Download PDF
FGR Automation and Cumulocity IoT improve safety in the field
Technology Category
- Platform as a Service (PaaS) - Connectivity Platforms
- Analytics & Modeling - Real Time Analytics
Applicable Industries
- Mining
- Automotive
Applicable Functions
- Discrete Manufacturing
- Quality Assurance
Use Cases
- Remote Asset Management
- Predictive Maintenance
- Real-Time Location System (RTLS)
Services
- System Integration
- Data Science Services
The Challenge
The mining company was facing challenges in monitoring and collecting data from remote installations. The boreholes in the phosphate mine were located in a remote desert area with no utility-provided electricity or internet. Communications were limited to company satellite phones. If anything happened in one of the boreholes, it would take hours to get medical help or a crucial part. The ability to monitor and remotely supervise the boreholes was not just for compliance reasons, but also for safety. The company needed to collect and turn critical data into value. Another challenge was the pre-permitting process which required a lot of data to prove that the soil is stable enough for the operation.
About The Customer
FGR is an engineering firm established in 1985 that specializes in systems offering significant improvements in overall plant efficiency, control, and profitability with the total automation of manufacturing processes. FGR has developed and installed integrated control systems around the world for refineries, power, water & waste water, truck & train loading, and pharmaceutical product packaging, among many others. The company was brought in to solve the problem of collecting and turning critical data into value in a phosphate mine and dozens more.
The Solution
FGR designed, built and installed solar panels to provide a means of communicating data from the mine and sending it to the cloud for analysis. It then designed, built and installed sensors that could monitor and relay conditions in real time. FGR partnered with Cumulocity IoT to provide an IoT platform to capture the data, analyze it for patterns that signal problems and then send real-time alerts back to the field. The IoT solution allowed the soil measurements to be completed before the drilling took place, to reassure government officials that it is stable enough for a borehole operation. Using Cumulocity IoT, the data could be fed directly into government forms, making pre-permitting a much easier and quicker process. In other mines, FGR and Cumulocity IoT’s combined solution is used to monitor rock containment walls. By monitoring the walls for vibration or movement, potential accidents could be prevented.
Operational Impact
Related Case Studies.
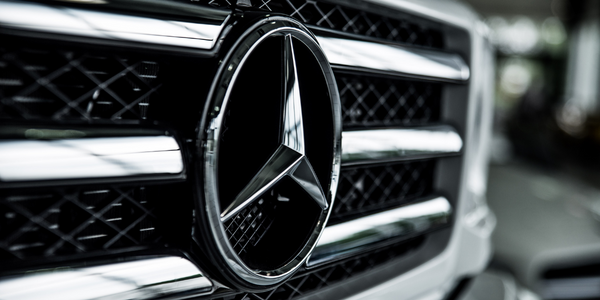
Case Study
Integral Plant Maintenance
Mercedes-Benz and his partner GAZ chose Siemens to be its maintenance partner at a new engine plant in Yaroslavl, Russia. The new plant offers a capacity to manufacture diesel engines for the Russian market, for locally produced Sprinter Classic. In addition to engines for the local market, the Yaroslavl plant will also produce spare parts. Mercedes-Benz Russia and his partner needed a service partner in order to ensure the operation of these lines in a maintenance partnership arrangement. The challenges included coordinating the entire maintenance management operation, in particular inspections, corrective and predictive maintenance activities, and the optimizing spare parts management. Siemens developed a customized maintenance solution that includes all electronic and mechanical maintenance activities (Integral Plant Maintenance).
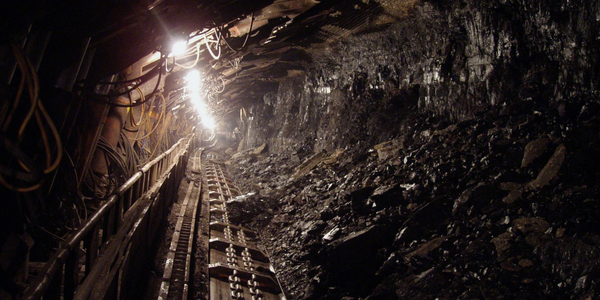
Case Study
Underground Mining Safety
The goal was to produce a safety system to monitor and support underground mining operations; existing systems were either too simple (i.e. phone line) or overly complex and expensive, inhibiting deployment, and providing little-to-no support in event of an accident. Given the dangerous nature of the mining work environment and the strict regulations placed on the industry, the solution would have to comply with Mine Safety and Health Administration (MSHA) regulations. Yet the product needed to allow for simple deployment to truly be a groundbreaking solution - increasing miner safety and changing daily operations for the better.
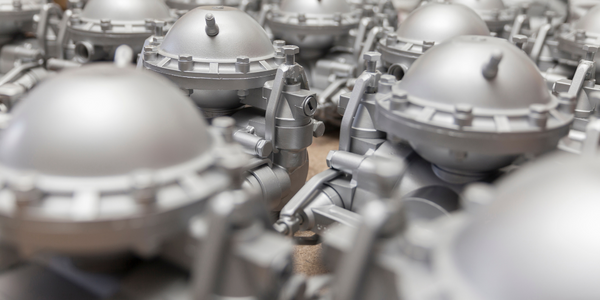
Case Study
Monitoring of Pressure Pumps in Automotive Industry
A large German/American producer of auto parts uses high-pressure pumps to deburr machined parts as a part of its production and quality check process. They decided to monitor these pumps to make sure they work properly and that they can see any indications leading to a potential failure before it affects their process.