Download PDF
Faster Self-Service Analytics with Salesforce
Technology Category
- Analytics & Modeling - Big Data Analytics
Applicable Industries
- Automotive
- Transportation
Applicable Functions
- Sales & Marketing
- Business Operation
Use Cases
- Predictive Maintenance
- Fleet Management
Services
- Data Science Services
- System Integration
The Challenge
Ryder System, Inc., a leading provider of fleet leasing and maintenance, dedicated transportation, and supply chain management solutions, was facing several analytic challenges. They had an in-house analytics team of over five people, but there was no centralized data source. The team heavily relied on IT, resulting in long lead times for project completion. They were using various CRM systems that collected product line information on customer transactions, contacts, prospects, and pipeline opportunities for analysis. However, blending Salesforce data with other data sources was labor-intensive and sapped analyst productivity. Incorporating advanced analytics and visualizations complicated the process even further.
About The Customer
Ryder System, Inc. is a leading provider of fleet leasing and maintenance, dedicated transportation, and supply chain management solutions. The company serves customers globally and is publicly traded on the NYSE under the symbol 'R'. It is a component of the Dow Jones Transportation Average and a Fortune 500 company. Founded in 1933, Ryder System, Inc. has an annual sales revenue of $6.5 billion as of 2015. The company has over 50,000 B2B customers and operates a fleet of more than 185,000 vehicles at over 700 locations.
The Solution
Ryder System, Inc. adopted Alteryx with Salesforce to overcome their analytic challenges. They used a trial license of Alteryx and web-based training to familiarize their team with the tool. Early successes in data blending were shared with the team, leading to a decision to initiate a full pilot with the entire analytics team. Alteryx helped the company to consolidate customer data from multiple CRMs, eliminate repetitive tasks performed in running reports, and merge spreadsheets. It also allowed the company to realize significant efficiencies where data from entire Salesforce objects can be queried. Production reports can now be run with the click of a button.
Operational Impact
Quantitative Benefit
Related Case Studies.
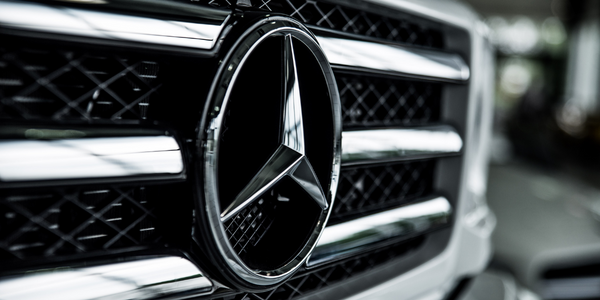
Case Study
Integral Plant Maintenance
Mercedes-Benz and his partner GAZ chose Siemens to be its maintenance partner at a new engine plant in Yaroslavl, Russia. The new plant offers a capacity to manufacture diesel engines for the Russian market, for locally produced Sprinter Classic. In addition to engines for the local market, the Yaroslavl plant will also produce spare parts. Mercedes-Benz Russia and his partner needed a service partner in order to ensure the operation of these lines in a maintenance partnership arrangement. The challenges included coordinating the entire maintenance management operation, in particular inspections, corrective and predictive maintenance activities, and the optimizing spare parts management. Siemens developed a customized maintenance solution that includes all electronic and mechanical maintenance activities (Integral Plant Maintenance).
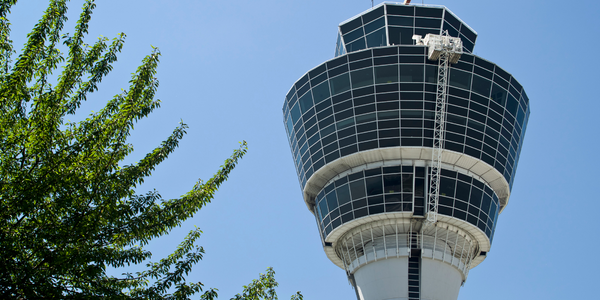
Case Study
Airport SCADA Systems Improve Service Levels
Modern airports are one of the busiest environments on Earth and rely on process automation equipment to ensure service operators achieve their KPIs. Increasingly airport SCADA systems are being used to control all aspects of the operation and associated facilities. This is because unplanned system downtime can cost dearly, both in terms of reduced revenues and the associated loss of customer satisfaction due to inevitable travel inconvenience and disruption.
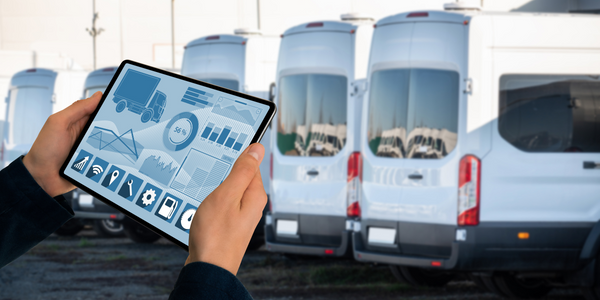
Case Study
IoT-based Fleet Intelligence Innovation
Speed to market is precious for DRVR, a rapidly growing start-up company. With a business model dependent on reliable mobile data, managers were spending their lives trying to negotiate data roaming deals with mobile network operators in different countries. And, even then, service quality was a constant concern.
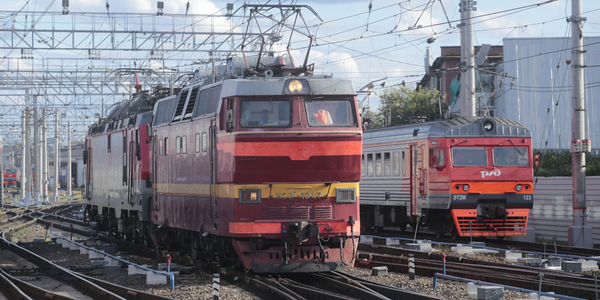
Case Study
Digitize Railway with Deutsche Bahn
To reduce maintenance costs and delay-causing failures for Deutsche Bahn. They need manual measurements by a position measurement system based on custom-made MEMS sensor clusters, which allow autonomous and continuous monitoring with wireless data transmission and long battery. They were looking for data pre-processing solution in the sensor and machine learning algorithms in the cloud so as to detect critical wear.