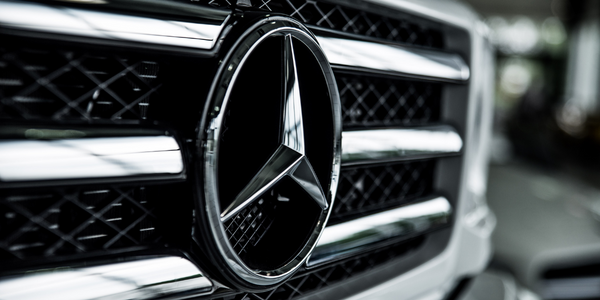
Case Study
Integral Plant Maintenance
Mercedes-Benz and his partner GAZ chose Siemens to be its maintenance partner at a new engine plant in Yaroslavl, Russia. The new plant offers a capacity to manufacture diesel engines for the Russian market, for locally produced Sprinter Classic. In addition to engines for the local market, the Yaroslavl plant will also produce spare parts. Mercedes-Benz Russia and his partner needed a service partner in order to ensure the operation of these lines in a maintenance partnership arrangement. The challenges included coordinating the entire maintenance management operation, in particular inspections, corrective and predictive maintenance activities, and the optimizing spare parts management. Siemens developed a customized maintenance solution that includes all electronic and mechanical maintenance activities (Integral Plant Maintenance).
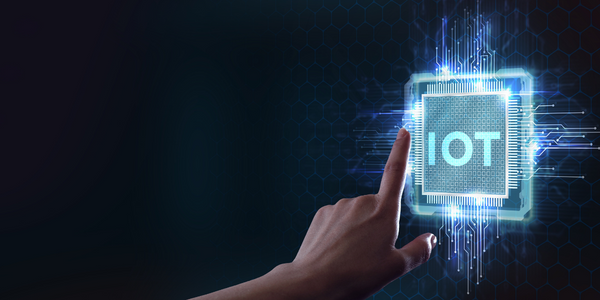
Case Study
Leading Tools Manufacturer Transforms Operations with IoT
Stanley Black & Decker required transparency of real-time overall equipment effectiveness and line productivity to reduce production line change over time.The goal was to to improve production to schedule, reduce actual labor costs and understanding the effects of shift changes and resource shifts from line to line.

Case Study
Asset Management and Predictive Maintenance
The customer prides itself on excellent engineering and customer centric philosophy, allowing its customer’s minds to be at ease and not worry about machine failure. They can easily deliver the excellent maintenance services to their customers, but there are some processes that can be automated to deliver less downtime for the customer and more efficient maintenance schedules.